From speed skaters to spacecraft, engineers use wind tunnel tests to design for optimal aerodynamics and performance
Wind tunnel testing may harness the power of new technologies, but the concept of testing air flow is hundreds of years old.
For centuries, inventors struggled to replicate how air moves over aircraft, vehicles and other objects. But within the past 100 years, technological advancements have made sophisticated wind tunnel testing a reality for designers and manufacturers of all types of products, including cars, wind turbines, and even clothing.
In anticipation of Boom’s upcoming wind tunnel tests on its supersonic airliner, Overture, here’s a primer on how aerospace engineers recreate the power of wind to optimize aerodynamics and performance for a multitude of designs.
What’s a wind tunnel?
A wind tunnel is a structure that has air flowing through it — usually in the form of a duct through which the air is set in movement by electric-powered fans (or another mechanism to the same effect). The type and size of wind tunnel used depends on the size of the object undergoing testing, as well as the flow conditions desired.
There are many different types of wind tunnels, but they are usually classified based on the speed of operation of the vehicle: subsonic, transonic (ranging between Mach 0.8 and 1.2), or supersonic.
Wind tunnels are routinely used to test aircraft, as well as cars, spacecraft, and almost any engineering application for which the effects of the air flow around a body matter, even golf balls.
Some wind tunnels can accommodate full scale models but, for practicality and cost reasons, most are built to fit miniaturized models. The U.S. is home to some of the largest wind tunnels in the world, at the NASA Ames Research Center in California. The facility includes a 40×80 foot (12×24.3 meter) wind tunnel circuit (pictured below) and an 80×120 foot (24×36.5 meter) test section. It comprises six fans measuring 40 feet (12 meters) in diameter and contains 15 large wood-laminated blades. Each fan blade is 12 feet (3.6 meters) long and weighs more than 800 pounds (362.8 kilograms).
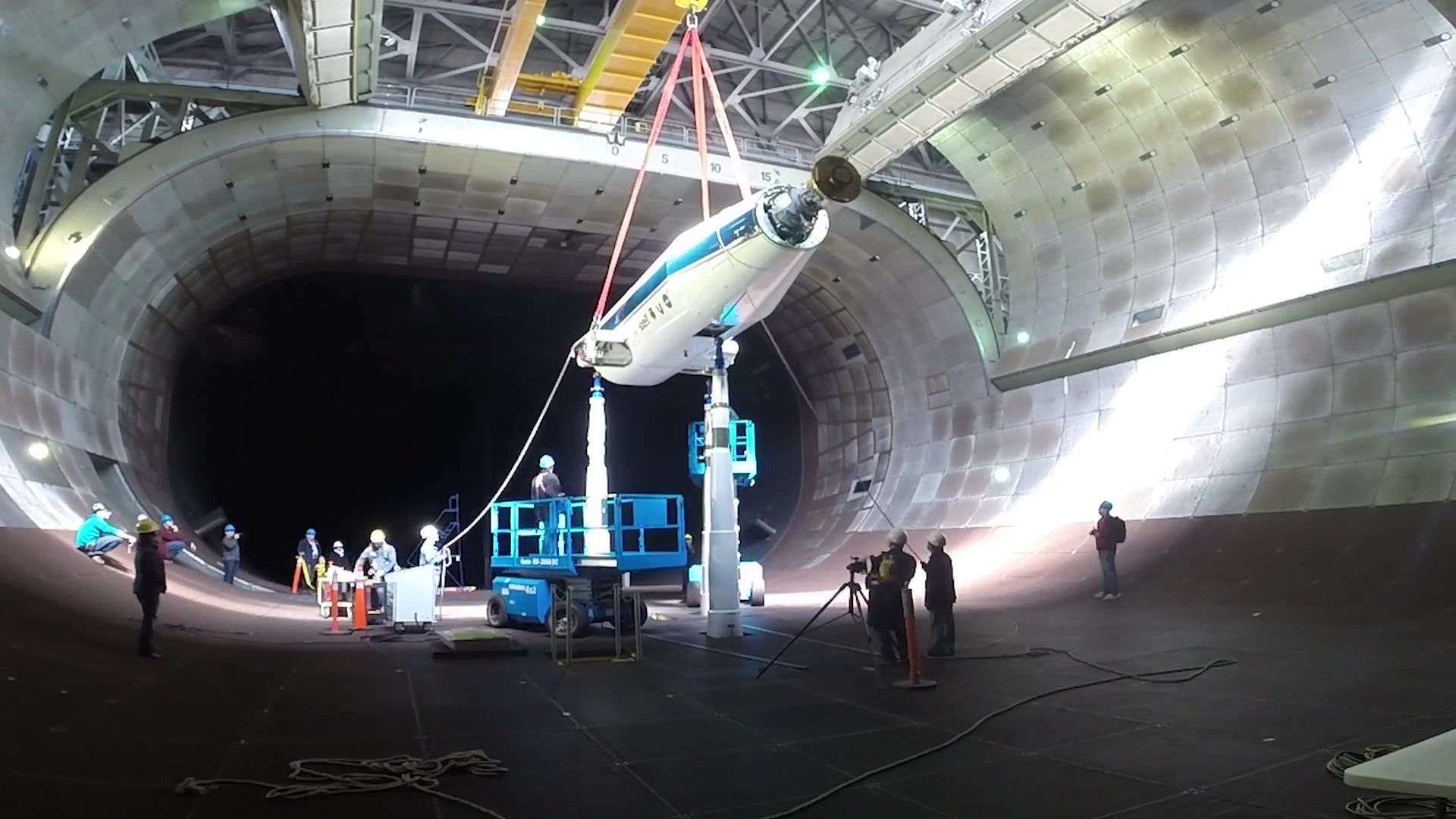
What can you test in a wind tunnel?
Wind tunnels are used to test virtually everything that moves through air, from parachutes and tractor trailers to spacecraft, missiles and drones. Engineers also use wind tunnels to optimize technologies such as floating wind turbines and shipboard helicopter operations (to help optimize rotor blade design and operation under windy sea conditions).
But wind tunnels aren’t just limited to vehicles and objects. Sports professionals and coaches use wind tunnels to test athletes’ aerodynamic drag. Because athletes continuously shift body positions during a sport, engineers measure aerodynamic drag for their primary sport-specific positions.
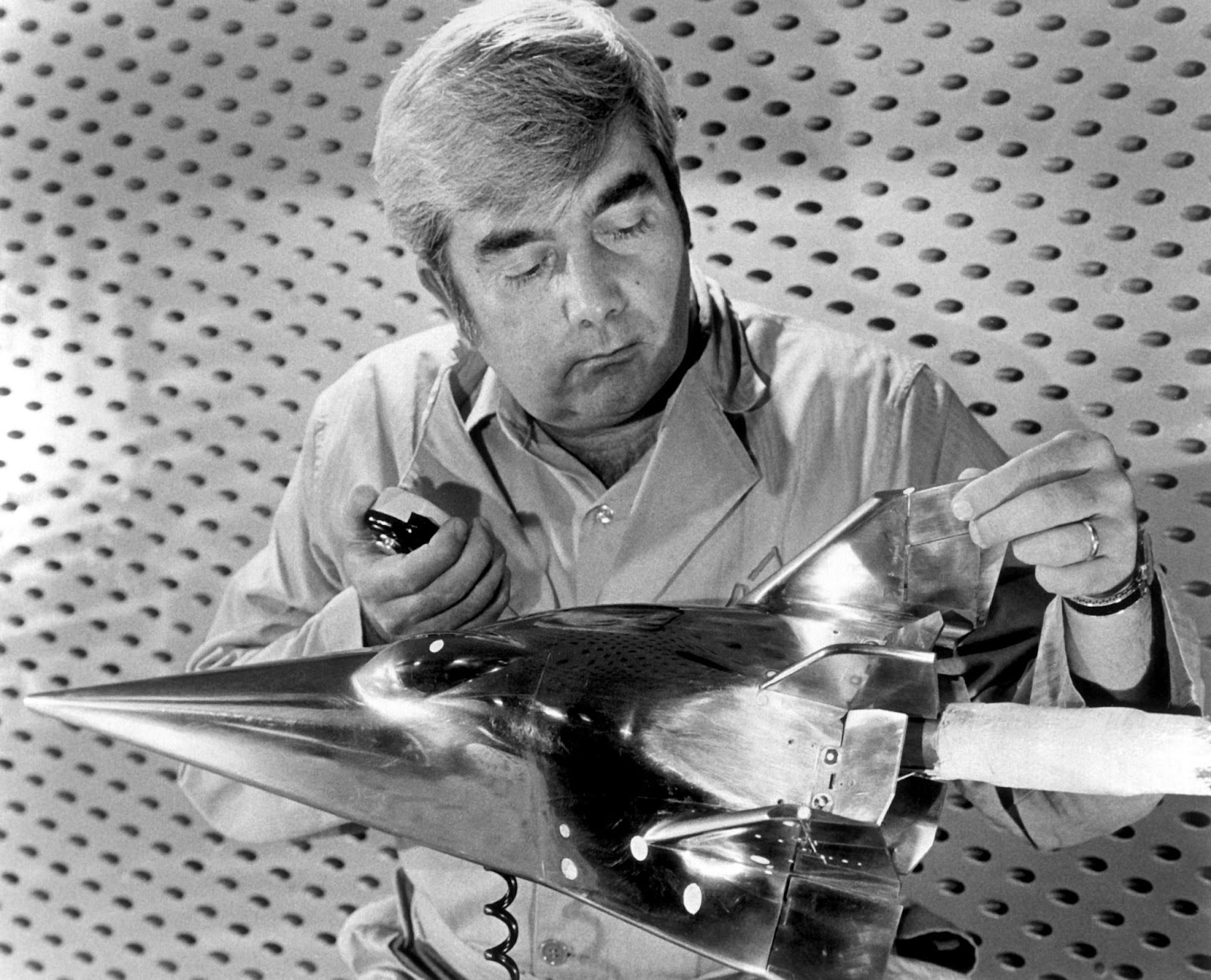
What were the first wind tunnels?
Beginning in the mid-1700s, inventors sought to better understand how air moves over surfaces, and gain an understanding of lift and drag. The advent of the “whirling arm” advanced research, but had its limitations. Some inventors looked to nature to test aircraft in places with consistent heavy winds, but soon realized that it was impossible to reproduce consistent flight conditions on a beach or mountainside.
The first to design a wind tunnel was British engineer Frank Wenham, who realized that by keeping the object still, and blowing air past it, he could learn much more about its aerodynamic performance. Based on his design, the first wind tunnel went into operation in 1871.
How do wind tunnels work?
Wind tunnels generate consistent air flow, usually with electric powered fans. The object undergoing testing doesn’t move. It’s the air that moves around the stationary object, creating the same relative air movement expected in the real-life, as closely as possible. Meanwhile, the aerodynamic forces acting on the object, such as drag and lift, can be measured by accurate load measuring devices. The characteristics of the flow around the object can also be visualized using a number of techniques — smoke injection and oil flow on the test article to name a few — meant to “make the invisible air visible.”
Some of the most powerful electric motors ever built are in wind tunnels. You’ll find them in the propulsion wind tunnel facility at the Arnold Engineering Development Center at Arnold Air Force Station in Tennessee. It’s home to three wind tunnels: the 16-foot (4.8 meter) transonic (16T), 16-foot (4.8 meter) supersonic (16S), and the aerodynamic 4-foot (1.2 meter) transonic (4T). The facility is as tall as a two-story house and as heavy as a railroad locomotive.
