Nearly two weeks after the Boom’s non-essential employees began working from home, the company’s testing facility continued to hum with the sound of progress. A small, essential team of socially-distant engineers and technicians began the three-day task of conducting XB-1 wing static load testing. The tests, upon successful completion, would verify wing design and officially approve the structure safe for flight.
As the project lead, Boom’s mechanical engineer Nate Hepler led execution on the ground, while Chief Test Pilot Bill Shoemaker relayed updates to remote employees via Slack. Minute-to-minute updates quickly became a source of excitement and connection to the action.
“This is a big milestone for the program that will put significant uncertainty in the rearview mirror,” Chief Test Pilot Bill Shoemaker began in a company-wide message. “At the end of this process, we’ll be confident that the wing will stand up to any forces it might experience in flight.”
Hepler explained the process in pre-brief:
“As part of the test, we’re simulating the forces acting on the wing when XB-1 is flying at its limit load factor. An array of 26 hydraulic actuators will be positioned up against the structure, each exerting a different force to mimic the distribution of pressure from flight. We will be testing up through its highest load case of 60,000 pounds of force.”
After final preparations, upward wing testing began.
The event was a nail-biter, even through the written medium.“Loading at 5%, down to 0%, up to 10%,” Shoemaker reported live, with photos included.
“This is like ‘watching’ a baseball game via telegraph,” Boom’s Landing Gear Engineer Adam Vaccaro responded. “Nerdiest sport ever,” added Erin Young, Mechanical Systems Lead.
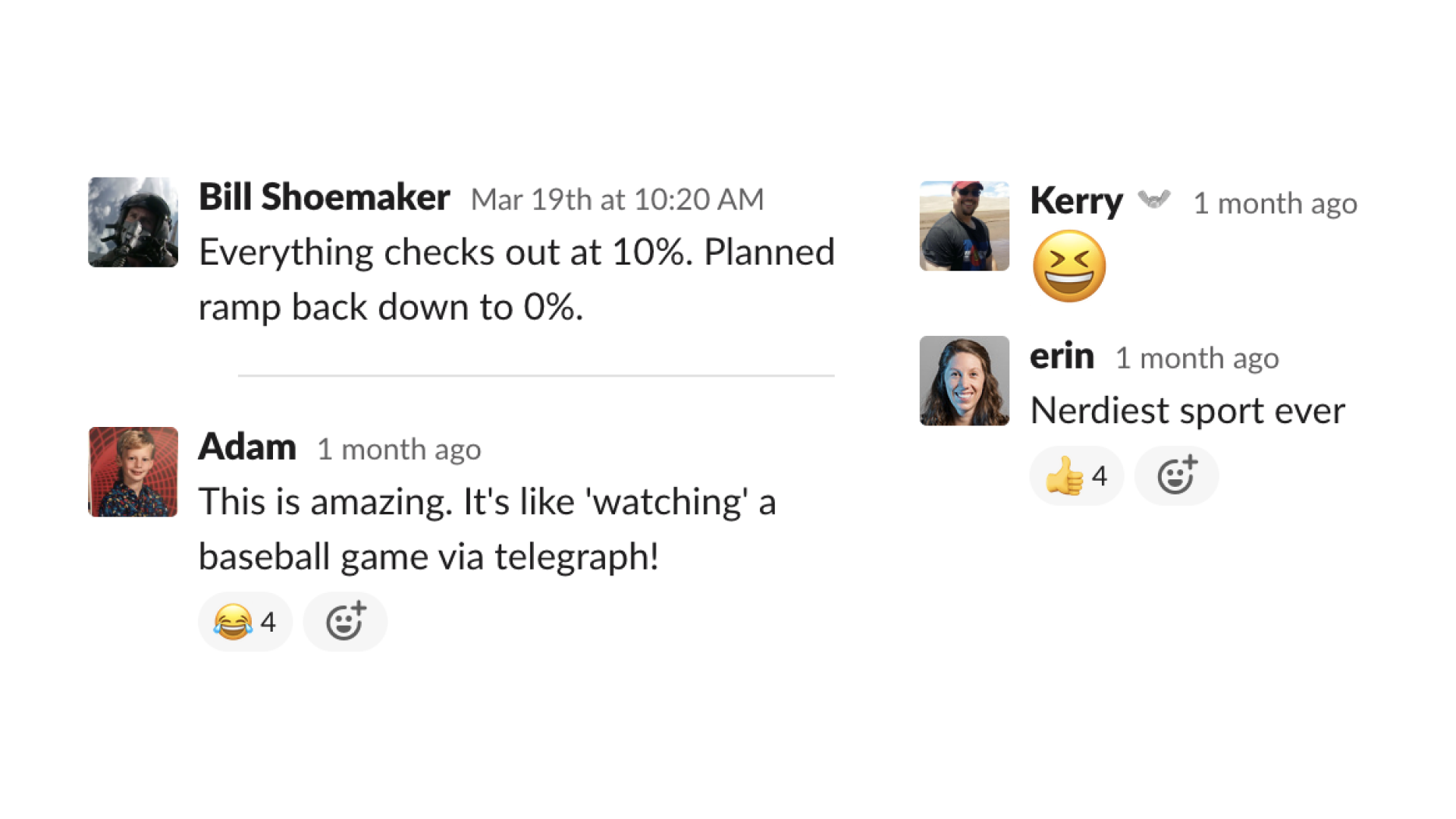
The commentary continued through each phase of testing, as the load increased from 10%, to 20%, and 40%.
“As the load is applied, the team is continually measuring the wing’s deflection and strain at various locations, and comparing that measurement against predictions,” said Shoemaker. “They’re also constantly checking for noises. Some noises are normal when a composite structure is loaded