Erin Young regards flight test as a delicate balance of safety and efficiency. As Boom Supersonic’s Senior Manager of Aircraft Systems, Young is among the original team members leading the flight test program for XB-1, the company’s supersonic demonstrator jet. She has been involved in the aircraft’s development since its inception.
Safety and efficiency are the core of the XB-1 flight test program currently underway at Mojave Air & Space Port in Mojave, CA. While the ultimate goal is achieving supersonic speed, it also lays the foundation for a flight test program for Boom’s commercial jet, Overture. Learnings, best practices, and, most importantly, the company’s safety culture, will be carried forward to Overture.
Young stresses that the XB-1 flight test program is unlike any other. Not only is XB-1 the first independently developed supersonic aircraft in aviation history, but it’s made almost entirely from advanced carbon fiber composite materials, has an augmented reality vision system, and is the forerunner to a commercial supersonic passenger aircraft.
The XB-1 program also has some surprises.
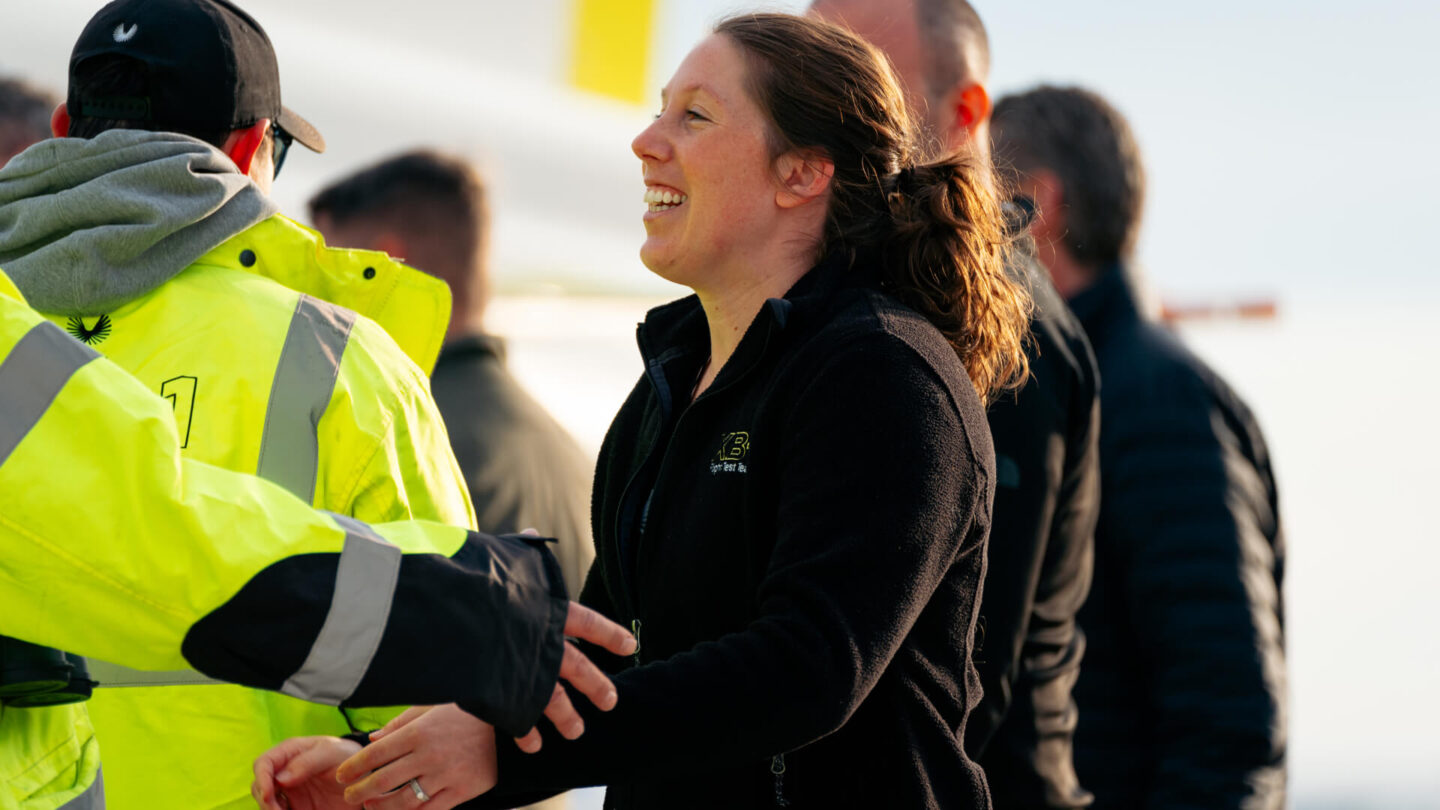
Decreasing and increasing levels of risk
“You might imagine that a successful flight test program involves flying as many hours as possible, but the opposite is true,” says Young. “Each test flight has high risk, and our role is to manage and limit that risk. We do that by minimizing the number of flights and flying time while maximizing the scientific data gathered during each flight. We aim to safely accomplish our goals in shorter, more efficient flights.”
