Wood rots. Fabric perishes. Steel and iron are heavyweights. Titanium is pricey. Aluminum can’t always take the heat. Carbon fiber composites spur innovation.
The history of aircraft materials — what parts are made of — is like a chronicle of modern engineering.
Today’s aircraft include a wide range of materials, many of which weren’t widely available or feasible 50 years ago. Boom engineers, who have spent the past two years testing materials for supersonic flight, have combined both innovative and traditional materials in our supersonic demonstrator, XB-1.
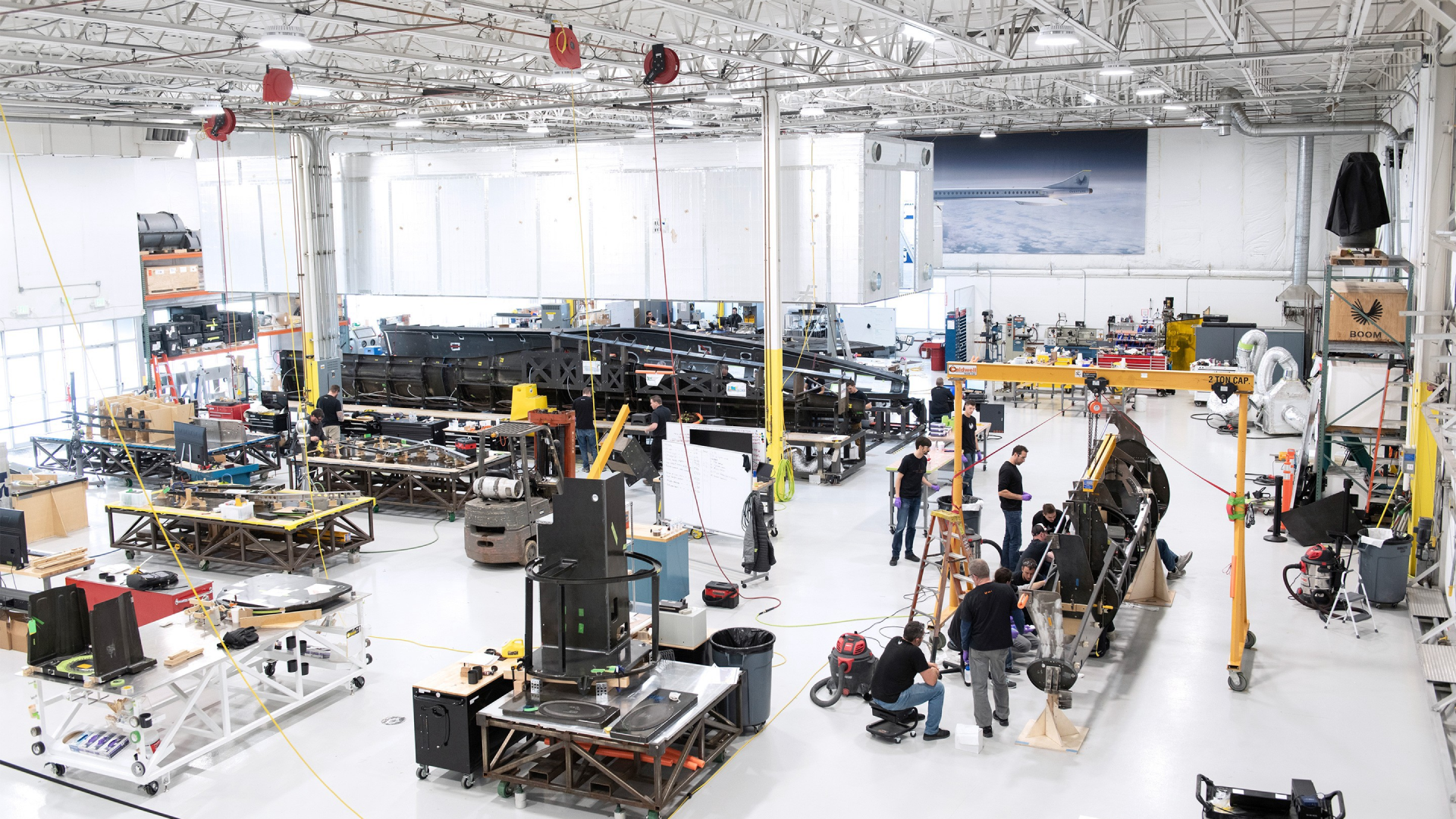
XB-1’s materials were selected based on dozens of factors. Throughout every step of the build, engineers balanced the requirements for performance, cost, strength and weight. Every pound of weight saved in design is another pound of fuel that can be used to fly XB-1 longer at supersonic speeds, so every material — and its subsequent parts — is analyzed methodically. Materials are also scrutinized on how well they perform over time; each part must maintain its mechanical properties throughout the life of the aircraft and perform just as well after 500 hours of flight time as it would after 50 hours.
