Fires, failures and malfunctions: flight simulators allow pilots to train for catastrophic systems failures in both new and existing aircraft. But long before aircraft take to the skies, engineers and pilots invest thousands of hours identifying and resolving potential issues to greatly reduce risk. Before production begins, these teams learn more predictive ways to improve safety and integrate them into aircraft design.
At Boom, this process began with human factor evaluations in our in-house flight simulator two years ago. By starting simulations with the engineering team early, we had the benefit of testing and resolving issues before getting deep into the development life cycle of our demonstrator, XB-1.
Human factor evaluations examine the relationship between pilots and the systems with which they interact, including systems, controls and ergonomics.
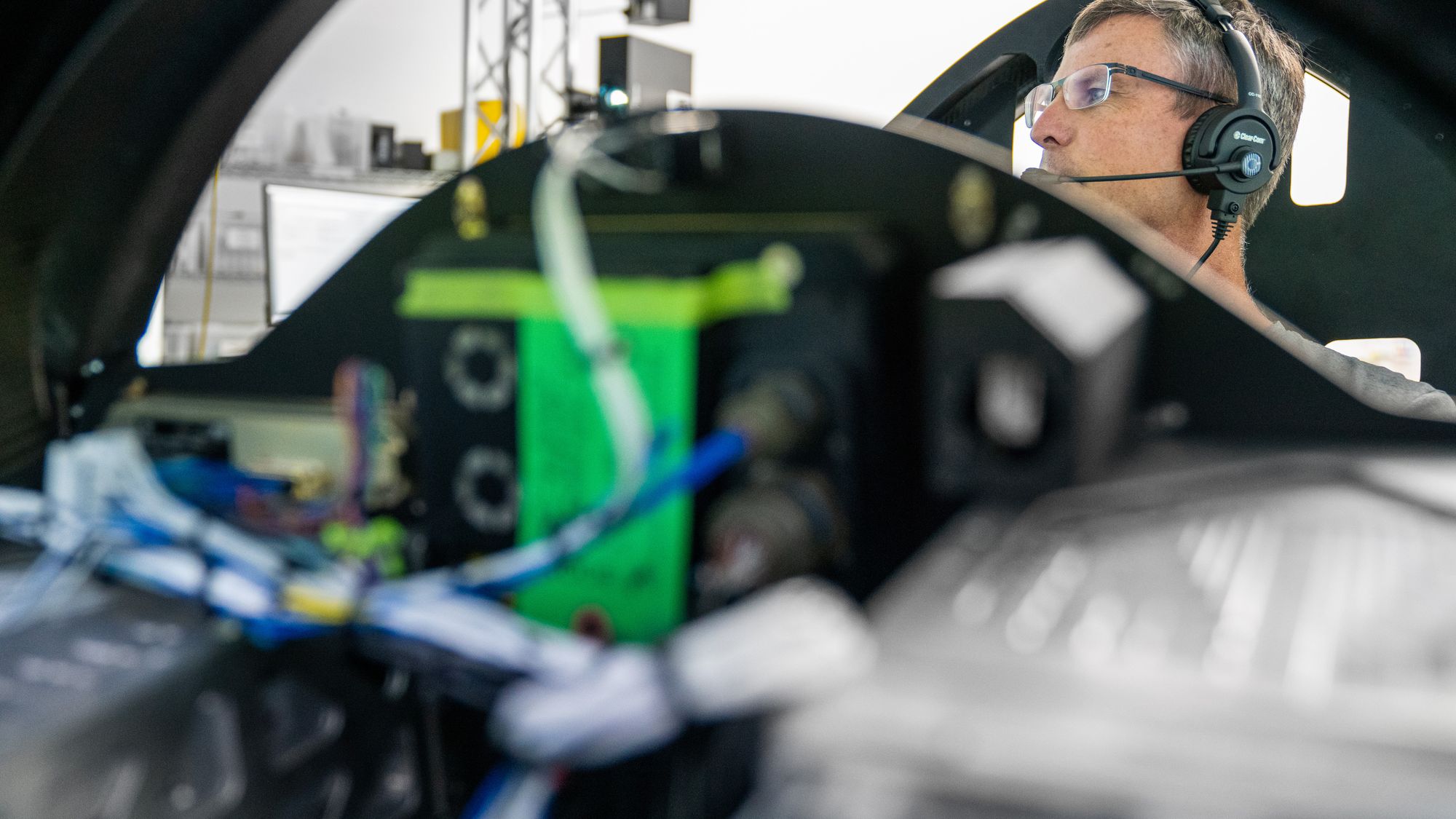
Built in-house, the simulator’s hardware and software are flight-representative: it’s a replica of a real aircraft cockpit. This strong level of realism is equally beneficial to the pilots and the engineering team. At low cost — and minimal risk to the schedule — the engineering team evaluated form, fit and function of all cockpit components, long before integration into the aircraft.