Another aspect of flight test might surprise you—the level of risk changes with each flight.
While it’s fair to say the level of risk to specific systems decreases with each flight, it increases in other areas. In flight test, the team is always doing something for the first time. However, the first flight always has the highest risk potential because it has the most unproven systems.
“Each flight has a different risk level,” explains Young. “During XB-1’s first flight, we didn’t raise the landing gear for a reason. We tested other mission-critical systems first and did not introduce an additional level of risk.”
“During the second flight, when we had more data available, we raised the landing gear,” she continues. “Each subsequent flight has introduced different tests at greater speeds and altitudes. This methodical approach is the core of all flight test programs.”
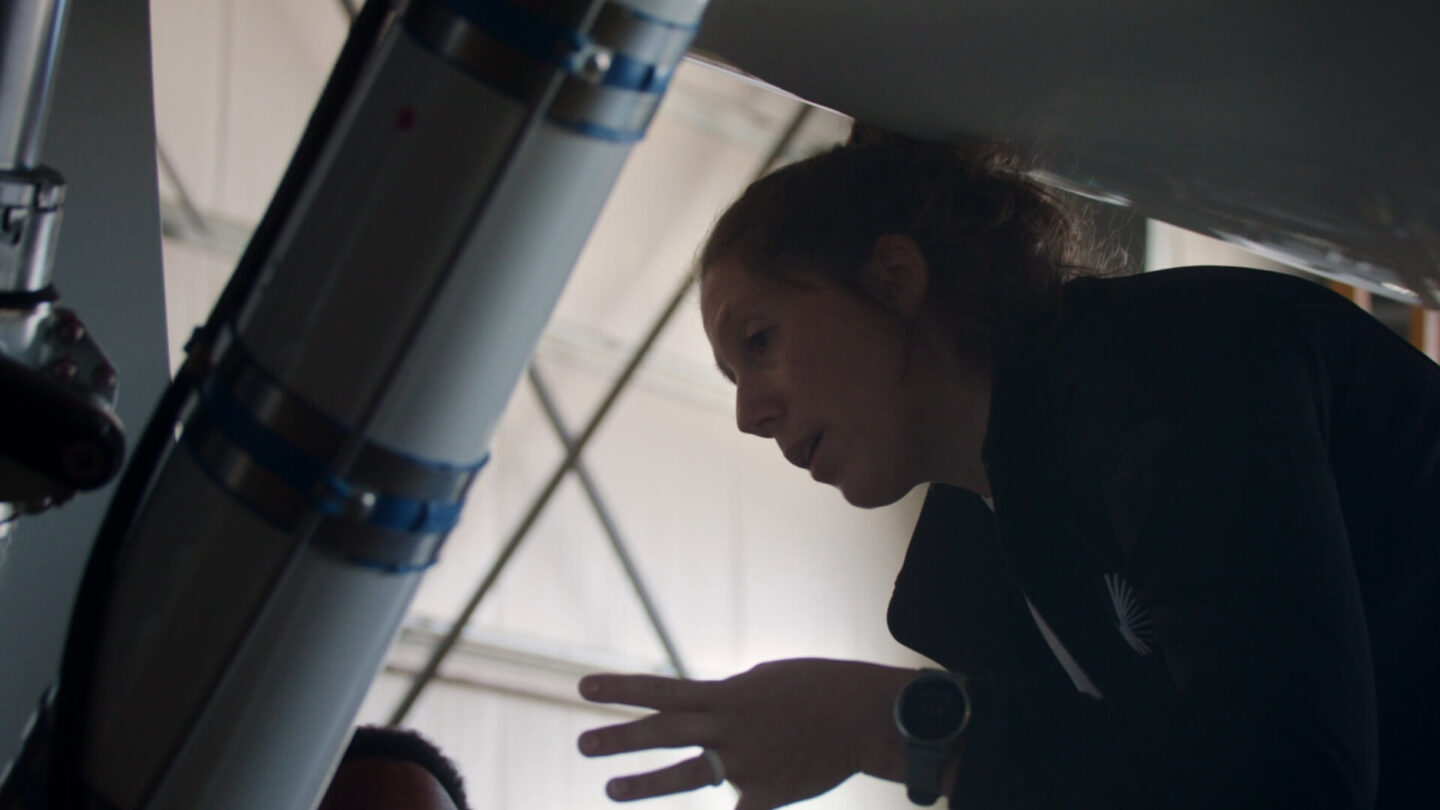
Climbing higher and faster
XB-1’s flight test program progressively adds new tests and benchmarks, but only when previous tests indicate the aircraft is cleared to do so. With each flight, XB-1 reaches new speeds and altitudes. Young breaks down each flight by its milestones to date:
Flight 1: First Flight
This was our initial assessment of the aircraft’s handling qualities, and it posed the greatest level of risk.
Flight 2: Landing Gear Tests
We retracted and extended the landing gear in-flight for the first time, establishing this essential milestone for all subsequent flights; we also tested the digital stability augmentation system.
Flight 3: Pitch, yaw, and environmental control systems
We achieved the maximum pitch and yaw attitudes expected during future flights; we also verified the environmental control system (ECS), which ensures our pilot has a reliable oxygen supply at high altitudes.
Flight 4: Flutter and G-forces
