How does a concept go from sea to sky—and from nature to aviation? Read on to learn how Boom tested the durability of a new material that’s inspired by sharkskin.
Testing sharkskin-inspired material on XB-1
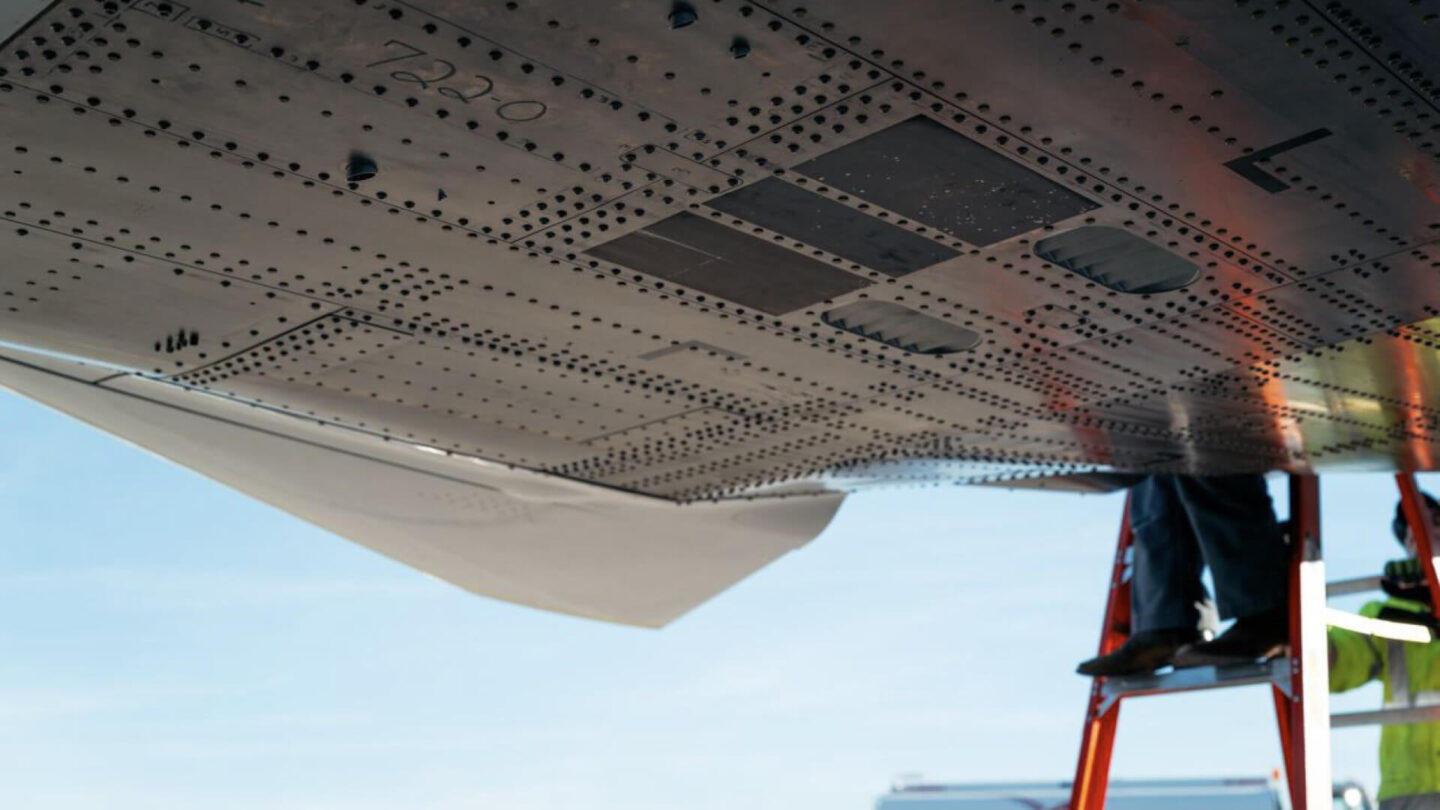
Did you notice anything different about XB-1 during Test Flights 8 through 13? You have an eagle eye.
