It’s one of the most exciting milestones of XB-1’s build to date: the successful bonding of XB-1’s cockpit and nose landing gear into the fuselage. Accomplished in late 2019, it brings Boom’s demonstrator aircraft closer to first flight.
Bonding is as straightforward as it sounds — it’s the joining together of aircraft parts. But, the process is far from simple.
Preparation began two months prior with detailed planning, staging, and three dress rehearsals. Several members of the team played a central role while others supported the effort during key moments. Drawing from engineering, analysis, manufacturing, the shop floor, and even the HR department, the team assembled on December 19 to get started.
The event spanned more than 20 hours, beginning with a very early morning grit blast.
3 a.m.
Work gets underway outside the Boom hangar with a grit blast to remove surface contaminants (particles of dust and dirt). The four-hour process begins under the cover of night and ends under a beautiful Colorado sunrise. It’s time to move the work indoors.
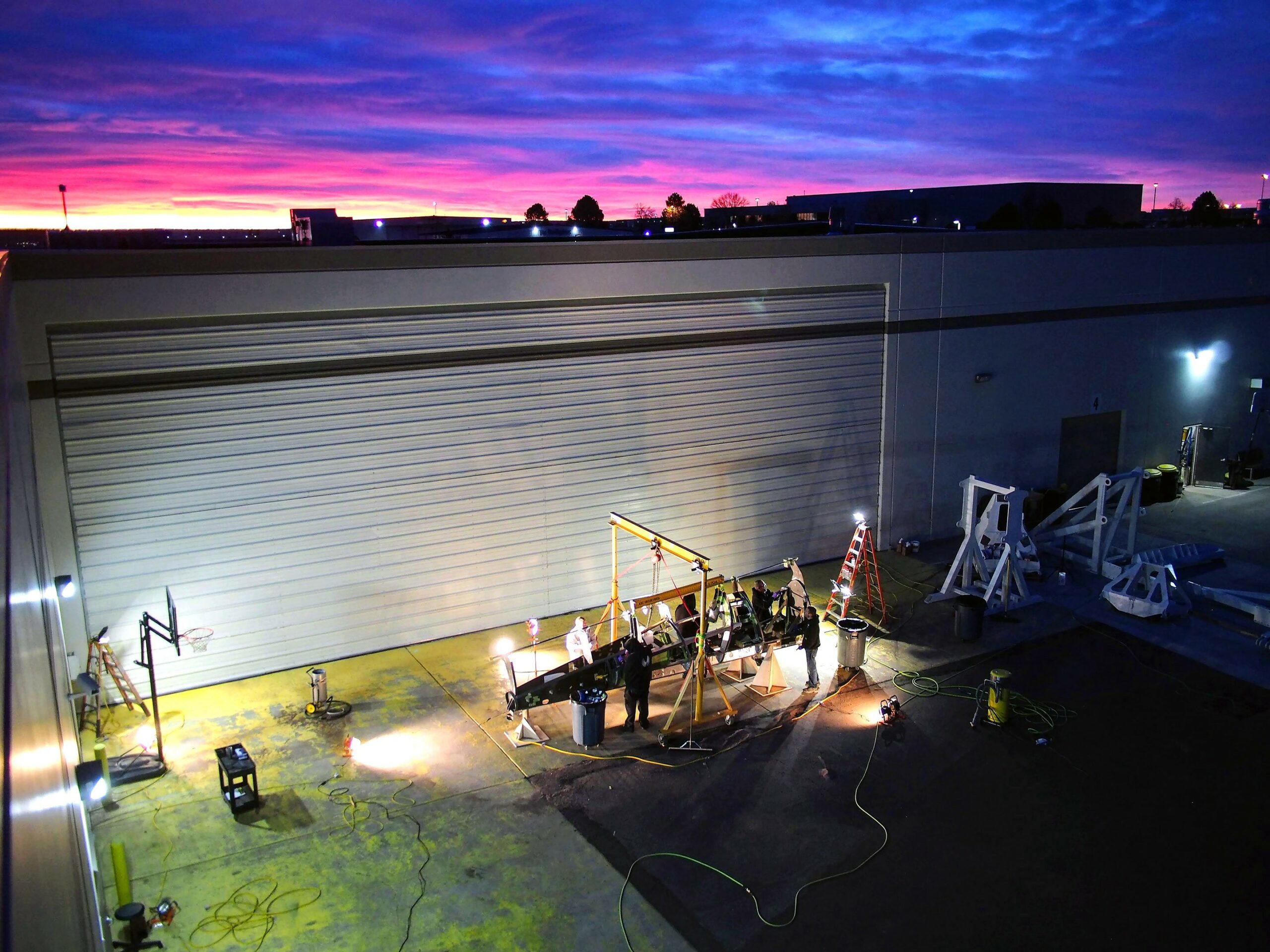
7 a.m.