For supersonic aircraft, which have unique issues of aerodynamic heating, materials must also provide thermal resistance. At supersonic speeds, there is greater compression of air on an aircraft, and that produces more heat. Because all metals expand and lose strength as they are heated (at speeds above Mach 5, most metals will melt or become so soft that they wilt and bend), the materials in a supersonic aircraft are selected with aerodynamic heating in-mind.
Built for strength and heat resistance, XB-1 features these key materials:
Carbon Fiber Composites
The majority of XB1’s fuselage structure, as well as some brackets, is manufactured from lightweight carbon fiber composites that offer strength and a low CTE (coefficient of thermal expansion). They expand at a rate more closely matching that of titanium, which is also a key material in XB-1. Composites are proven to withstand corrosion and wear and tear, making them materials of choice for parts that are exposed to the elements.
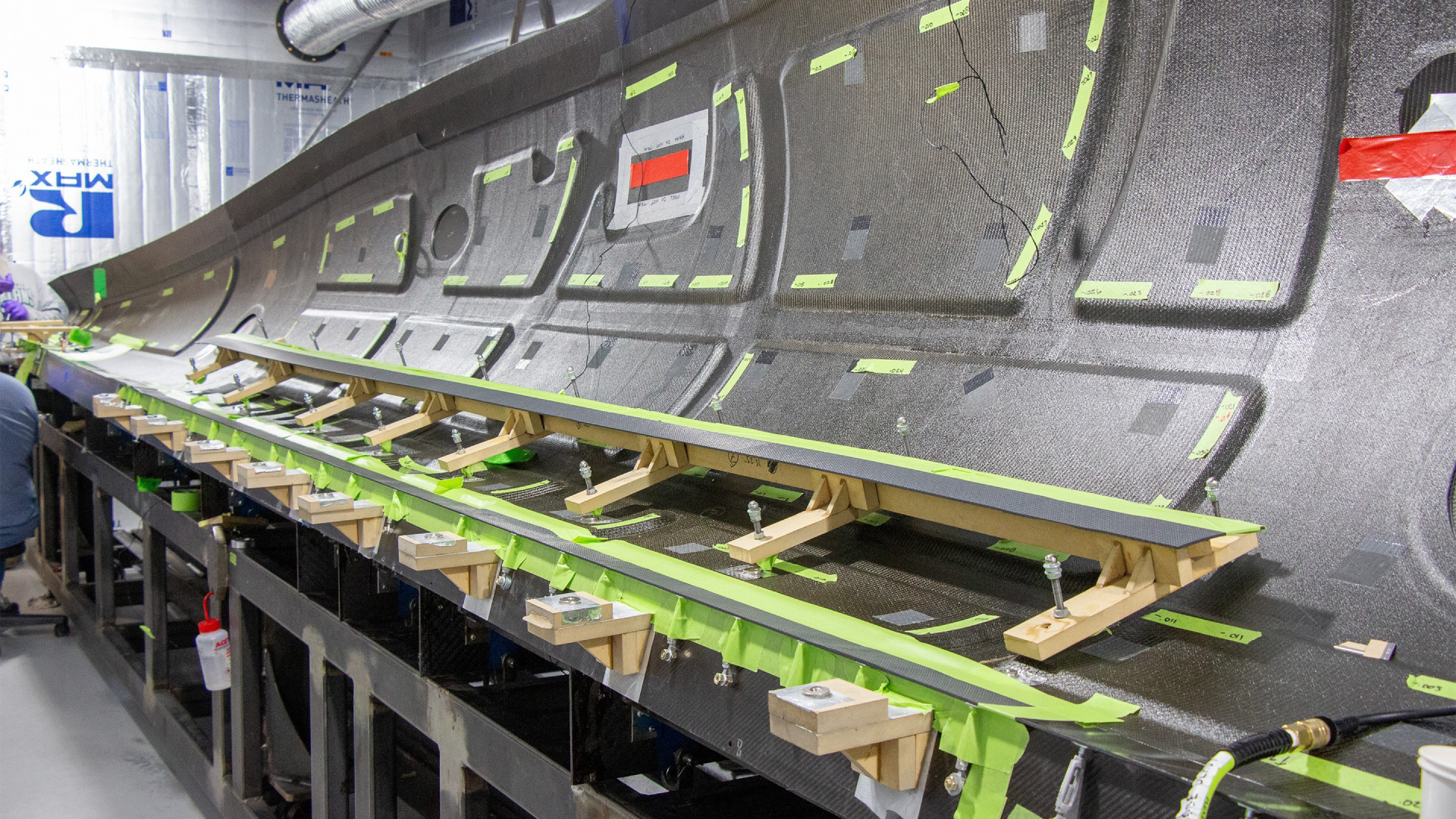