Applying learnings from the simulator, Boom engineers modified nearly all components, achieving multiple design iterations while XB-1 design was still underway. The team has repeatedly simulated operations and emergencies in the environmental control system and pressurization, as well as the hydraulic system, three engines, electrical and avionics systems, flight control failures, and fuel system.
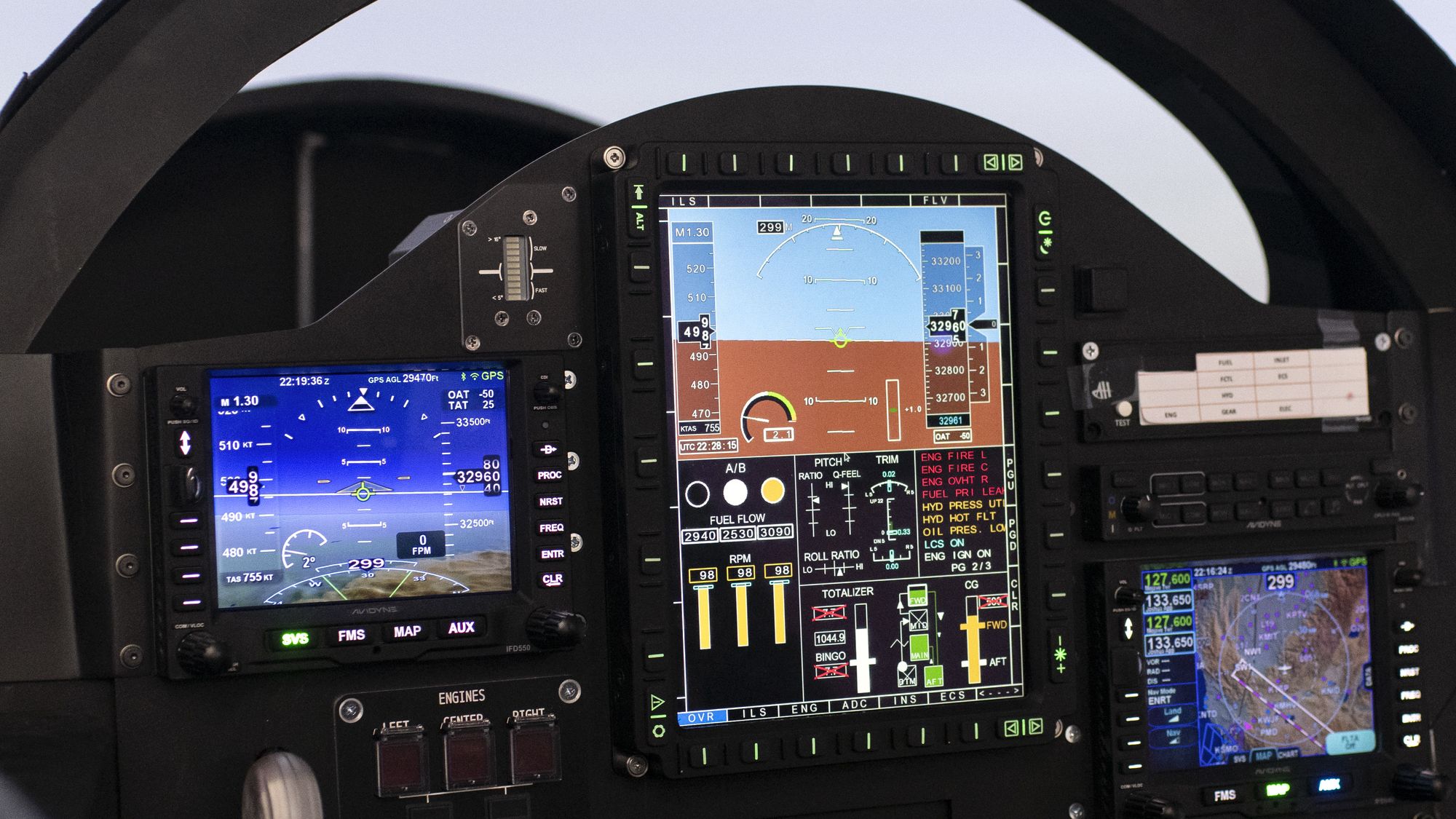
Boom test pilots Bill “Doc” Shoemaker and Chris “Duff” Guarente run simulations daily, but Boom’s simulator is markedly different than simulators used to train and qualify commercial airline pilots today: it incorporates systems for supersonic flight. Take the environmental control system, for example. At supersonic speeds, an aircraft’s exterior could reach temperatures above 300° F, causing heating that typical commercial aircraft don’t need to dissipate. This scenario doesn’t happen in aircraft that only fly subsonically (slower than the speed of sound, Mach 1.0) and isn’t included in typical flight simulators. Boom’s simulator, by contrast, includes supersonic environmental controls so pilots can learn how to manage that system and provide feedback.
Boom’s simulator is markedly different than simulators used to train and qualify commercial airline pilots today: it incorporates systems for supersonic flight.