Team members start cleaning. The team removes all masking tape, vacuums leftover sand, and cleans the surface with acetone and isopropyl (alcohol). Previous dress rehearsals prepared the team to work together in parallel.
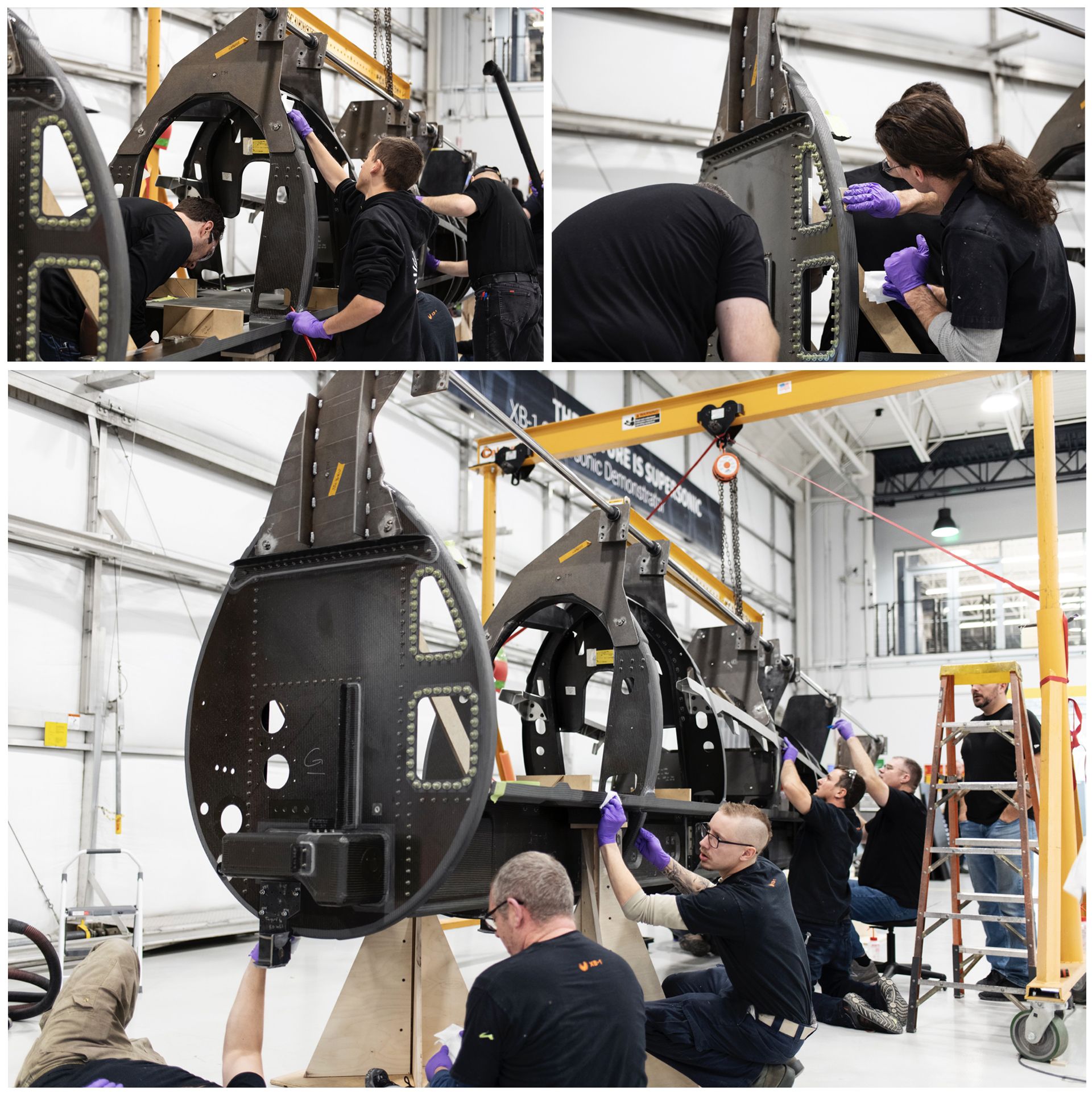
8 a.m.
The team positions the cockpit and nose landing