On October 7, 2020, Boom will unveil XB-1 to the world. With rollout right around the corner, here’s an inside look at three recently completed milestones that span from tip to tail.
Avionics systems: Installed.
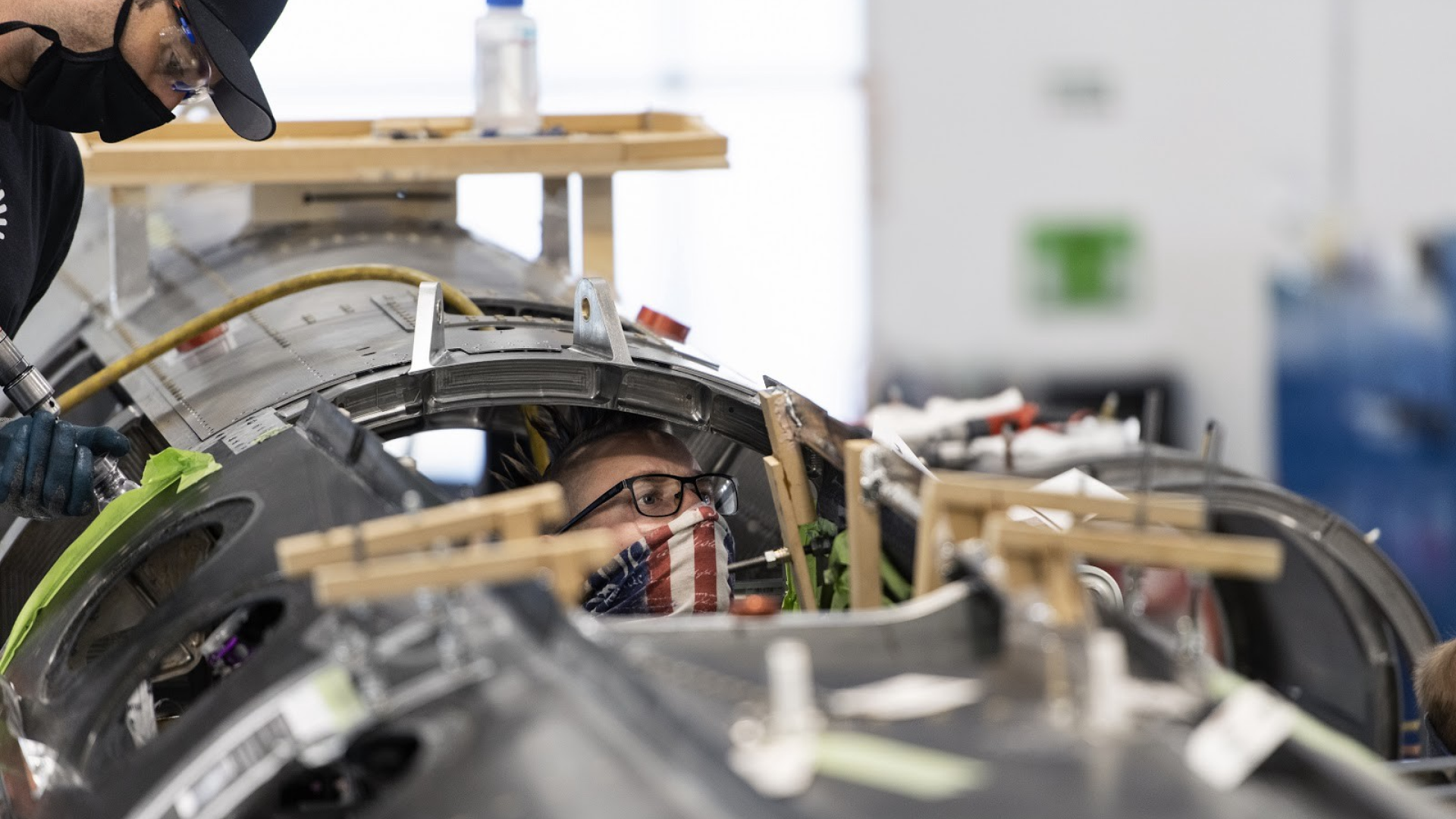
Objective: Install and test 370 pounds (168 kg) of wires.
