As XB-1 nears the end of ground testing before moving to Mojave for flight test, there are a variety of physical tests that must be performed on the ground before the aircraft can be proven safe to fly.
One of the more involved tests is the ground vibration test, or GVT. It’s a unique test during which the aircraft is softly supported. It’s then “excited” by attaching electrodynamic shakers to the aircraft. The “shakers” are similar to a music speaker, but the shaker has a thin rod in place of a cone. On a speaker, a cone pushes air backwards and forwards to create the sound waves, but on a shaker, this cone is replaced by a simple rod to repeatedly impart a small back and forth force onto the aircraft.
This force profile can take a number of shapes but all serve to excite different modes of vibration in the aircraft, and allows analysts to confirm that predicted modes match the tested modes. Vibration modes are the unique shapes a structure will take on when provided with excitation. It is important to have finely tuned models, as these predictions inform flight flutter testing, which is accomplished later during the flight test program.
In the simplest of terms, GVT is completed to ensure the aircraft, once flying, will avoid flutter. Flutter is a dangerous “aeroelastic” phenomenon whereby aircraft structural behavior becomes intertwined with aerodynamics in a way that leads to very large forces that can ultimately lead to structural damage.
We chatted with Eric Gustafson, Loads and Dynamics Engineer, who has been planning for these five days of tests for the last two years. His team is a special branch of Flight Sciences that sits at the intersection of the aerodynamics and structures disciplines to develop and refine external loads (such as flight maneuvering, turbulence, or landing) and evaluate aeroelastic behaviors (the deformation of the vehicle under load and how this loading affects aerodynamics, control, and structural stability).
What is ground vibration testing?
Ground vibration testing validates our understanding of fundamental aircraft behaviors. This includes the modes of vibration, each of which have a resonant frequency, damping, and characteristic shape.
Think of a string on a violin. Characteristics of vibration depend on mass and stiffness. In a sense, ground vibration testing is “playing” the aircraft. We excite it and make it vibrate in different modes, or resonant frequencies, which are measured with sensors. Conceptually, this is similar to how a violinist carries a bow across a string to produce a frequency of sound; a string is perturbed and vibration results.
The behavior of the aircraft in a dynamic sense is driven by modes of vibration. Anything that happens to the aircraft over time can be characterized by modes. For example, when a gust of wind hits the aircraft, its response over time can be characterized by these modes. In the special case of flutter, wing oscillations can begin interacting with the unsteady variation of aerodynamics over the wing. A common example you might’ve heard of which involved aerodynamics interacting with structure is the Tacoma Narrows bridge, where the bridge twisting mode was the cause for the disaster.
We use real world tests to calibrate and validate our theoretical aeroelastic models that are managed by the Loads and Dynamics team. If there are discrepancies between how we thought the aircraft would react when excited and what our models show, we can then make adjustments to the model before taking XB-1 up to 35,000 feet for flight test.
GVT is a way to know how XB-1 will behave in flight from the safety of our hangar. And what we are really trying to avoid here is flutter. The goal in aircraft development is to design a structure that is inherently safe against any tendency to flutter within reasonable limits.
Okay, let’s take a step back, how did you prepare and plan for this test?
Any good plan begins with stating our goals. This separates what is required from what is nice-to-have. Every program wants a fast GVT to minimize the time before the aircraft is declared ready-to-fly. So we do a couple of things for efficient testing, such as developing a clear, organized, and optimized test plan. Since every aircraft program undergoes a GVT, it can be somewhat formulaic, but each aircraft has unique needs, such as the distribution of shaker locations and sensor locations. Finding the optimal location to excite the aircraft (i.e. the same reason you jump off the end of a diving board, not at the base) is important, as is where to measure responses. We can leverage predictive analysis to plan this out.
Writing the plan for a test like this is complex — there are many stakeholders involved in the test that touches on avionics, flight controls, structure, test engineering, and even facilities. Members of this team include the test vendor, manufacturing/ test engineers, flight controls engineers, avionics engineers, and loads and dynamics engineers. These contributors ensure we have the requisite testing equipment, flight hardware, flight software, structural configuration, and even building power, clearance, and equipment to complete the test at our facility.
All in all, we planned for 5 days of testing (including setup), and the test was completed successfully within that window.
Once you have the plan and are ready to execute, how did you hang XB-1 up?
The behaviors assessed with the aircraft aeroelastic model happen, quite obviously, with the aircraft in the air. The goal is therefore to test like we’ll fly. This includes a retracted landing gear state. But that creates a problem, because the gear normally supports aircraft weight on the ground. So to overcome this we decided to support the aircraft from above. Two large gantry frames that are taller than the aircraft served as the means of vertical lift support for the front and back of the aircraft. To minimize the unwanted stiffness provided by the gantry system, which could prevent successful conclusions from being garnered from the test, we isolate the aircraft from it with bungees. The components of this “suspension system” are all tested individually prior to GVT because of the dangers associated with lifting such a mass off the ground.