gear in place. At close to 300 pounds, the cockpit requires a synchronized effort to move into the correct position. When all required tooling is added, it weighs a considerable 900 pounds. The team seamlessly positions it using a shop gantry crane. At the same time, several team members shift their focus to mixing and preparing bonding adhesive.
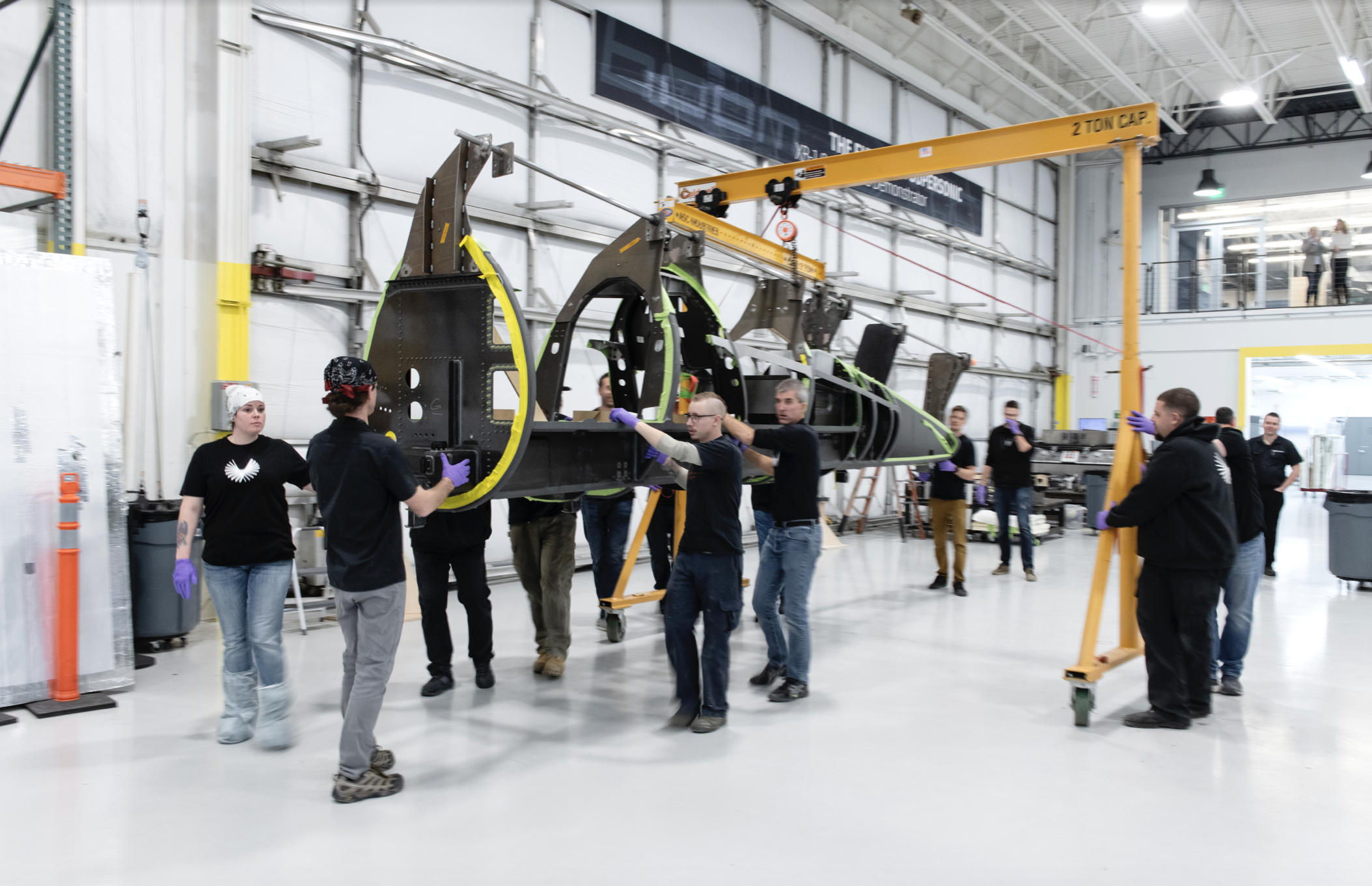
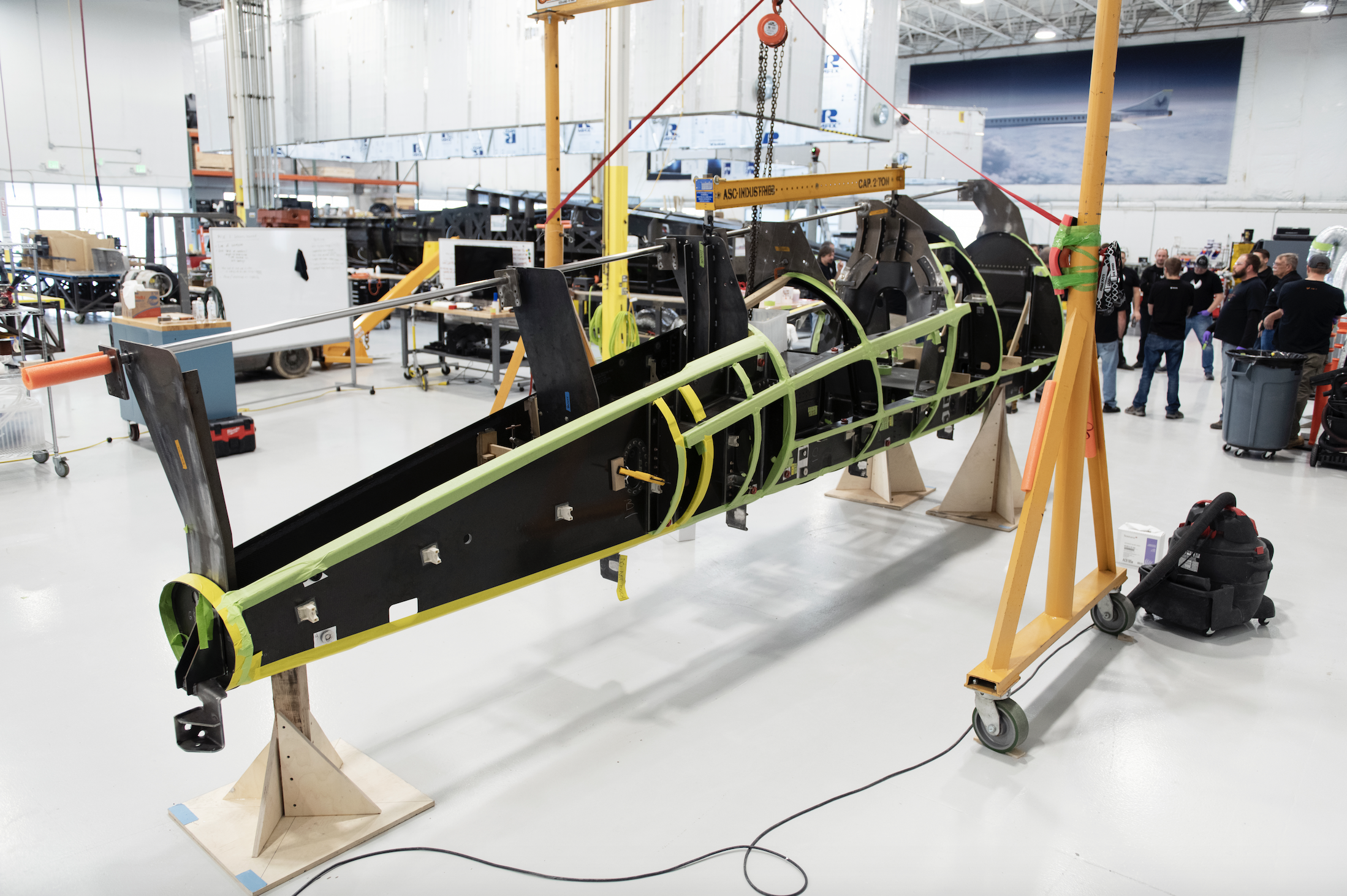
11 a.m.
The event is on schedule. The team begins the application of bonding adhesive. It’s an orchestrated effort — close to 20 team members simultaneously apply adhesive. Time is of the essence. The aircraft