Purpose: The avionics system is like the brain and nervous system of an aircraft. Avionics wires connect each system, including hydraulics, flight controls, communications, navigation and environmental control, to a central computer that records everything. This data is then displayed to the pilot. Pertinent data is also transmitted in real-time to the control room on the ground where teams are on the lookout for anomalies.
Materials: Six miles (9.6 km) of wire are strung throughout XB-1. Contained in more than 150 individual assemblies, the wires weigh close to 370 lb (168 kg). The team installed wires in almost every part of the aircraft. It was a meticulous operation with little room for error. While the small spaces within XB-1’s thin wing and long, sleek fuselage offered little room to physically maneuver, work progressed smoothly thanks to the team’s patience, attention to detail, and ability to adjust to the unique workspace.
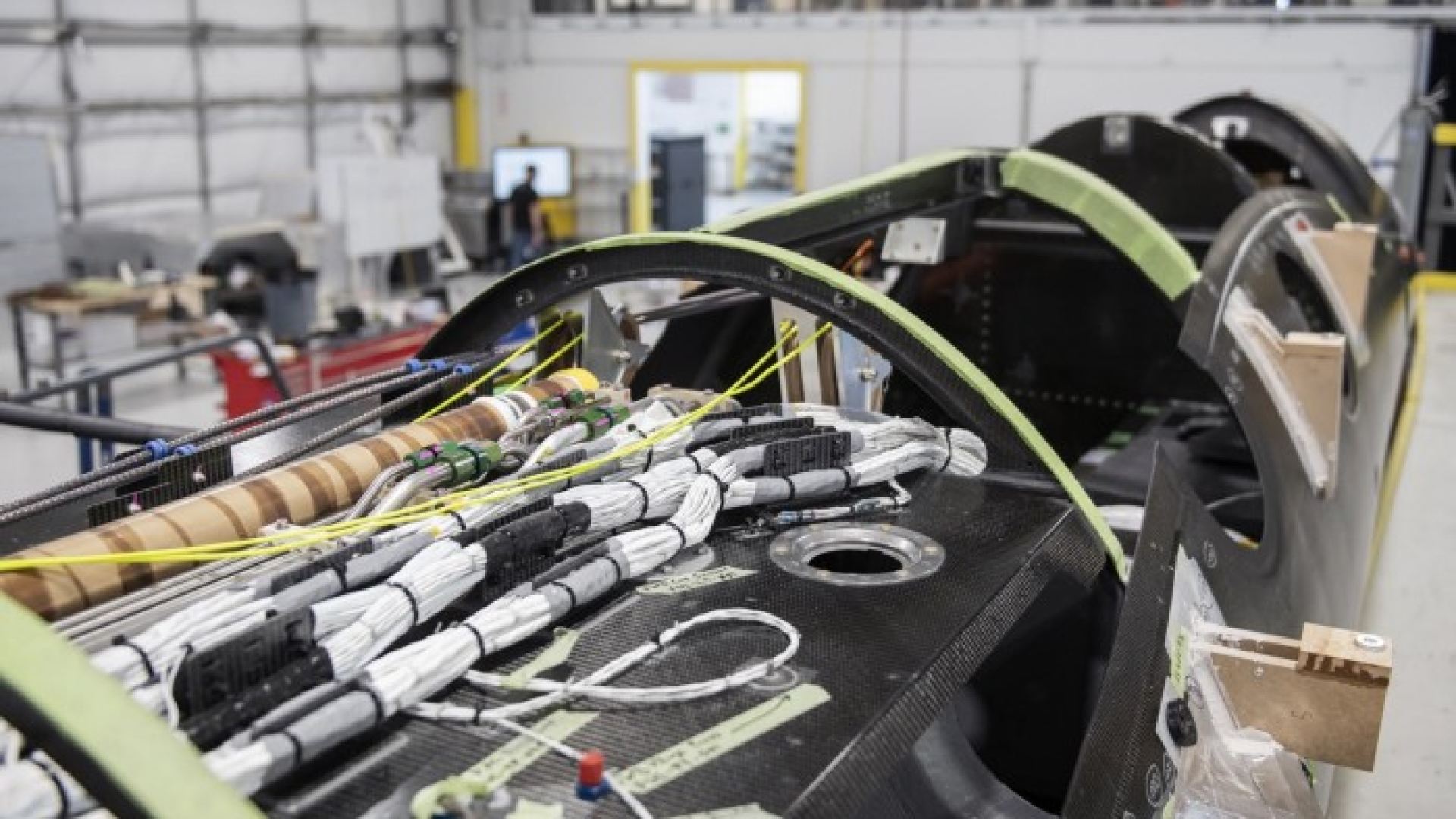
Testing: On XB-1, “avionics” is a broad term that includes all the wiring and most of the electrical devices installed on the aircraft. It also includes custom software that Boom developed in-house. The team runs a rigorous set of tests every night as part of a “Continuous Integration” (CI) process. These tests verify that each part of the code functions as intended. In the event that the software fails a test, the team can start fixing it the next morning. This daily cadence identifies an area of concern before it causes a larger problem.