This flight marked the first use of the flutter excitation system (FES)—a device that is applied during flight tests to intentionally vibrate the aircraft. (FES is only used during flight tests and is not installed on commercial aircraft.) We also successfully applied elevated g-forces of 2.78g in preparation for supersonic flight.
Flight 5: Testing at up to Mach 0.69
We raised the landing gear right after takeoff and reached a new top speed; we also tested handling quality, flutter, and pacer checks at progressively higher speeds.
Flight 6: Altitude envelope
We expanded the altitude envelope to 20,000 ft. (We use the term “envelope” to describe an aircraft’s operating boundaries.)
Flight 7: On the edge of transonic speed
We reached a new top speed of Mach 0.82, which is the outer limit of the transonic regime—it’s faster than some commercial aircraft can fly. (When aircraft speed hovers between Mach 0.8 and 1.2, it’s in the transonic regime.) We also tested cockpit pressurization.
Flight 8: Stability augmentation system off
We confirmed that our pilot can safely operate XB-1 at Mach 0.8 with the stability augmentation system off. Here’s why this is important: Many modern fighter jets use computerized automated augmentation systems to make quick, constant adjustments to the flight path—adjustments that a human can’t make. While XB-1 has a computerized augmentation system, the aircraft design doesn’t rely on it to stay safe. We call the augmentation system “non-critical” because it isn’t necessary for safe flight. It simply helps to make things a little smoother and more manageable when it’s on. We confirmed that if it were to fail, our pilot could safely operate the aircraft.
Future flights
Future flights will see XB-1 climbing higher and faster toward breaking the sound barrier. During Flight 9, the team will finalize flutter excitation system tests, and evaluate flying and handling qualities at up to Mach 0.9.