During Flight 8, we launched a series of tests on new material in collaboration with the Defense Innovation Unit (DIU), which is the Department of Defense (DOD) organization focused on accelerating the adoption of commercial and dual-use technology, and the Air Force Operational Energy Office (SAF/IEN), which is the Air Force’s office dedicated to increased operational capability through efficient use of energy. While the Air Force did not fund this specific effort, they were willing to allow the use of their existing contract vehicle for the testing to be accomplished. We applied the film-like material to XB-1’s aft underbelly and tested its durability at transonic and supersonic speeds.
Developed by MicroTau in Australia, the sharkskin-inspired riblet material reduces drag, which in turn can reduce fuel consumption, carbon emissions, and operating costs. On aircraft, riblets are microscopic grooves on the surface that reduce skin friction by smoothing turbulent airflow.
MicroTau is developing a durable material to survive the harsh environments experienced in aviation. The film is designed to be efficiently and effectively installed, maintained, and eventually removed in line with existing aviation maintenance schedules.
In fall 2024, the XB-1 team applied patches of the material to the aft underbelly on a painted and unpainted (titanium) surface. We tested several patches with a total area of 0.5 m2 (5.4 sq ft).
The Boom connection
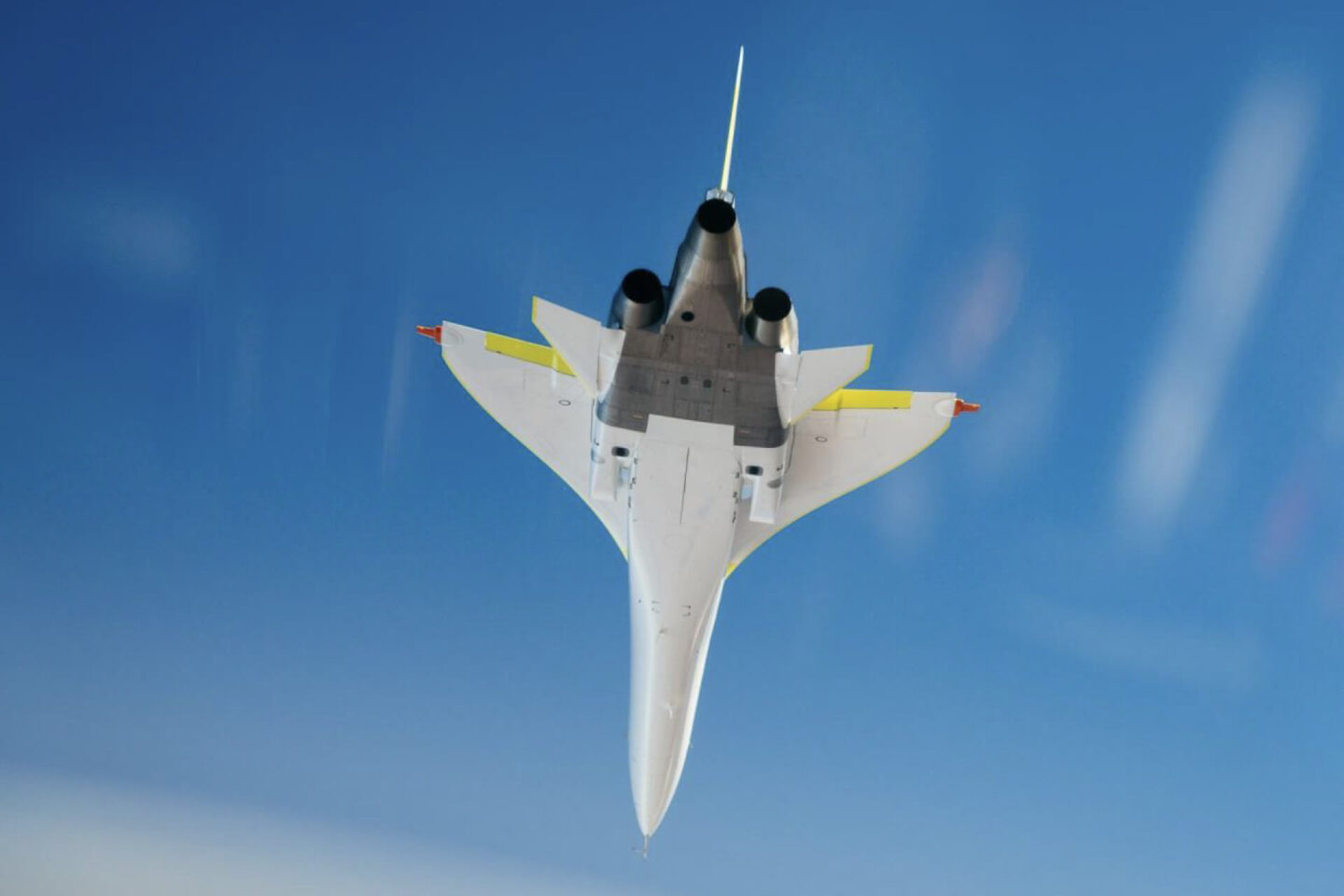
How did a material developed in Australia become part of the flight test program for XB-1, the world’s first independently developed supersonic jet? It began with a mutual connection between MicroTau, Boom, and DIU.