and others are not. The wing has been instrumented with an array of acoustic sensors specifically for this purpose.”
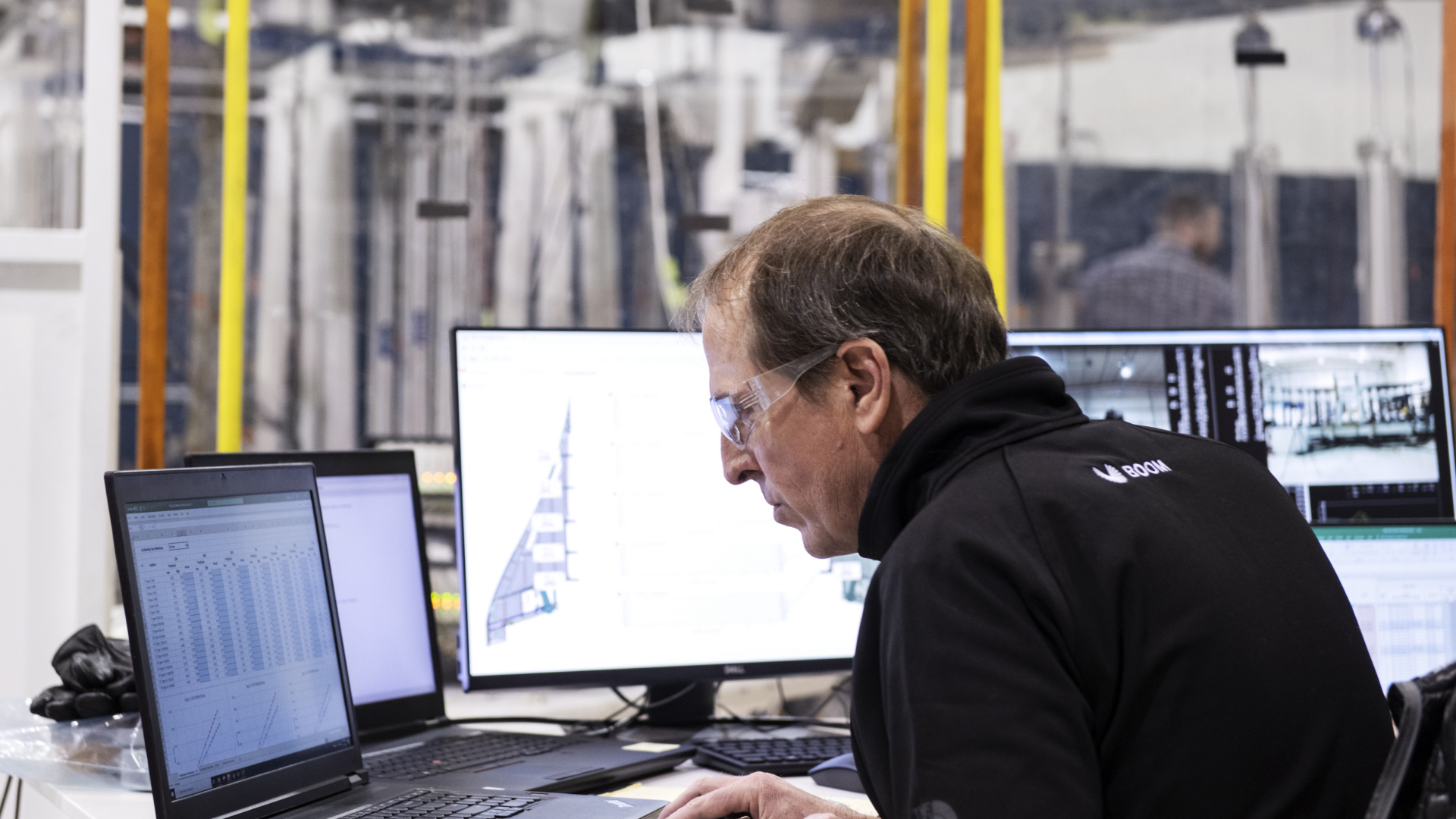
March 20th, 2020: After significant data review, the team resumed progress the following day.
“The team is repeating the 40% case before moving on to 60% to verify results from yesterday,” shared Shoemaker. “We do this testing incrementally for a reason. As the structure is loaded into new territory, we expect that its properties will change by a small amount. We gain insight into the health of the structure by seeing the differences in strain, displacement, and noise during the second loading.”
By late in the afternoon, the excitement was once again palpable.