“Boom’s flight test program is rigorous and progressive,” Young concludes. “Each flight has benchmarks we must achieve before proceeding to further tests. And at the core of the program is safety. It is always in our hearts and minds that a human pilots XB-1; it is not a drone.”
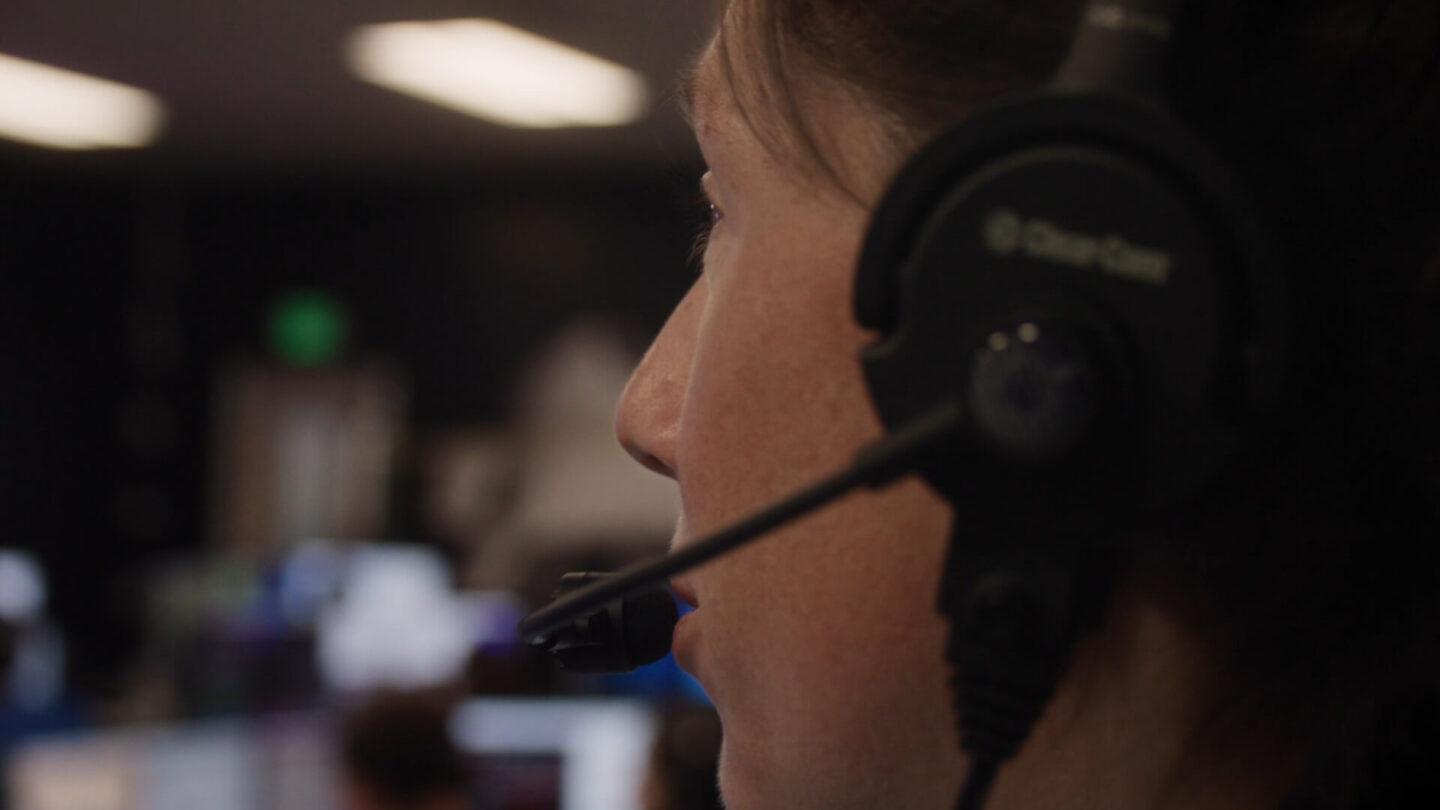
Planning for the unexpected
As Young likes to say, the ultimate truth of a flight test is that not everything goes as planned.