In early 2023, SAF/IEN and DIU selected MicroTau to develop a commercially viable technology to reduce drag and, therefore, fuel consumption, that could be rolled out to several U.S. Air Force legacy aircraft, including the C-17 Globemaster III and C-130 Hercules (military cargo transport aircraft), as well as the KC-135 Stratotanker (aerial refueling tanker). MicroTau was also chosen to test and deliver a riblet solution for the C-130J Super Hercules. These military transport aircraft are capable of subsonic speeds of less than Mach 0.8.
DIU’s mission is to facilitate the rapid transition of commercial technologies into the DOD through industry partners and multiple DOD offices. DIU helped identify the opportunity to test the durability of the riblets on XB-1 at higher speeds in the near-transonic (Mach 0.8 to 1.2) and supersonic (above Mach 1.0) speed regimes. Because MicroTau’s other tests are only conducted on subsonic aircraft, validating MicroTau’s findings at faster speeds was vital.
Applying lessons from sea to sky
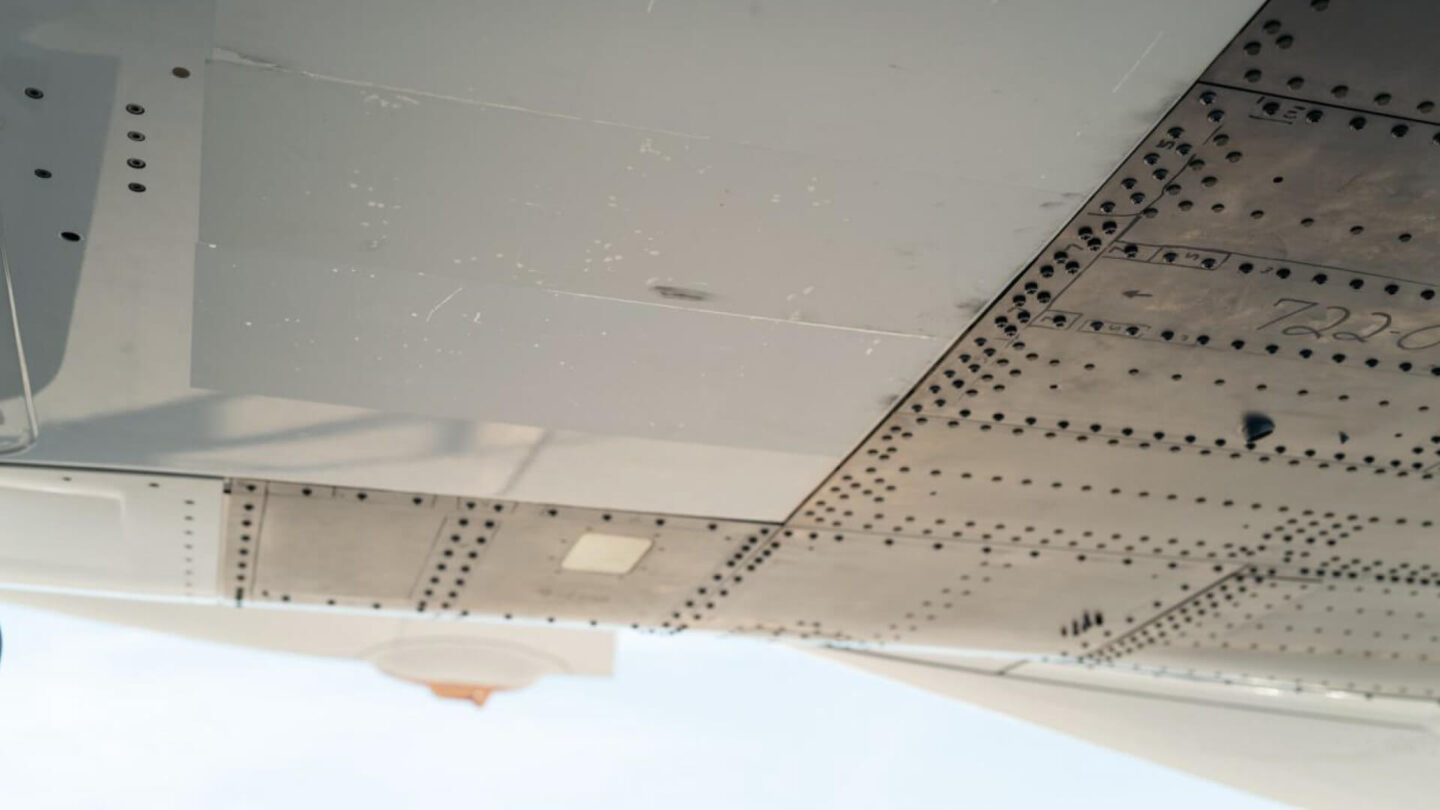
What exactly are riblets? Sharks have been perfecting their riblet design for millions of years. Their skin is covered in tiny, tooth-like scales, which help them glide through water with impressive efficiency. These riblet scales point toward the tail and help reduce friction from the surrounding water when the shark swims.
The science behind riblets has been around for more than 40 years. The original research was conducted by NASA’s Langley Research Center in the 1970s and pursued by aerospace researchers, as well as the maritime industry.
MicroTau was born from a need in both defense and commercial aviation for solutions to improve fuel efficiency. In 2015, MicroTau’s Henry Bilinsky invented a scalable method to print drag-reducing shark skin riblet microstructures, and this technology has now flown thousands of flight hours on aircraft around the globe.
What is drag, and why is it important?
Drag is the aerodynamic force generated in flight. Around half of an aircraft’s fuel is spent overcoming drag—burning fuel to push the plane through the air.
Airplanes overcome drag with engine thrust, which requires fuel. More drag means more thrust, which requires more fuel. More fuel means a heavier aircraft, which in turn requires more thrust.
As a result, reducing drag—even by a small margin—can reduce emissions and fuel costs while enhancing mission capability.
“From a big picture perspective, our Riblet Package product can potentially save the aviation industry up to $10 billion in fuel annually,” explains MicroTau Founder and CEO Henry Bilinsky. “Due to the fuel cost savings, our customers in commercial aviation can expect a profit uplift of around 20 percent.”