Shoemaker:
“Loading to 100%.
Increasing through 30%
50%
70%
90%
95%.
Holding at 100%.”
The team repeated the process once more for verification and then released the wing from the testing structure.
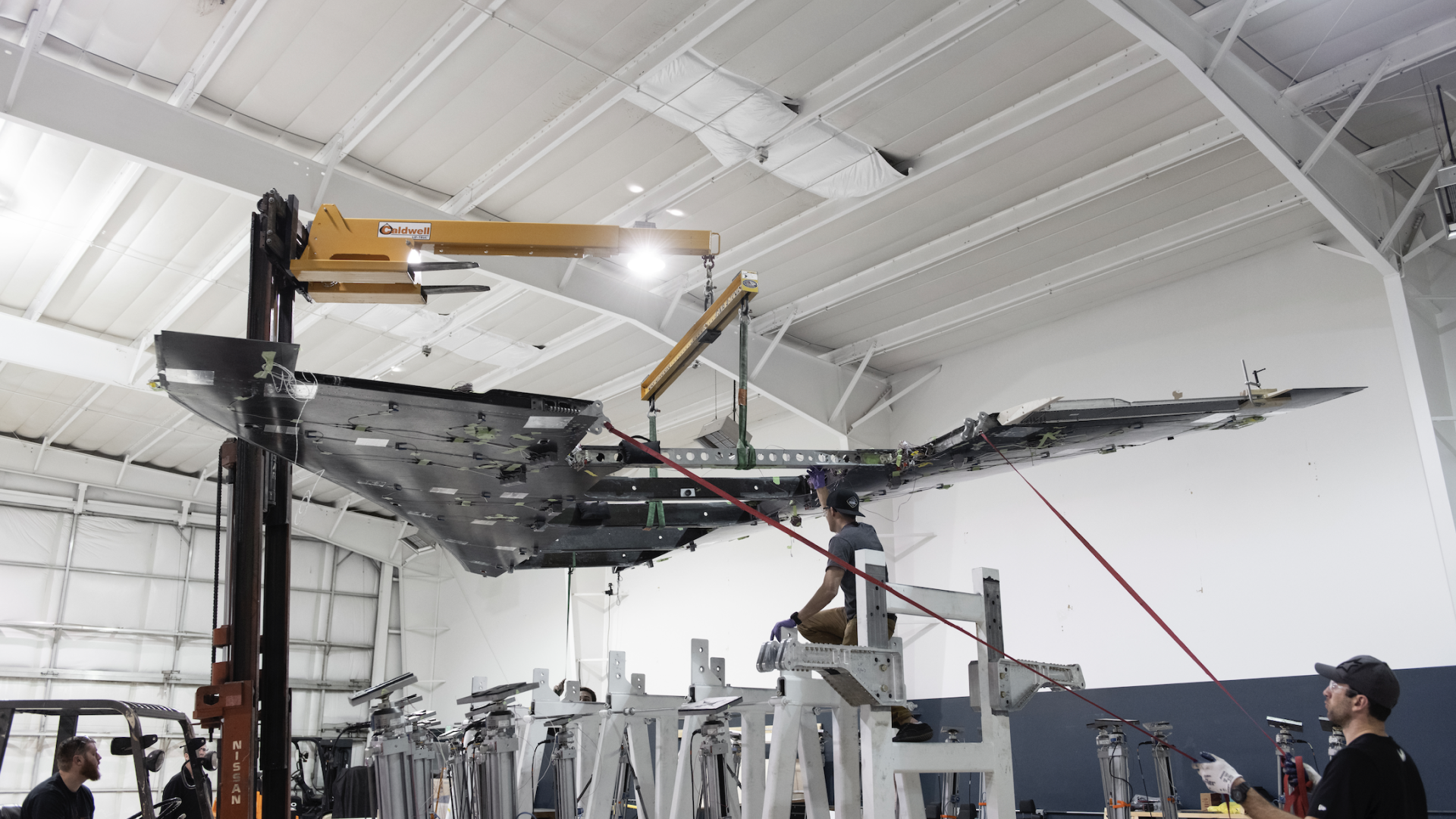
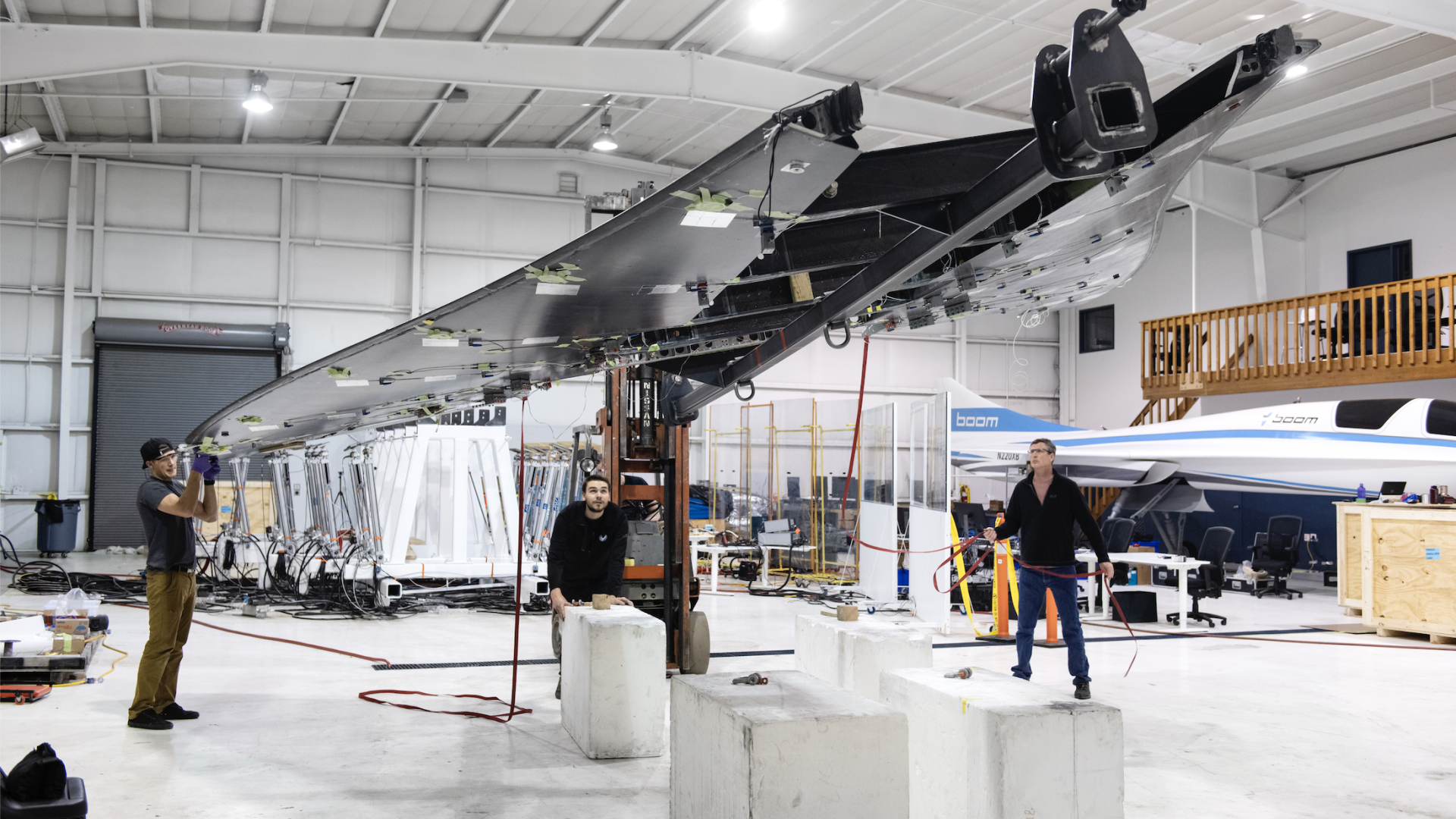
“The team successfully cleared the wing for 3.8Gs in upright flight,” announced Shoemaker. “Tomorrow, we flip the wing over for the ‘down’ bend tests, which will clear XB-1 for [negative] 1.5Gs.”
March 21st, 2020: The wing structure was carefully rotated and the 26 actuators were repositioned against the upper wing skin, as part of preparation for ‘down’ bend tests.
After set up, briefing, and inspection of the rig, the loading cases began again.