Composites were not fully tested and proven for aviation during the design of Concorde, although the aircraft did include them. Designed in the 1960s, Concorde was manufactured with materials ranging from unique aluminum alloys and steel, to stainless honeycomb and resin-bonded glass fiber (a composite). These materials withstood extreme heat, but weren’t all lightweight (which triggered the need for more fuel). We can only imagine how Concorde’s engineers would have used today’s composites to improve weight and heat challenges.
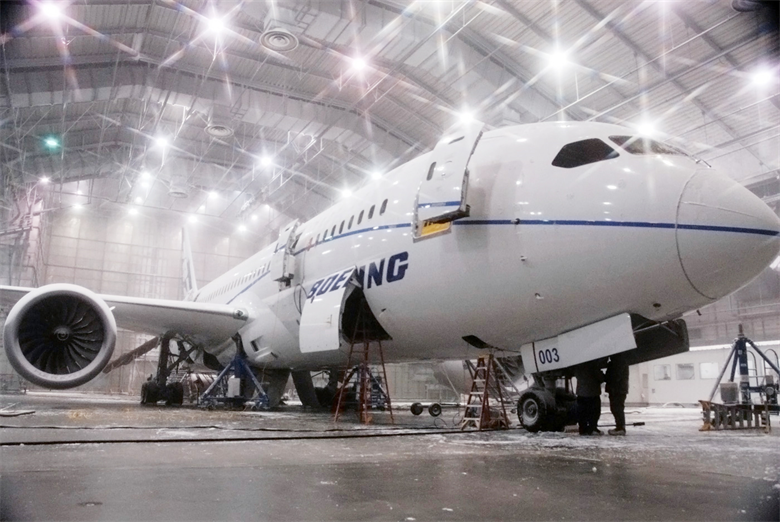
Titanium
Offering extreme strength, titanium is also compatible with carbon fiber composites. Both have similar heat characteristics and expand at a closer rate, making them an ideal pairing for supersonic aircraft manufacturing.
XB-1’s main landing gear bulkhead is manufactured from a 4-inch thick plate of titanium that weighs 66 pounds. It has one of the highest strength-to-weight ratios of any material in XB-1, and the bulkhead will take the majority of the load at landing speeds. When XB-1 lands, the bulkhead will absorb up to 112,000 pounds of force from each landing gear. The majority of the aft fuselage is also manufactured with titanium due to the strength required for this part.