Flying Laboratory: XB-1 is built to gather as much data as possible during each flight. Avionics gathers much of that data. Thousands of sensors will constantly measure every aspect of flight. This data will be invaluable to the teams on the ground. As a “flying laboratory,” XB-1 will record vital data that will inform and optimize the design of Overture, Boom’s supersonic airliner.
Aft fuselage: Installed.
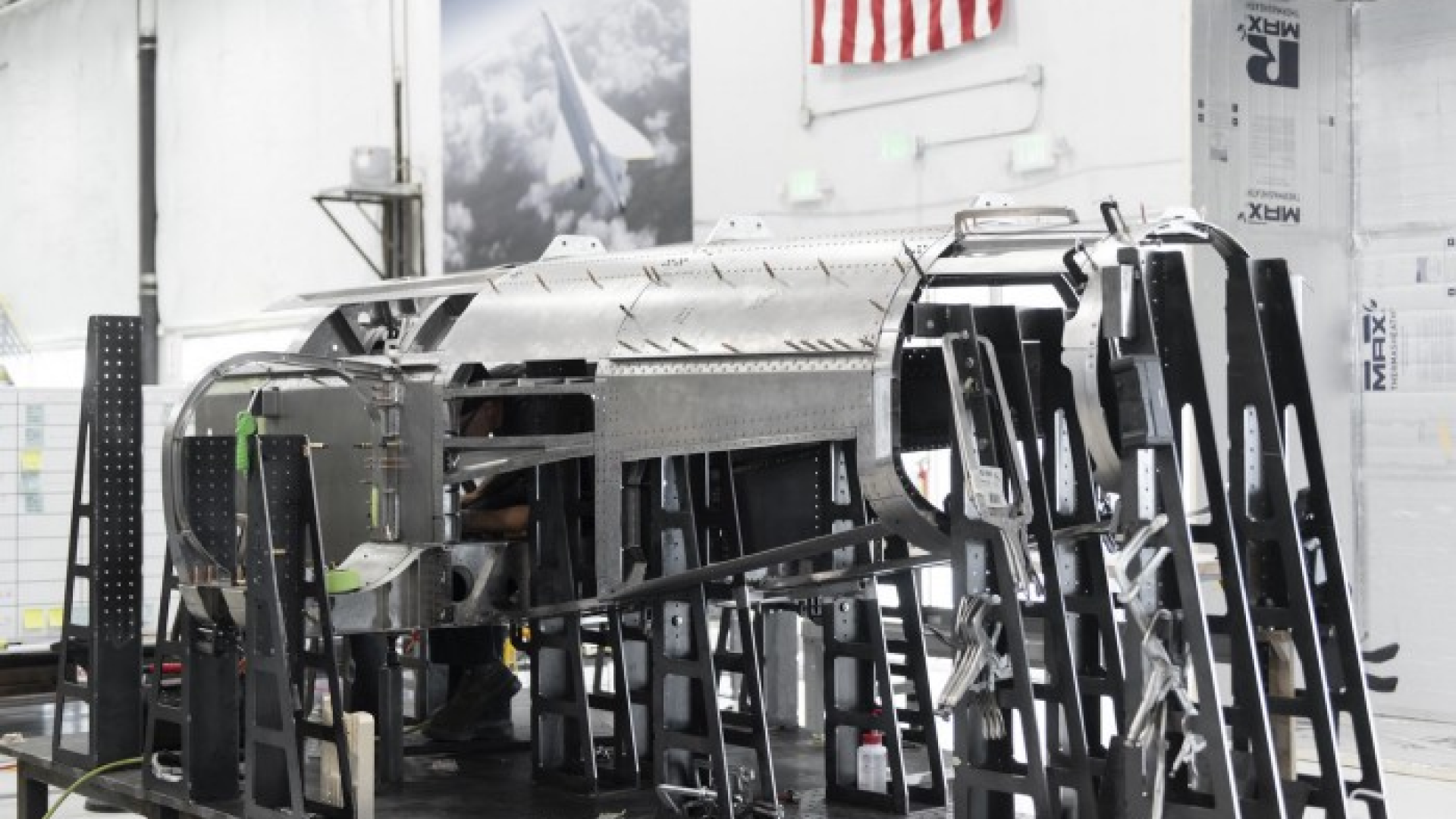
Objective: Build the titanium aft fuselage from raw materials (titanium plate and sheet stock).
Purpose: The aft fuselage holds XB-1’s three engines. It’s the rear section of the aircraft.
Materials: The aft fuselage is the only section of XB-1 that is entirely metallic. The team machined it with 90% titanium and 10% A286 (a metal alloy that can withstand extremely high