components must be aligned and attached within a relatively short window of five hours to prevent the adhesive from drying too soon.
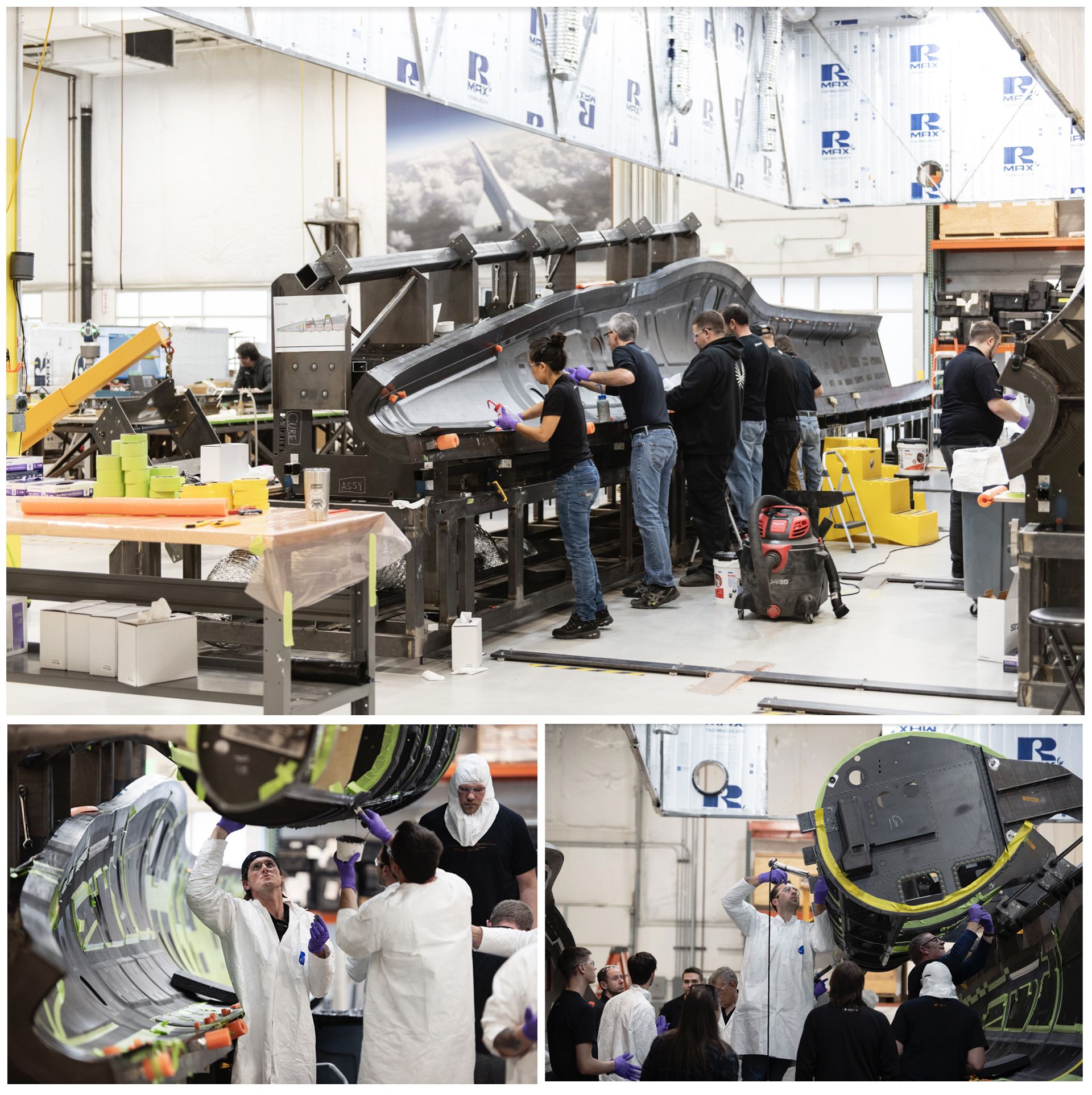
1:45 p.m.
The fillet process gets underway as the cockpit and nose landing gear are joined with the fuselage. Enough adhesive is applied before