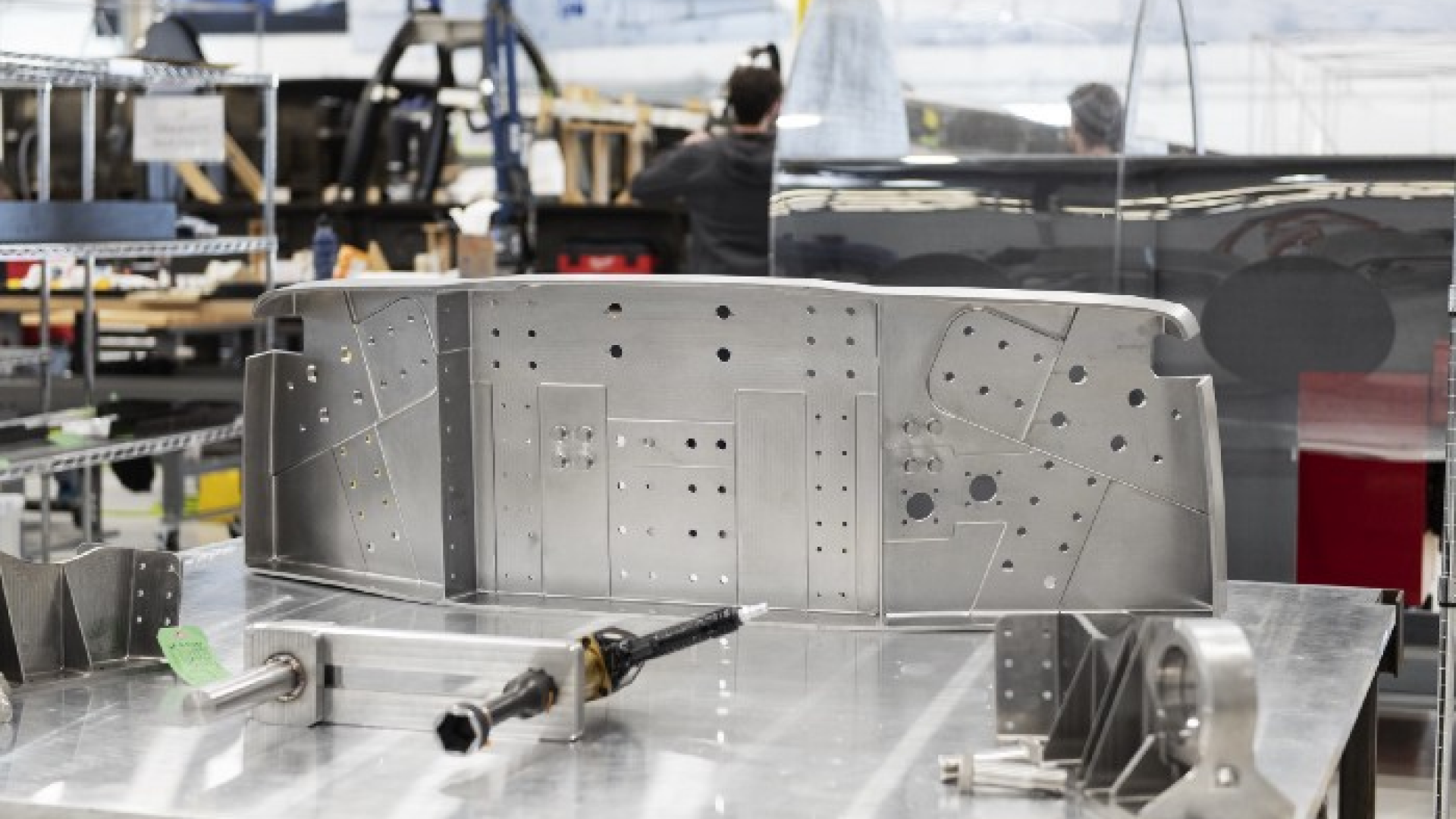
While titanium is ideal in these specific scenarios, it’s not feasible to manufacture an entire aircraft with this metal. It’s difficult to source and also very expensive, currently averaging $40 USD per pound compared to aluminum, which costs about a dollar per pound (both prices vary widely by market conditions and how the metal is purchased).
Titanium is also difficult to manufacture. However, aircraft with titanium skins do exist: one of the most famous is the Lockheed SR-71 Blackbird. During the development of the aircraft, which is part of a family of spy planes with titanium skin, specialized titanium tools had to be manufactured because ordinary metal tools would fracture the more brittle titanium. Coincidentally, the SR-71 included some of the very first carbon fiber composites used in aircraft manufacturing.
Ultem 9085
This thermoplastic is not only 3D-printable; it’s strong, lightweight and flame-retardant. In XB-1, the tertiary bracketry, clamp blocks, spacers, ducts, and fuel closeouts are mostly manufactured in-house at Boom using 3D-printed Ultem 9085.