temperatures, even higher than titanium). Titanium isn’t just heat-resistant and incredibly strong, it’s also lightweight. Reducing aircraft weight also reduces fuel consumption, which results in cost-savings over the long-term and also lowers carbon emissions.
The aft fuselage also includes Inconel heat shields, located right behind the side engines. Inconel is an austenitic nickel-chromium-based superalloy that withstands extreme heat.
Manufacturing: The aft fuselage began as 25,000 lb (11,340 kg) of raw titanium, which is notoriously difficult to machine. Forming the shape, and securing all sections, was a painstaking operation. The team drilled close to 6,000 holes to achieve the perfect alignment using Stratasys 3D-printed drill blocks. Because titanium is difficult to form, “bump forming” was applied to achieve the curvature of the skin panels. It’s a process that uses a hydraulic press brake to put dozens of small bends into sheet metal to achieve gradual curvature and complex bends. This operation ensured the skins were made to the correct shape before fitting them onto the airframe.
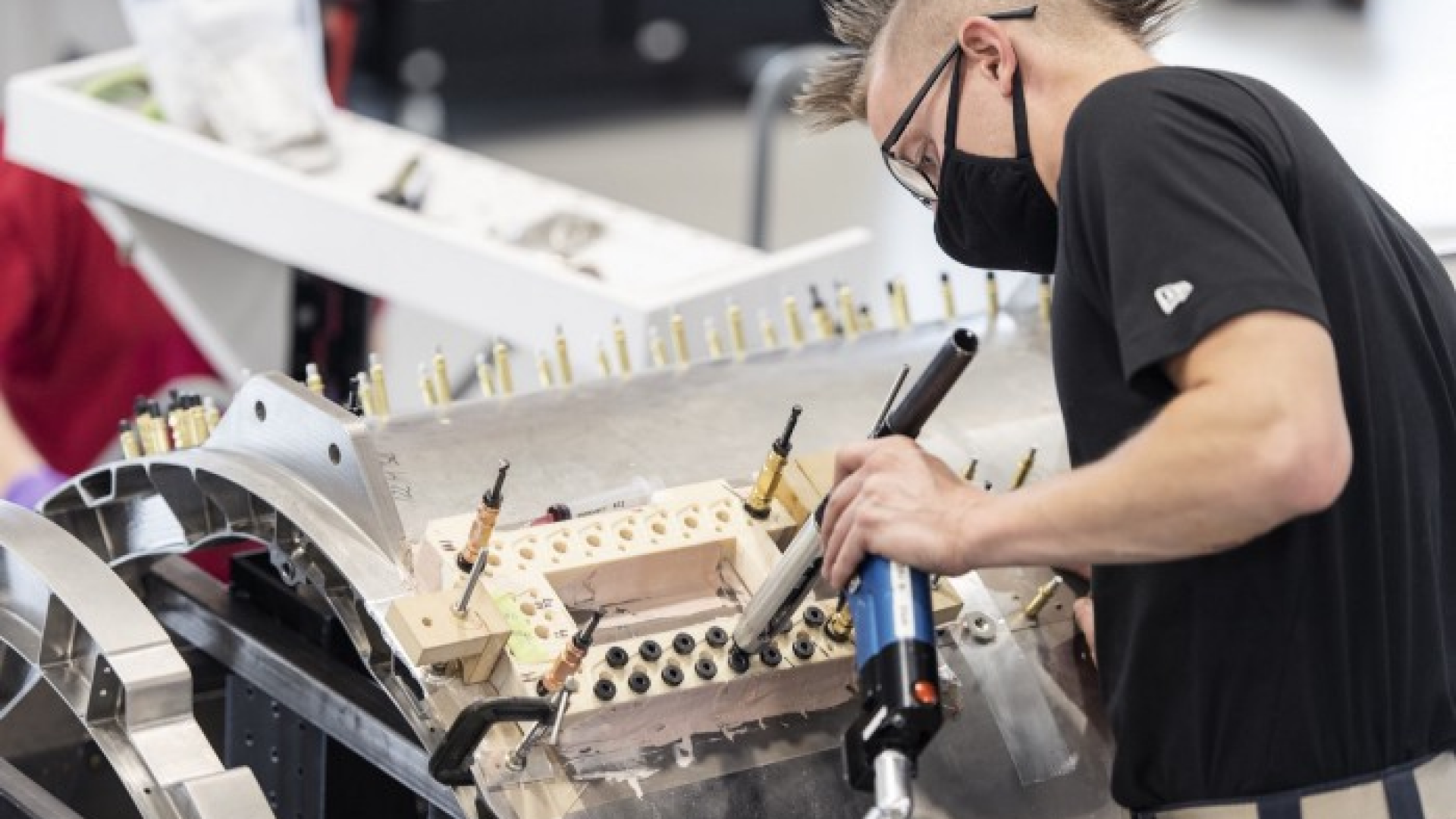
How hot, exactly? Between titanium, A286 and inconel, the aft fuselage is built to withstand temperatures that would melt other materials. How much heat can it take, exactly? The Boom team estimates that the aft fuselage will experience:
- Maximum titanium temperatures of up to 800°F (427°C). (Titanium is very heat-resistant and maintains good strength to 1000°F (538°C).)
- Maximum A286 temperatures of up to 1200°F (649°C).
- Maximum inconel temperatures of up to 1600°F (871°C).