“Flexibility in a flight test program is essential,” says Young. “We have built a team that deals well with ambiguity. It enables us to pivot and refocus when a test flight doesn’t go quite as expected. No one is married to a schedule. This is a rare balance of a highly rigorous approach and a flexible mindset, something only a flight test team might understand.”
Here’s another surprise about XB-1—the flight test team practices for failure.
Before each flight, the team practices and rehearses in XB-1’s simulator. They recreate the entire flight and practice managing the unexpected.
“Only one member of the flight test team knows what’s going to happen during the simulation,” explains Young. “They ‘inject’ failures into the simulator and try to catch us by surprise. We’ve faced issues ranging from unexpected weather conditions to engine failure and loss of hydraulic power. We prepare for these issues, so if the unexpected happens, we are ready.”
While the team practices handling the unexpected, other issues require careful investigation. The team automatically reevaluates the flight test plan when an issue is identified.
As a demonstrator aircraft, XB-1 was built with several third-party, off-the-shelf systems. When a question arises about a third-party system, the XB-1 team partners with the manufacturer to find a resolution.
“At various points during the flight test program, we’ve invited manufacturers to work alongside our team to identify and fix any issues we encounter,” says Young. “We’re not just collaborating as a team; we’re collaborating with manufacturers and experts across the aerospace industry.”
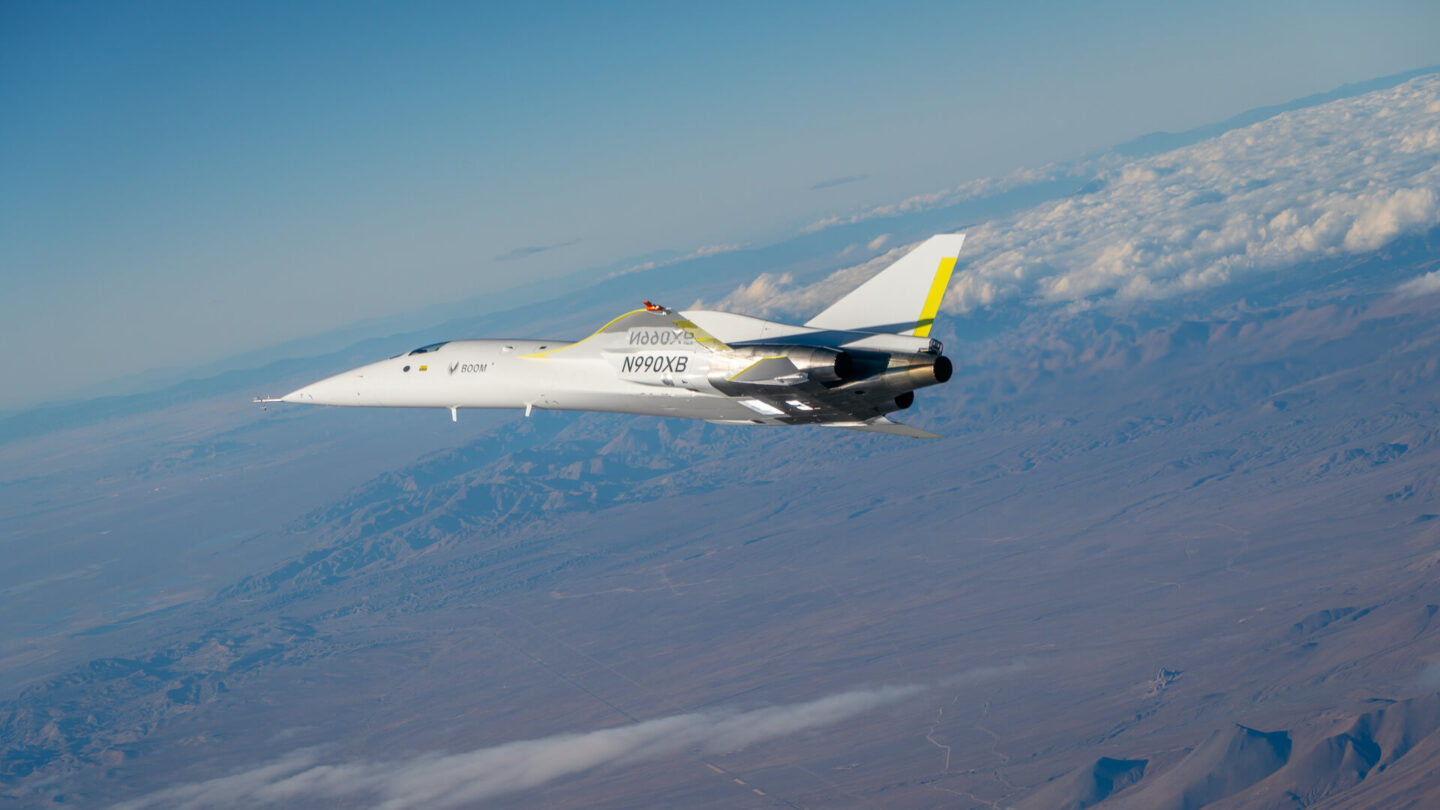
Demonstrator aircraft as testing ground for new technologies