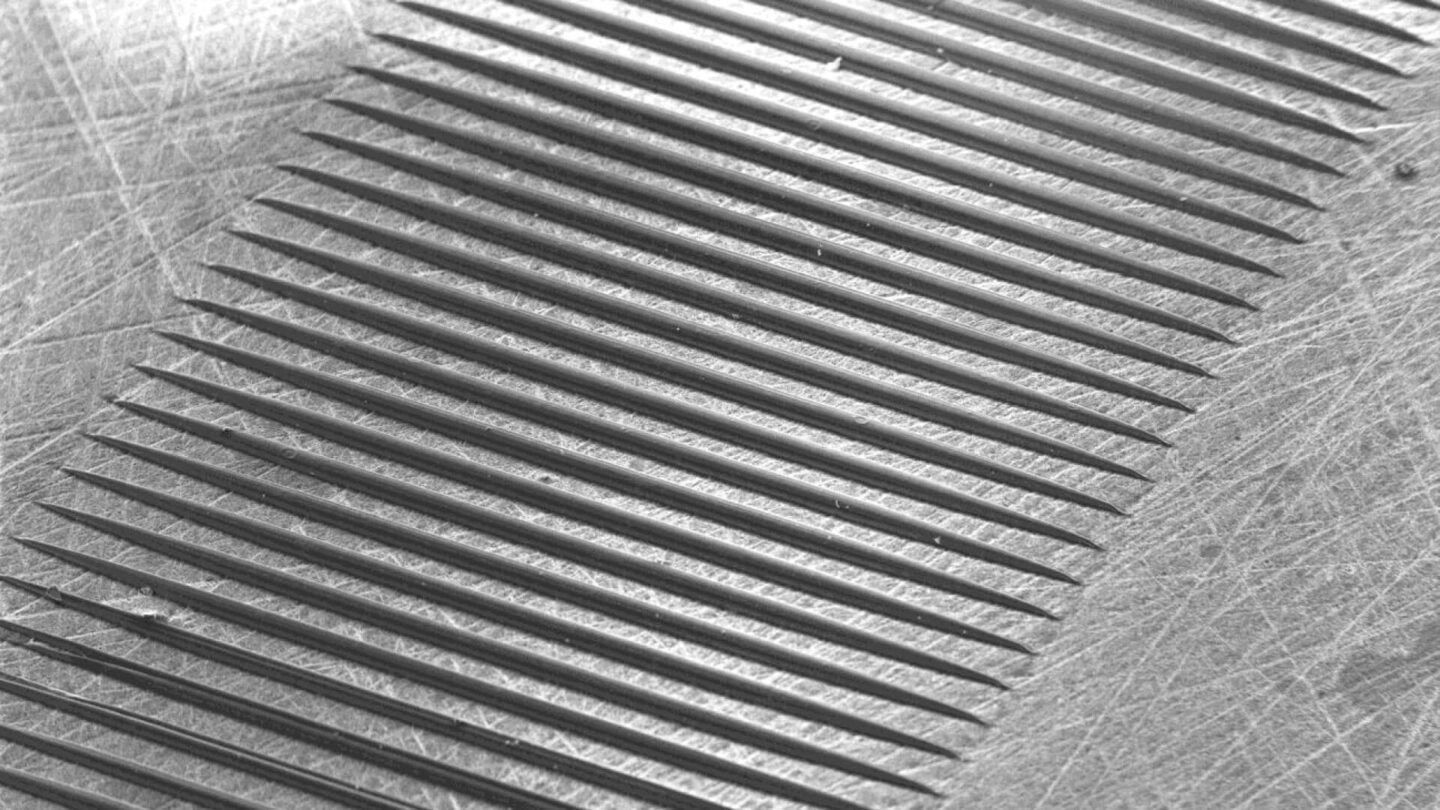
Driving innovation in aerospace
As a demonstrator aircraft, XB-1 is ideally suited for testing new materials and technologies. Think of it as a flying data collector supported by a team of flight test engineers.
The ultimate goal of MicroTau’s tests was to de-risk the technology for broader U.S. Air Force legacy aircraft and commercial applications, and its potential application on Overture. The MicroTau team examined data during flight tests to ensure their extensive lab results can translate to the real world.
Subsonic, transonic and supersonic tests
Test patches of MicroTau’s Riblet Package were flown on XB-1 test flights at subsonic and transonic speeds. The Boom team conducted observations and returned photographic data to MicroTau detailing the durability performance of the test patches at these speeds. Durability and adhesion met the expectations established in MicroTau’s tests on commercial airliners, with the patches having survived these conditions comfortably with no observable degradation.
XB-1’s Flight 12 and 13 saw the aircraft achieve supersonic speeds over the Mojave in the same historic airspace where Chuck Yeager broke the sound barrier for the first time in 1947. Along for the ride were MicroTau’s Riblet Package test patches, also breaking the sound barrier for the first time. The teams were pleased to report that these tests resulted in no macroscopic degradation, nor any lifting of the film from XB-1’s surface despite the extreme conditions—as perfect a result as they could have asked for.
Depending on testing outcomes, aircraft fleets worldwide may one day glide through the skies with shark-like ease—thanks to the combined innovation of nature and technology.