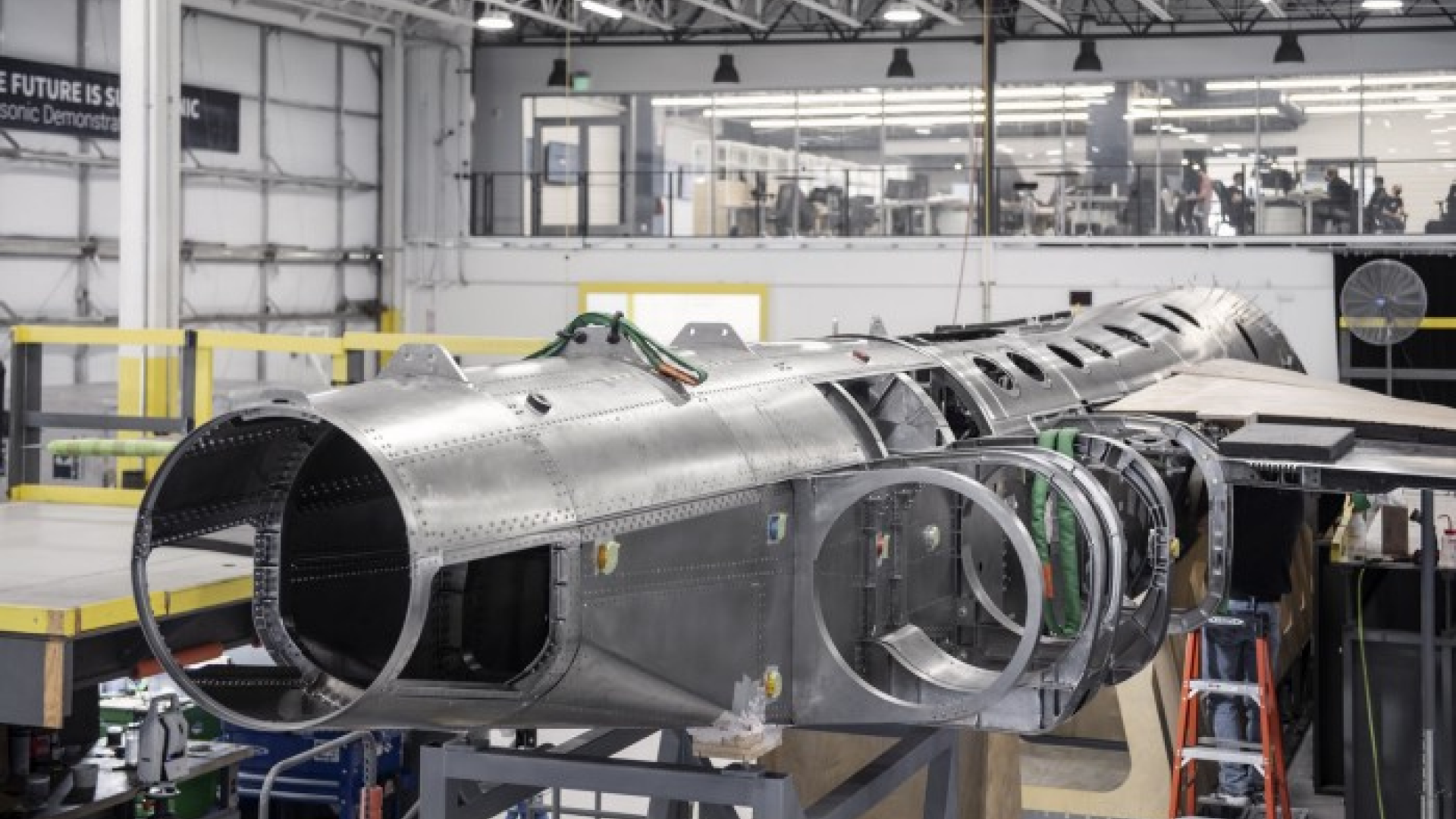
Vertical tail: Closed and installed.
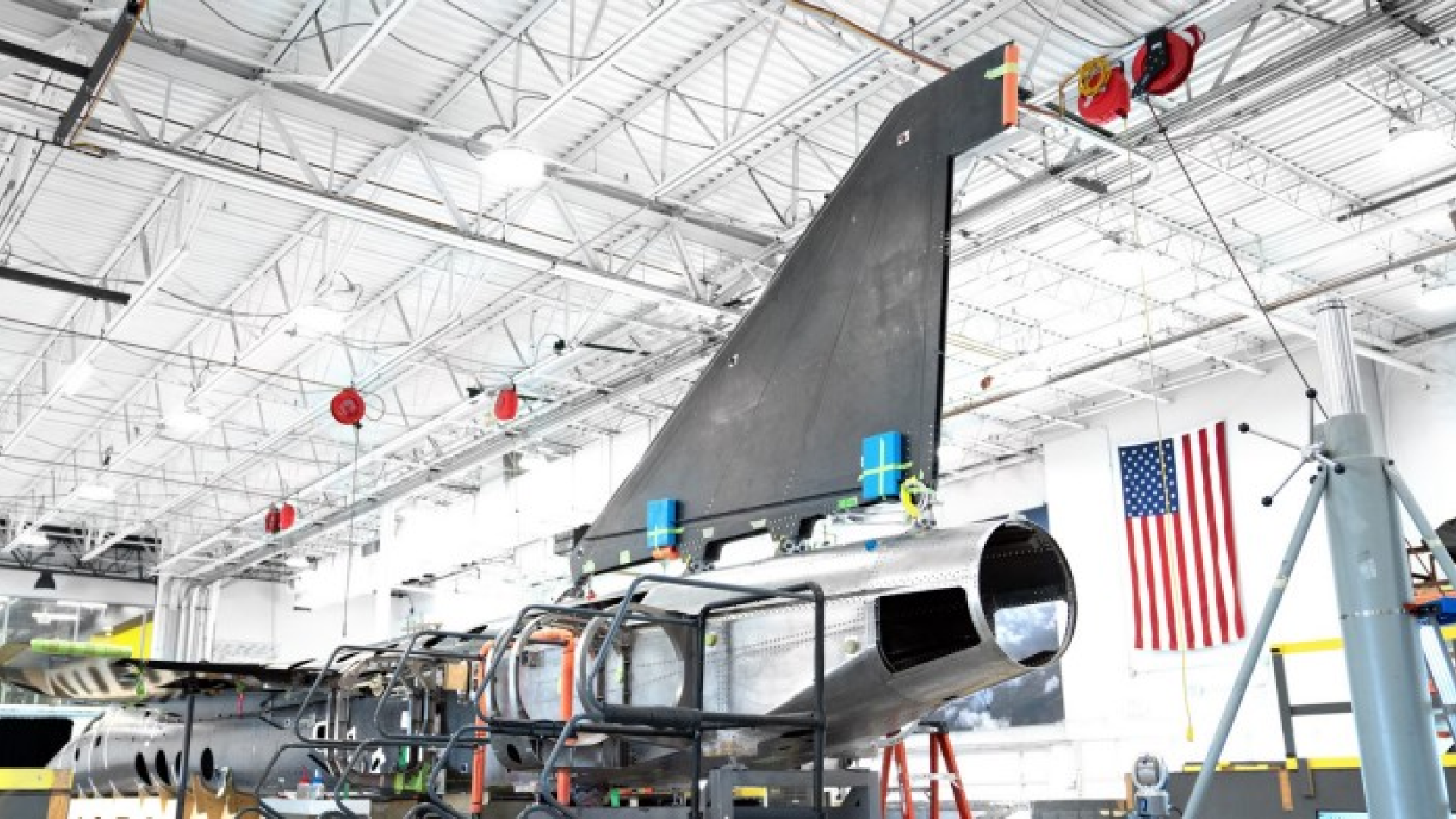
Objective: Build and test the vertical tail (stabilizer).
Purpose: Like a fin rising above XB-1, the vertical tail (vertical stabilizer) will keep XB-1’s nose straight and prevent yaw (swinging from side to side).
Materials: Weighing only 125 pounds (56.7 kg) with a height of 6 ft. 9 in. (2 metres) from root to tip and a length of 12 ft. (3.6 metres), the vertical tail is made of carbon fiber composite ribs and spars. Carbon fiber, which is very lightweight, is five-times stronger than steel and twice as stiff, making it the ideal material for the vertical tail. Four sets of mounts attach the vertical tail to the aft fuselage. The front and back are aluminum and the middle two are titanium. The center of the vertical tail must withstand greater force, making titanium the logical choice for these mounts.
Manufacturing: Similar in structure to the wings, the vertical tail is a bonded composite structure with fasteners in highly-loaded areas. The operation went like clockwork. The team, which successfully accomplished the wing closeout earlier this year, drew on their experience to quickly and efficiently complete the operation. But unlike the wings, the vertical tail has no access panels to access systems; it will never be reopened. The vertical tail doesn’t contain systems such as hydraulics and flight controls that must be accessible for maintenance between flights. As a result, no access panels are required. In fact, its systems interfaces are between the bottom of the vertical tail and the top of the aft fuselage.