The Flight Test team is putting more than XB-1 through its paces. As a demonstrator aircraft, XB-1 is an ideal testing ground for new third-party technologies. For example, during XB-1’s eighth flight, the team tested a new material—a shark skin-inspired ‘riblet’ material they applied to XB-1’s underbelly. Developed by MicroTau, it aims to reduce drag, fuel consumption, and emissions, especially at high speeds. The team will monitor it throughout the remaining flights.
This test is part of a collaboration with the Defense Innovation Unit (DIU), which is focused on the rapid adoption of commercial and dual-use technologies, and the Air Force Operational Energy Office. XB-1 was chosen to test the durability of the new material because it has characteristics similar to many U.S. Air Force aircraft.
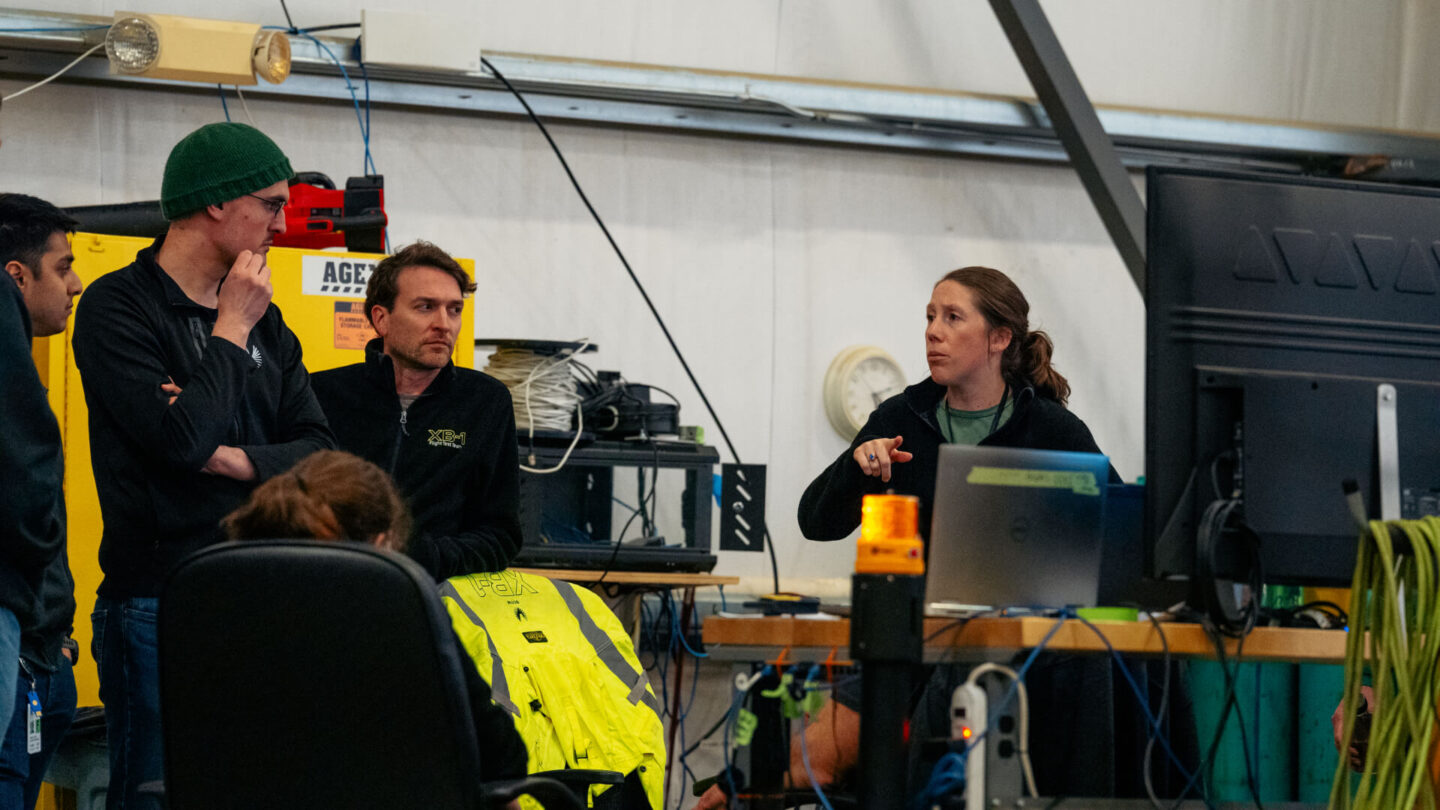
From demonstrator to passenger aircraft
Every aircraft must undergo a thorough flight test campaign before going into use, but the specific tests vary.
“It goes without saying that flight test of XB-1, a one-of-a-kind demonstrator jet, is different from how we will test Overture, a commercial passenger jet,” says Young. “But the methodology is the same: Boom’s progressive approach of rigorous testing that leads with safety.”
As a commercial passenger aircraft, Overture will be certified by the FAA (Federal Aviation Administration). The process begins with a design review, followed by ground and flight tests, and maintenance and operational evaluation, leading to airworthiness certification.
XB-1, considered a demonstrator or experimental aircraft, needs a Special Airworthiness Certificate issued by the FAA to operate. That certificate has strict operational limits, including where you can fly, which in XB-1’s case is the Mojave desert.
