Simulated flights for Boom’s supersonic demonstrator, XB-1, recently became much more realistic.
With the completion of Boom’s second generation in-house simulator, teams from Avionics, Flight Controls, and Flight Test have significantly advanced progress to XB-1’s test program.
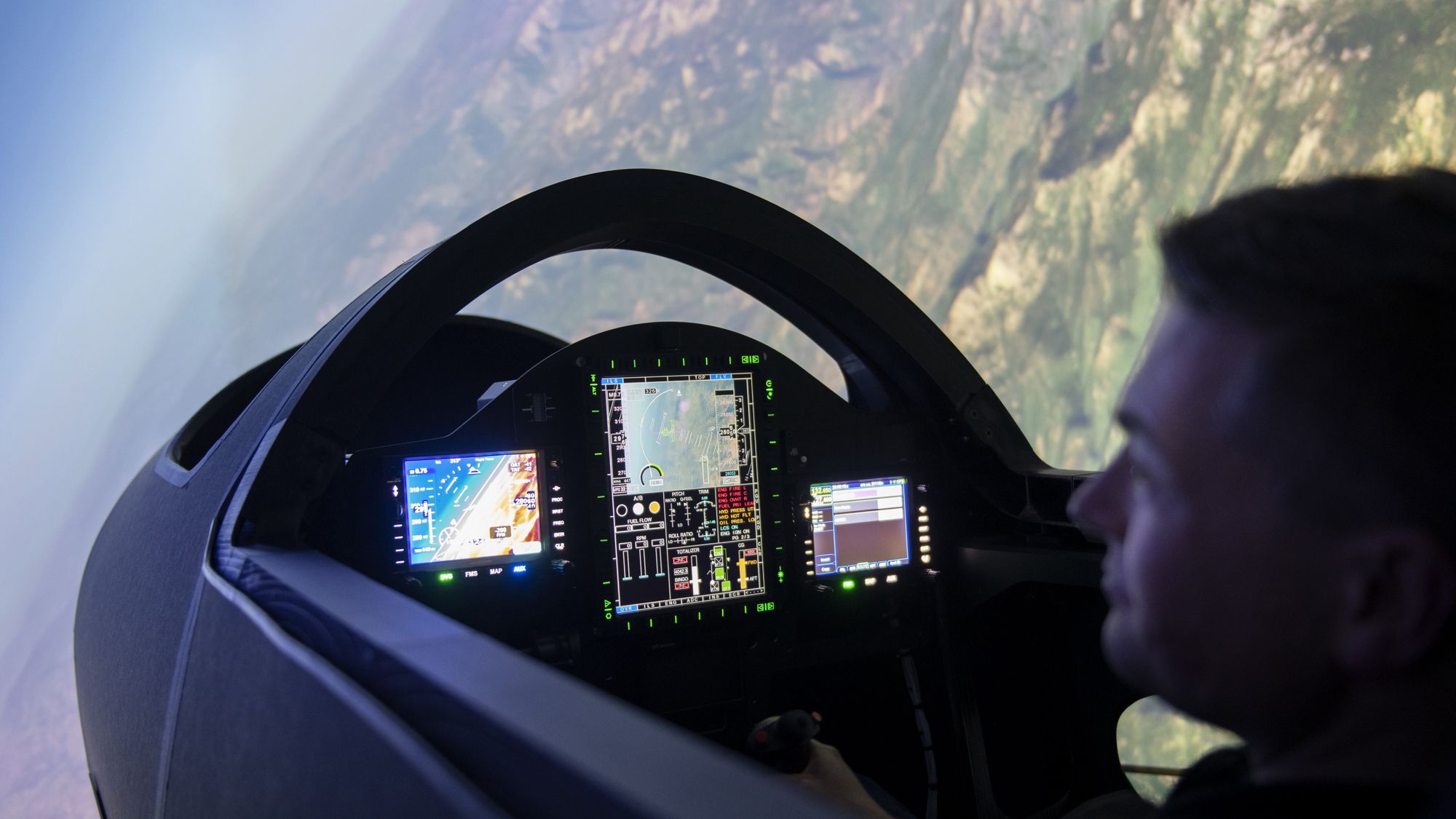
The project, led by mechanical engineer Ryan McKay, eliminated significant risk for the flight test program While Boom’s first simulator served as a critical tool for human factor evaluations, this second iteration provides confidence in flight control system design and serves to burn down design risk through frequent pilot evaluations.
“Boom’s second simulator provides much higher mechanical accuracy in representation of the aircraft flight controls than previous iterations,” said Chief Flight Test Engineer Jeff Mabry. “It not only allows us to finalize the design of the aircraft’s flight controls, but also enables training for both our pilots and control room team with full mission rehearsals.”