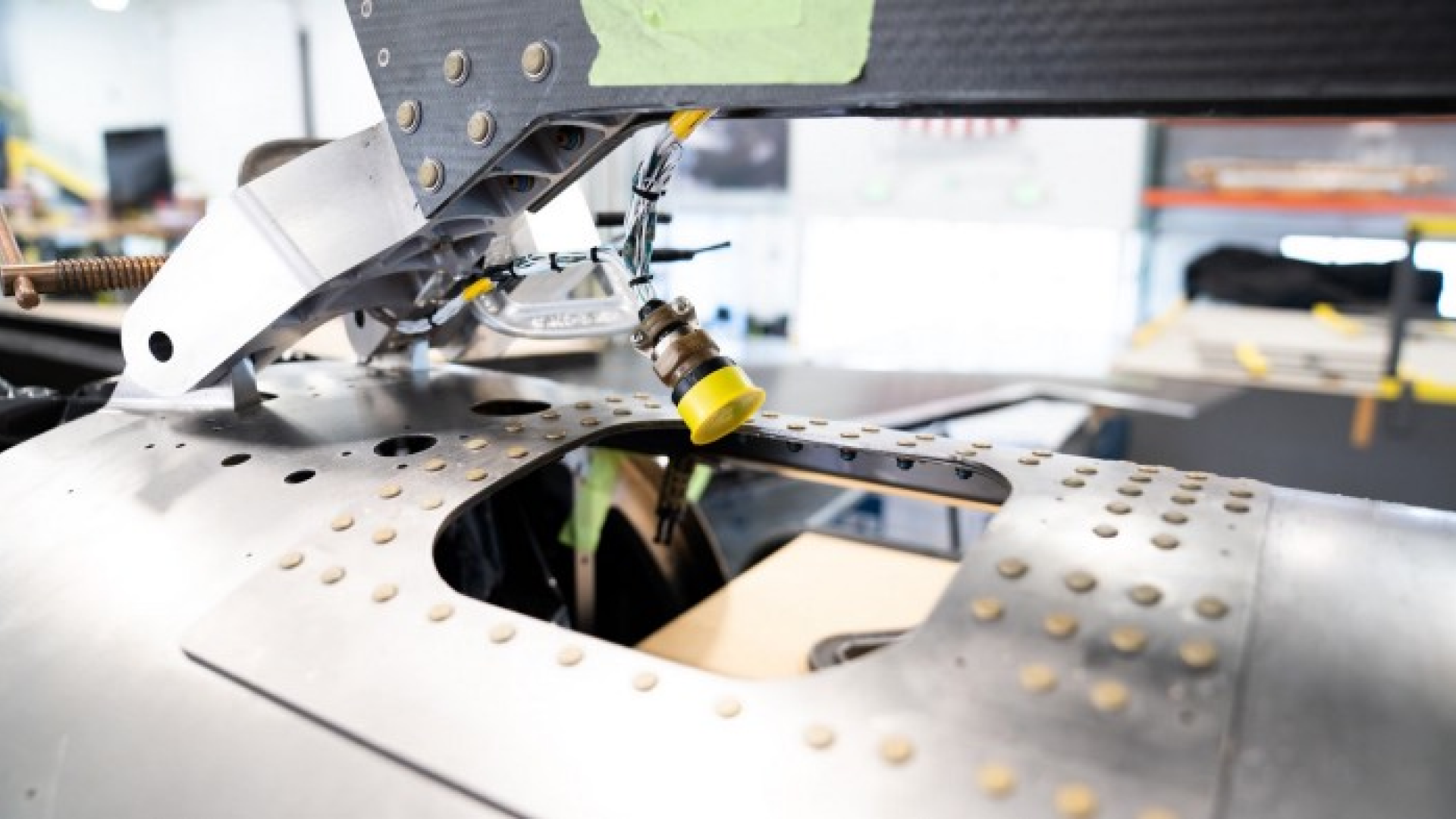
Testing: To expedite testing, the team moved the vertical tail testing to a specialized facility in Ohio. Two Boom team members traveled to the testing facility to record insights and apply learnings from the build to the process. During testing, they applied 4,800 pounds of force on the tail one direction at a time (about the weight of a Ford F150 pickup truck). String pots and fiber-optic gauges measured displacements and strains as the team put the vertical tail through simulated extreme conditions. The vertical tail passed with “flying” colors. Now fully attached to the aft fuselage, the vertical tail stands tall, bringing XB-1’s total height from the ground to the tip of the tail of 17 feet (5.2 metres).