pushing the parts together that there is considerable “squeeze out” as the compressed adhesive squeezes out on either side of the part. Team members work together to clean the squeeze out by filleting. The process consists of running a tongue depressor along the squeeze out to clean up the adhesive and create a neat fillet.
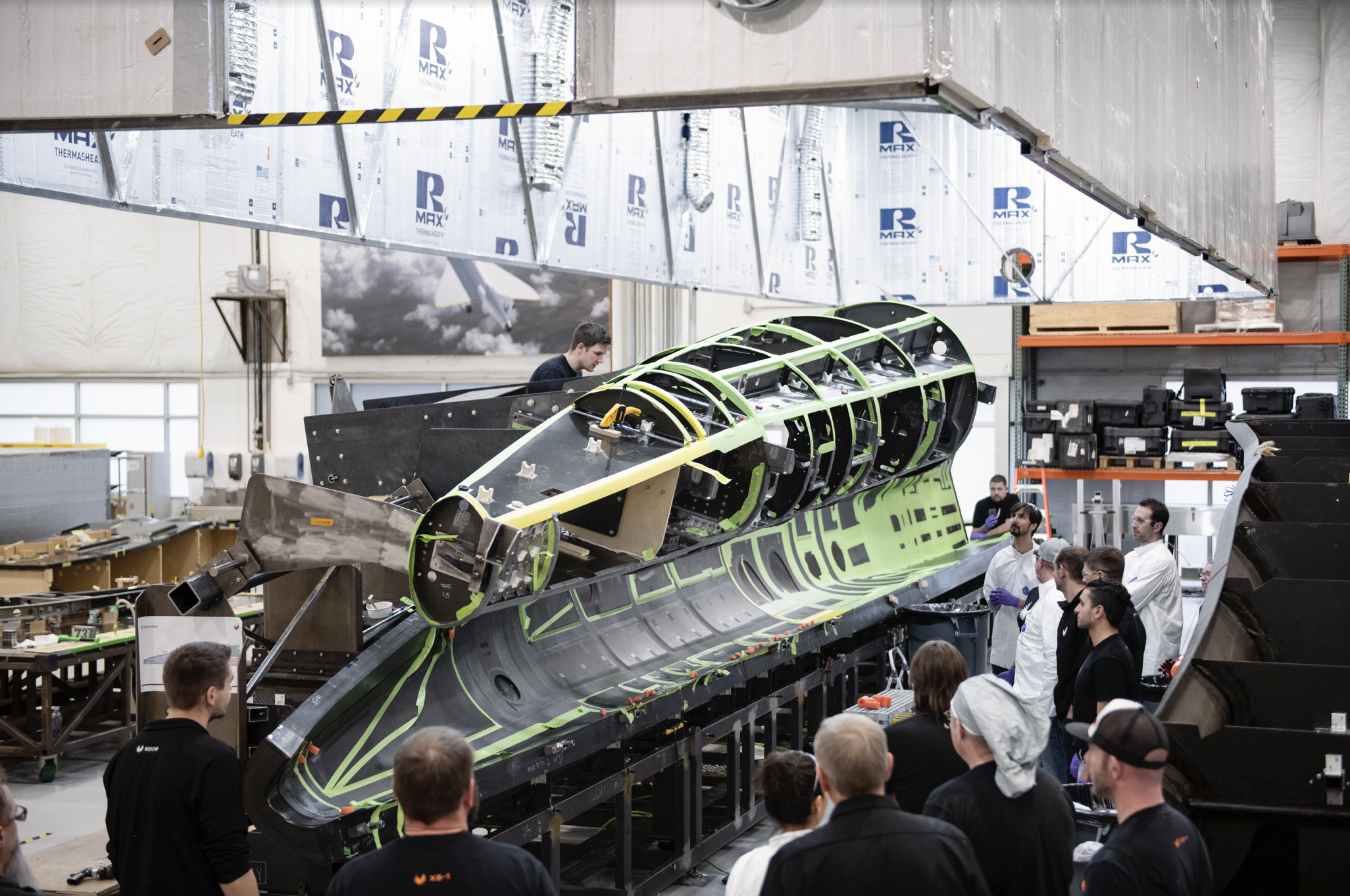
4:45 pm.
Inspections and checks follow to ensure exact positioning of the cockpit and nose landing gear. The metrology team uses laser trackers to check various points on each part and compares measurements to where the parts should be in CAD (Computer-Aided Design).