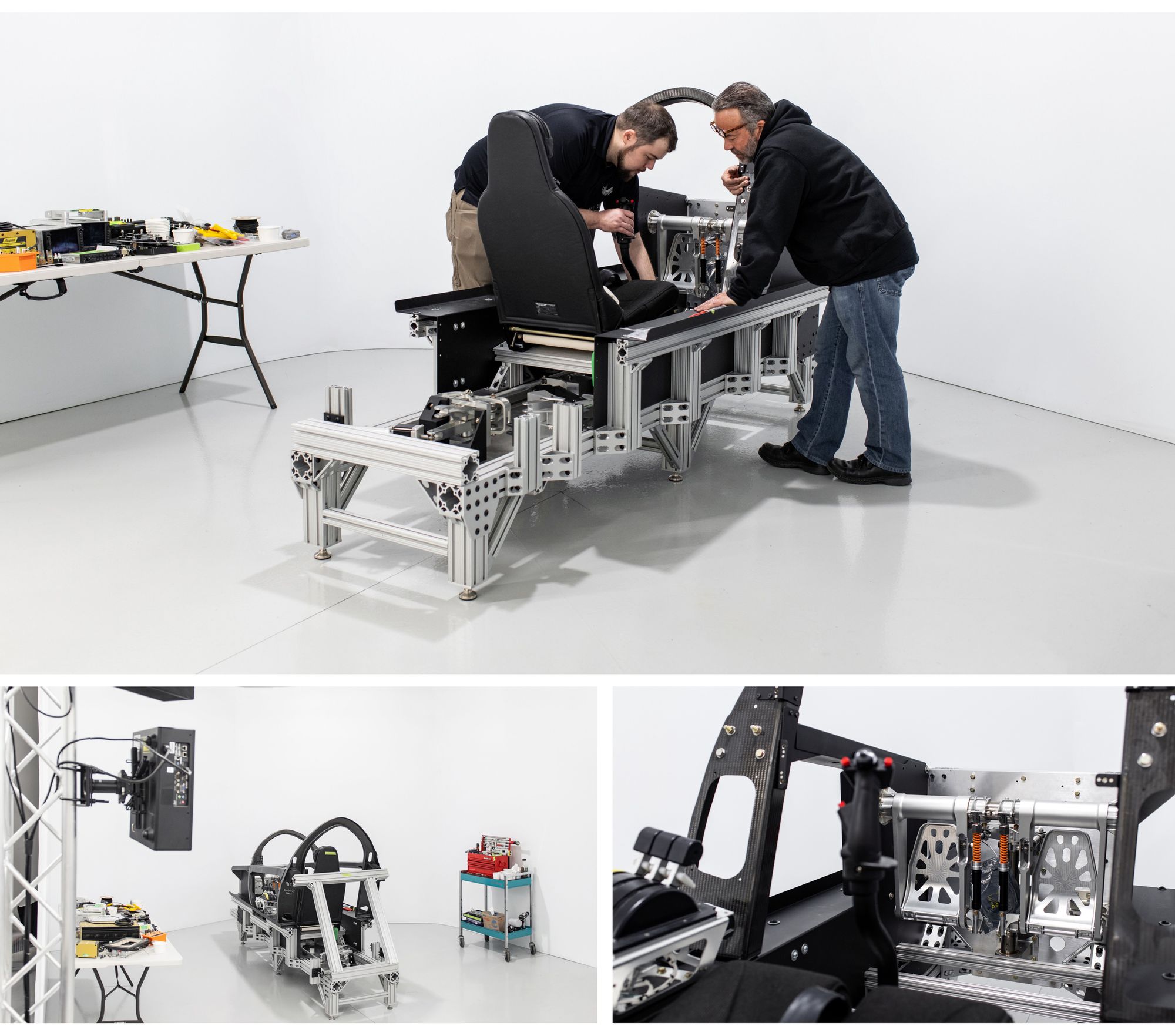
Delivered on schedule and aligned with the flight test program, the team immediately put the simulator to work. “Just a week after it’s completion, we had already placed three different pilots in the simulator to evaluate multiple combinations of stick feel and responsiveness,” said Mabry. “Refining the design with direct real-time feedback like this allows us to finalize the system to both meet specifications and produce the best feel for the pilot during all phases of flight.”
“This second simulator is just one example of how we incorporate risk reduction and safety into the design of an aircraft as early as possible,” said Mabry.
Along with increased cockpit fidelity, some key features of the simulator include the addition of virtual hydraulic actuators, a wind gust model and flight-like mechanical systems.
“The second generation simulator is essentially a slice out of the real airplane,” said Project Lead Ryan McKay. “We replicated the cockpit and mechanical systems as closely as possible. We’re anticipating that the pilots will put many more flying hours into the sim than the actual plane.”
Keeping smart and efficient through the project, the team leveraged Boom’s in-house 3D printer to fabricate the most realistic cockpit possible. “For even more efficiency, we reused a significant number of parts from the first simulator as well,” said McKay, “and optimized what was already available.”
Looking forward, the second simulator will play a critical role in mission rehearsals for XB-1. “We have this simulator in our Colorado hangar now, and will have an identical unit at our base in Mojave as we embark on flight test,” said Mabry. “During mission rehearsals, we will be able to mirror every part of the flight profile. Our pilot will be on a headset speaking with our control room in Colorado, effectively training the 20 or so people that will be sitting in the control room during the flight test program. By the time the actual first flight comes around, the team will function like a well-oiled machine, since it will have rehearsed flight so many times. In flight testing, we like to say that a good first flight is boring — the team is so well prepared that there is nothing that can surprise them. Having tools like the new simulator is the perfect way to do that.”