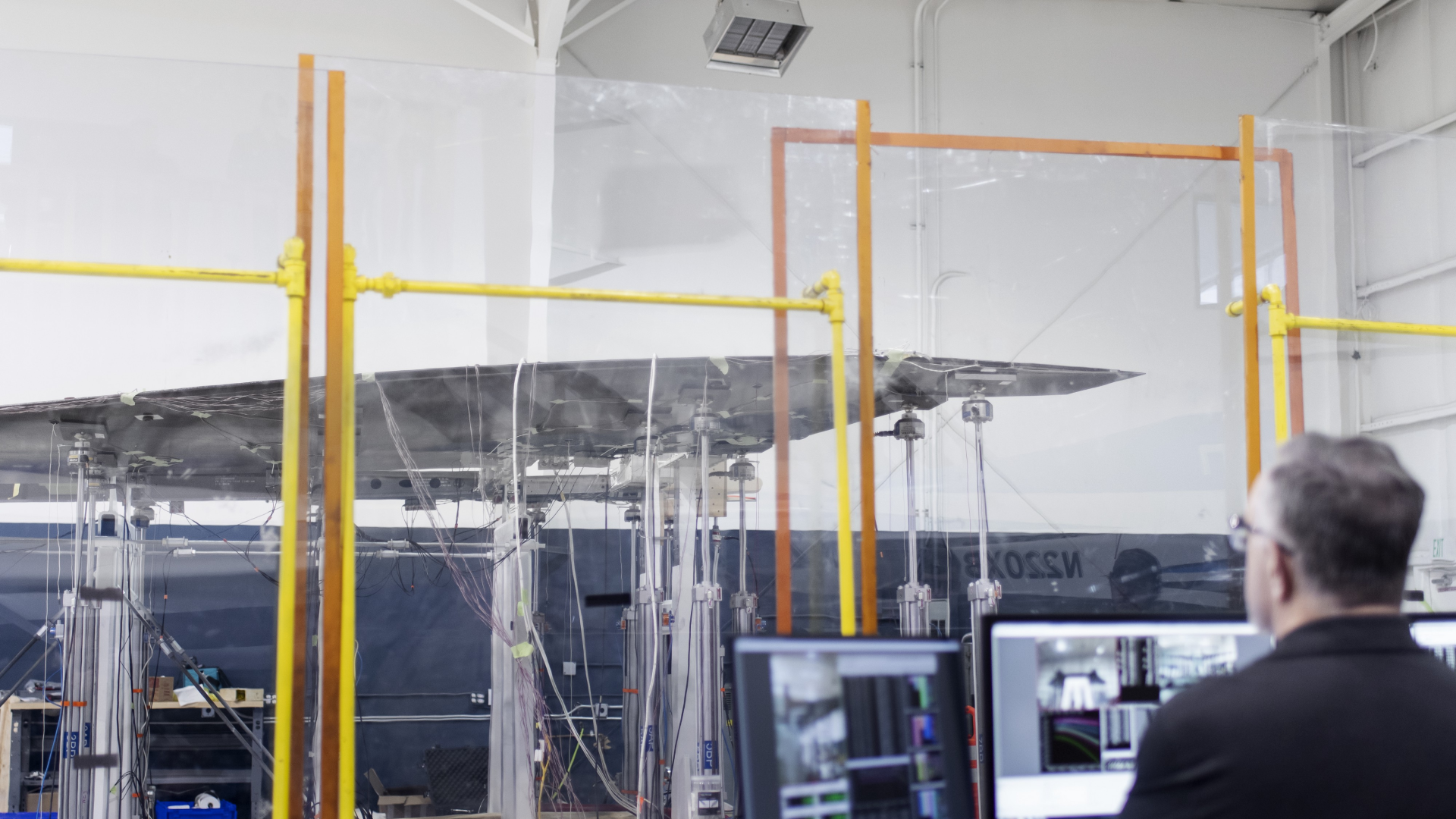
With trained efficiency and focus, the team increased load cases from 40%, to 60%, then 70%, continuing at increments of 5% at a time until conducting two 100% load cases. “Strains and deflections continue to track well against predictions,” Shoemaker shared live.
With the entire company once again at the edge of their seats, testing at last reached its final stage.
Shoemaker:
“Holding at 100% for aileron sweep.
Sweep in progress.
Full down.
Full up.
Sweep complete.
Holding at 20% for data review.
Static wing test objectives complete!”
Emojis replaced audible applause, but thanks to the terse commentary, the event had truly come to life.
With that, a critical milestone concluded for the XB-1 program. “This was undoubtedly a high-risk event,” said Shoemaker. “And now, a major risk element is safely in the rearview mirror for us. Great job by the team getting this done safely and professionally!”
The total event spanned from 8 A.M Thursday and concluded at 12:30 P.M. Saturday.