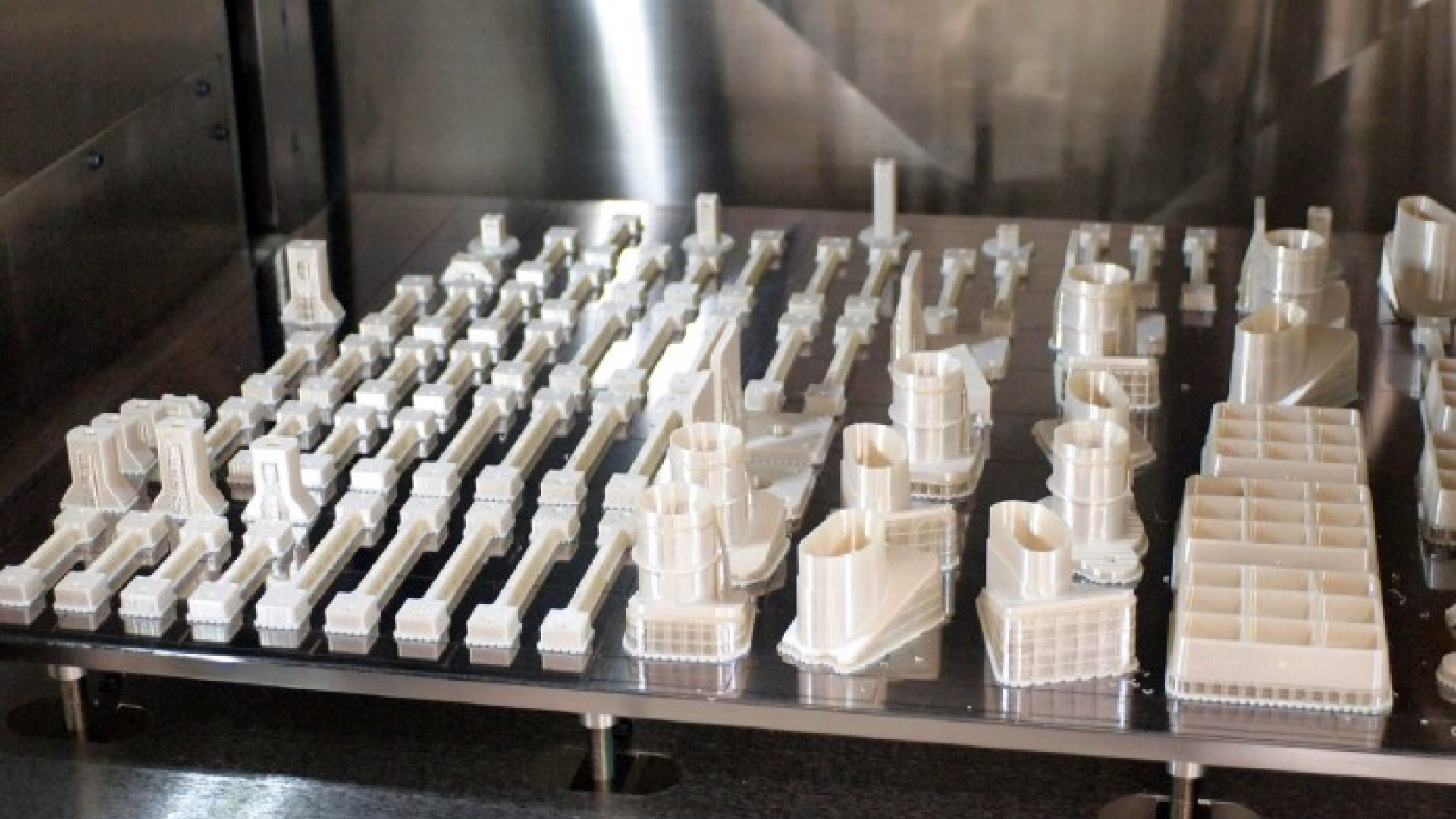
Because it enables quick design iterations, 3D-printed Ultem 9085 can save time and money — one small change will not set the build back substantially. Before the advent of 3D printing, complicated aircraft parts were milled out of a solid block of material, often requiring costly, painstaking and time-consuming endeavors.
Materials that go the distance
While XB-1 features many newer materials, it also includes tried and tested materials such as aluminum, stainless steel, rubber, brass, bronze, acrylic and copper. Each is ideally suited to the specific purpose of each part, and offers the required strength, heat resistance, durability, weight, machinability, and performance for supersonic flight. These are the materials that will go the distance for XB-1 as Boom prepares for rollout and first flight.