Overture will be a much larger aircraft than XB-1. When an airliner of this size is ready for GVT, engineers will employ a support system such as airbags placed underneath it to replicate flight and could have twice as many sensors and shaker locations as XB-1. As with XB-1, this will be an exciting time during the Overture program, as the flight test aircraft will be very close to first flight. And as a certified program, all Overture testing will be increasingly comprehensive.
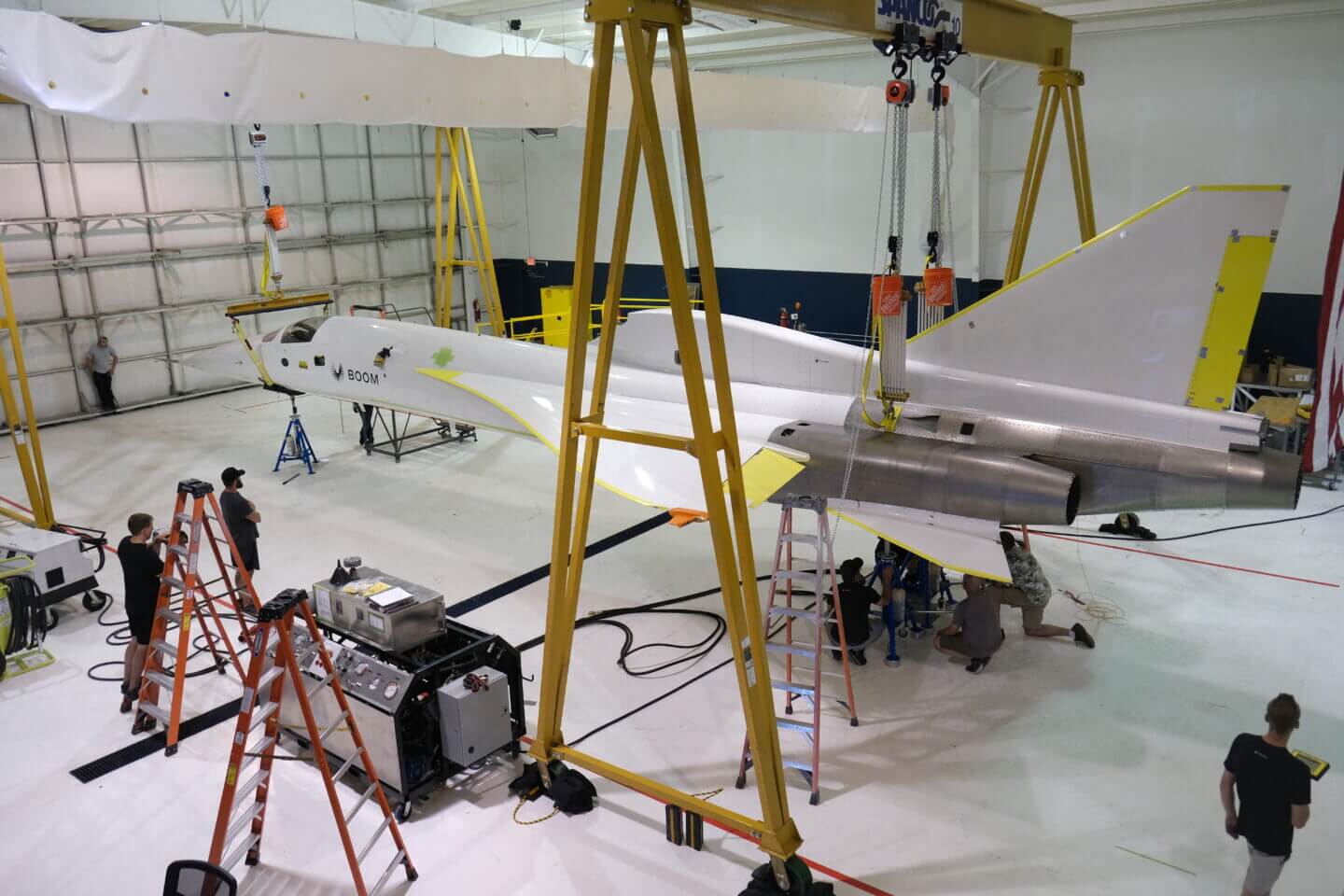
What are the different modes of vibration you’re testing?
Strictly speaking, any physical object can have an infinite number of vibration modes, but the first couple of modes with the lowest frequencies are often the most important. Each mode contributes in some part to the overall response of the aircraft’s motion, but it is difficult to characterize this all at once. Instead, we excite the modes at specific frequencies to uncover behaviors of each mode individually. In the case of XB-1, there are only about 30-40 modes that we care about. This includes fuselage bending, wing bending, wing torsion (twist), control surface rotation modes, and the like. The relationship of these modes to one another is important. For example, if certain mode frequencies are close, they can lead to unwanted interactions.
What is the next step for XB-1 related to GVT?
We enter into the model correlation phase where we update our theoretical aeroelastic model to match the behavior of the as-tested aircraft. Following this correlation phase, it is understood that the model, with minor changes, can also represent aircraft configurations that weren’t tested on the ground. This permits final flight predictions that give us the evidence we need to unlock XB-1 from getting in the air and accomplishing its mission – supersonic flight!
Learn more about XB-1’s ground testing program here.