One of the most significant differences between the XB-1 and Overture flight test programs is certification, which influences every aspect of the program. The requirements for Overture are dramatically different from those for XB-1.
A second difference between the two aircraft is the testing on Overture before its flight test program even begins.
Young explains that Overture will have more advanced tools and testing before the aircraft reaches the flight test phase. Overture’s systems and components are designed specifically for the aircraft (not off-the-shelf, like XB-1’s). This will provide extensive and early testing opportunities for Overture.
“By the time Overture reaches the phase that XB-1 is in now, the flight test team will have a wealth of information and previous testing behind it,” says Young. “The difference between flight test for demonstrators versus commercial aircraft is like night and day, except for the process itself. Our flight test team will apply the same systematic, rigorous approach to both aircraft. The tests will differ; the process and culture will be the same.”
The XB-1 flight test team has established a safety-first culture that carries forward into all aspects of the company and is interwoven with the design and planning for Overture. At the heart of it is a culture of accountability that Young believes is Boom’s greatest strength.
“Boom has built one of the best flight test teams in the world,” she concludes. “We are deeply rooted in a culture of safety and accountability—and each of us strives for excellence. As an engineer, there is no greater honor than being part of this team, and I’m immensely proud of what we have accomplished. The best aspect is that I know we will have many more accomplishments to celebrate in the coming years.”