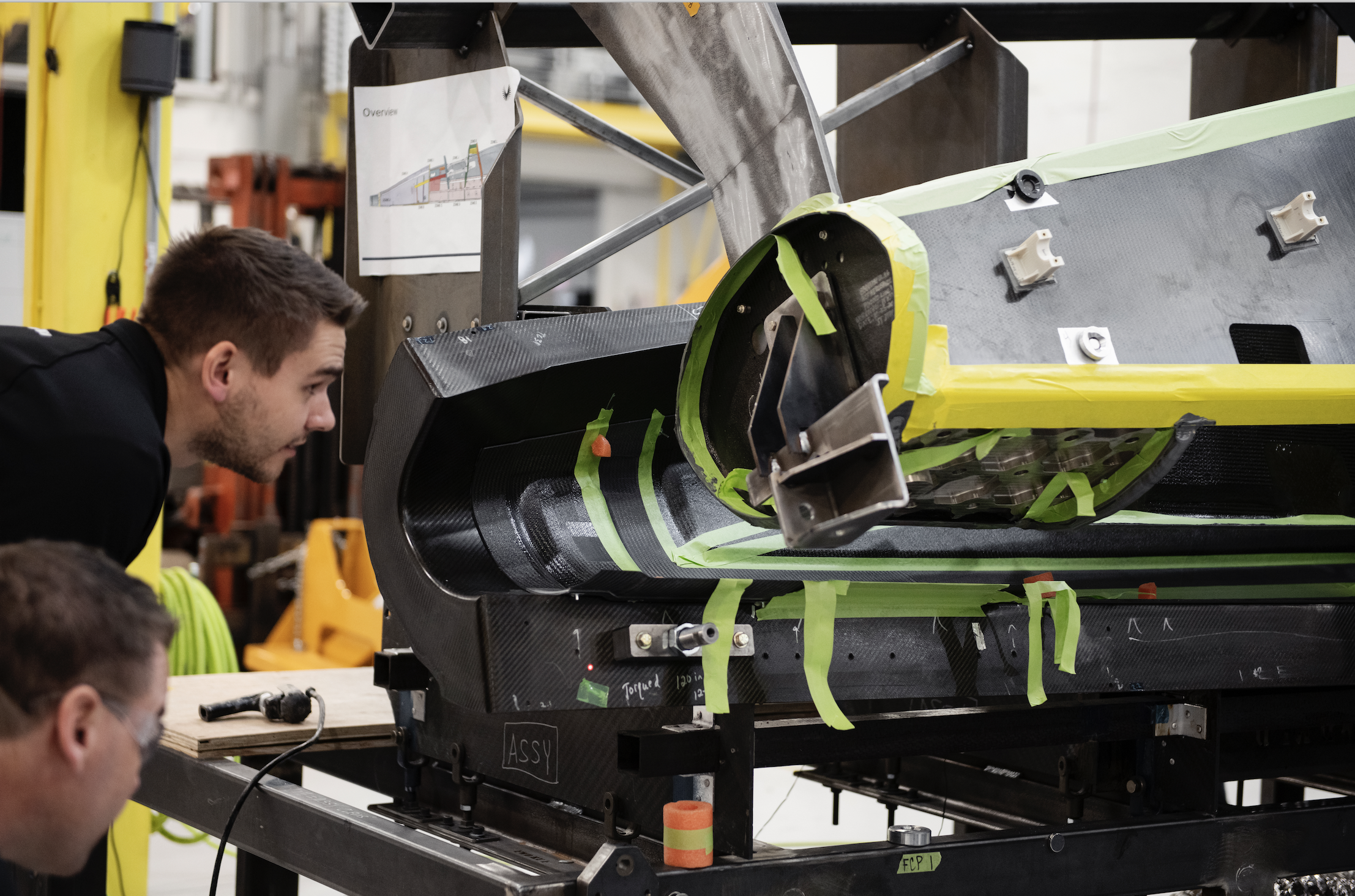
5:15 pm.
XB-1’s cockpit and nose landing gear are ready for curing, which requires more than 5 hours. The oven needs 2.5 hours to heat to the required temperature and XB-1 will take an additional 2.5 hours to cure.
It’s now past 10 pm and most team members have left for the day, but several remain behind to confirm that everything is running smoothly.
11:15 pm
The team verifies that curing is complete and that the process is complete.
The following morning
It’s the following morning and bonding appears to be successful, but it’s essential to confirm that the bond lines are shaped correctly or “filleted.” A member of the engineering team, who is certified in the process, begins non-destructive tap testing to audibly listen for voids such as air bubbles within the bond. With several decades experience, he knows what to listen for. Using specialized tools, he taps all bond lines and listens for different and unusual noises. He confirms that bonding is a success.
As the team celebrates this milestone, they look ahead to upcoming bonding events to apply what they’ve learned to the next phase of the XB-1 build.
Did you know? Bonding is not a new manufacturing method in the aviation industry. Many of the first aircraft were glued — bonded — together.