Flight simulations run the gamut when it comes to emergencies. It’s especially valuable for Boom because the way that pilots will experience challenges in XB-1 — and eventually Overture — will be different from what they’ve trained for in subsonic aircraft. Simulations include the worst of all imaginable scenarios, including dual-engine failure, hydraulic failure(s), rapid depressurization, engine fire(s), engine failure on takeoff, flight control malfunctions, wind shear on takeoff and landing, stall maneuvers, engine-out approaches (landing when you’re down an engine), landing and takeoff with minimum visibility, loss of electrical systems, and loss of instruments/computers.
But simulations aren’t only about learning about what’s not working — engineering teams benefit equally from learning about what’s working, and especially what’s working well. It’s an essential tool in Boom’s approach that establishes safety as an organizational foundation.
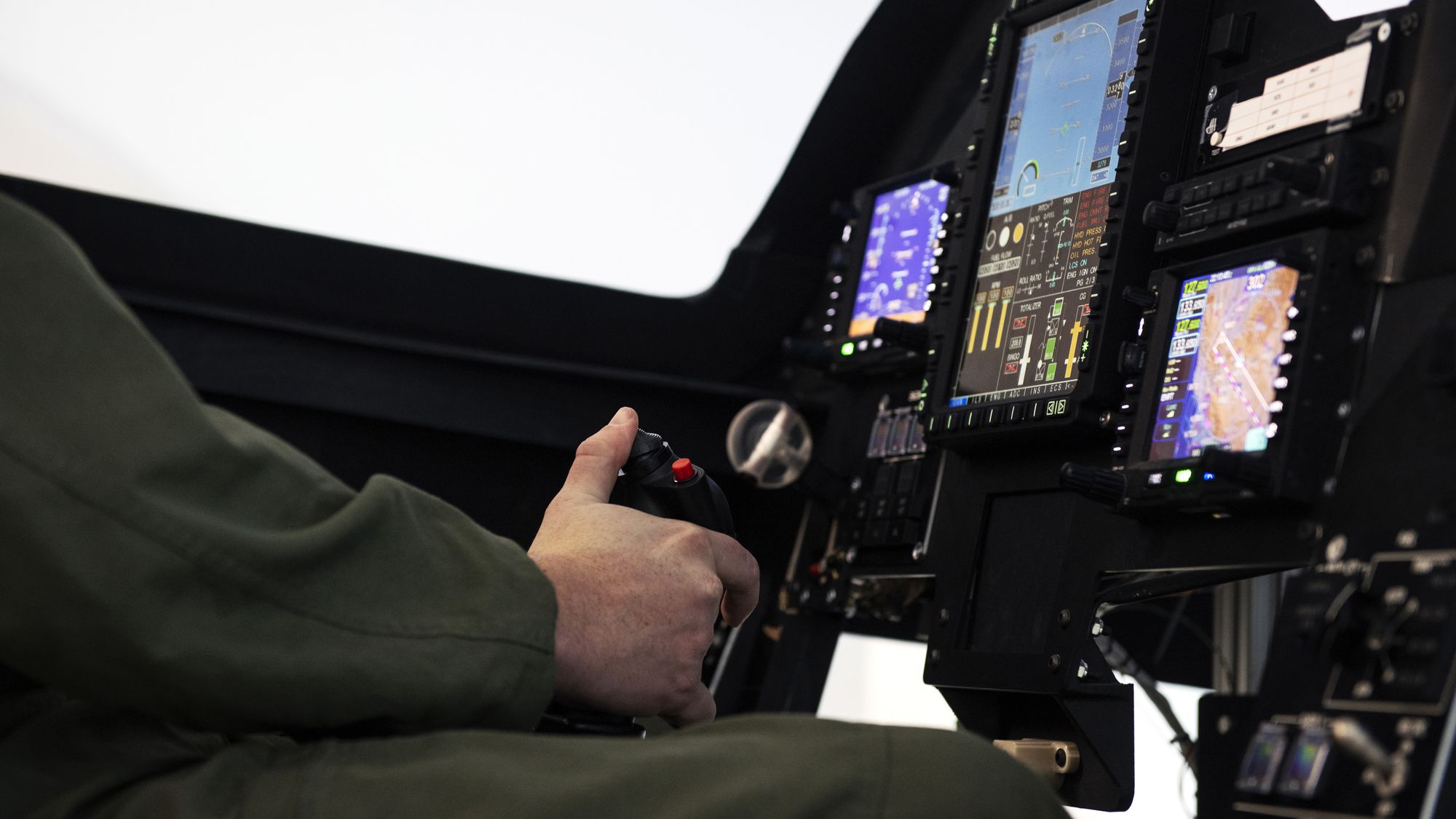
“Among many key learnings, the simulator has already helped us identify modifications that we’re testing further in the simulator and on XB-1,” said Jeff Bozarth, Boom’s Senior Avionics Engineer. “Further simulator evaluations — as the build of XB-1 progresses — are allowing us to directly measure increases or decreases in pilot performance with modifications to the displays and controls. We’ll use these many lessons on Overture to ensure the highest level of safety and pilot proficiency across the supersonic fleet.”
Built 100 percent in the hangar, the simulator is a product of the avionics team, which includes six engineers with experience on certified Level D full motion simulators and simulators for experimental vehicles including SpaceShipTwo and Stratolaunch. The simulator’s only commercial software component is the rendering engine that generates the breathtaking views of Colorado and beyond.
Used primarily as an engineering simulator and training tool for the pilots, Boom’s simulator doesn’t conform to specific levels for simulators because it won’t be certified by the Federal Aviation Authority (FAA). However, it will be used for self-defined pilot training and familiarity requirements that will be submitted to the FAA in order to obtain Letters of Authorization to fly XB-1. A second simulator, which is currently under construction at Boom, will be designed to fulfill future testing requirements.
By bringing the simulator in-house, Boom has reaped benefits in design and production that will eventually transfer to the safety of the end-product. It’s also proven to be our most popular and unusual job perk: a lunchtime supersonic ride above the clouds at 50,000 feet.