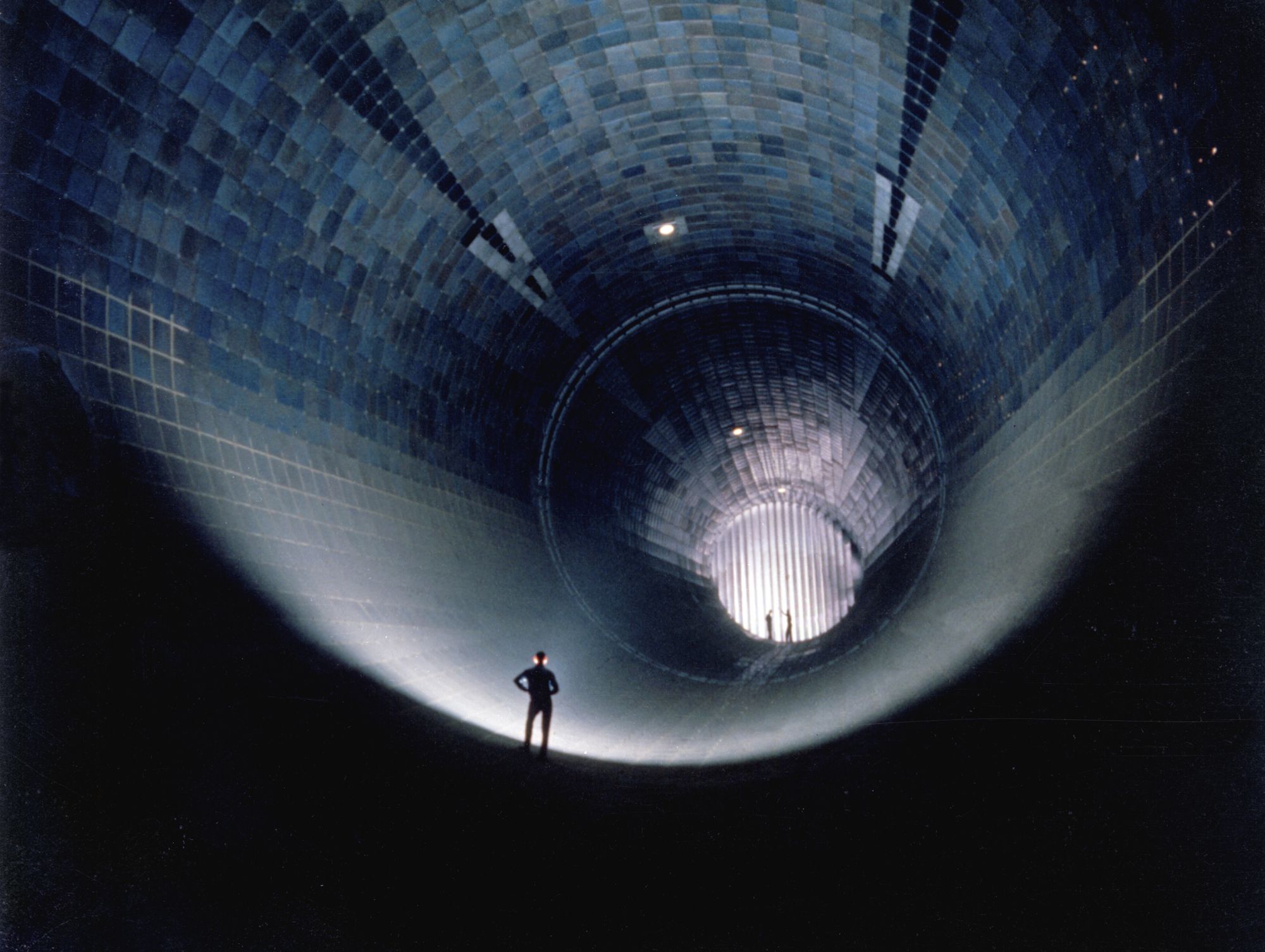
What’s the purpose of wind tunnel tests?
Wind tunnel tests help inventors and manufacturers better understand the nature of flow of air over and around a vehicle or object, as well as the effects it causes on that object, especially aerodynamic forces. Aerospace engineers use the tests to measure an aircraft’s lift and drag properties, as well as its stability. The test results can lead to more aerodynamic and fuel-efficient aircraft designs.
Before the advent of computer-aided design, refining a design required building successive wind tunnel models, which added cost and time delays to aircraft programs. With the advent of computational fluid dynamics (CFD) tools, engineers were able to accelerate the process and test hundreds, if not thousands, of designs virtually. As a result, only the most promising design configurations advance to physical wind tunnel tests, dramatically reducing development costs.
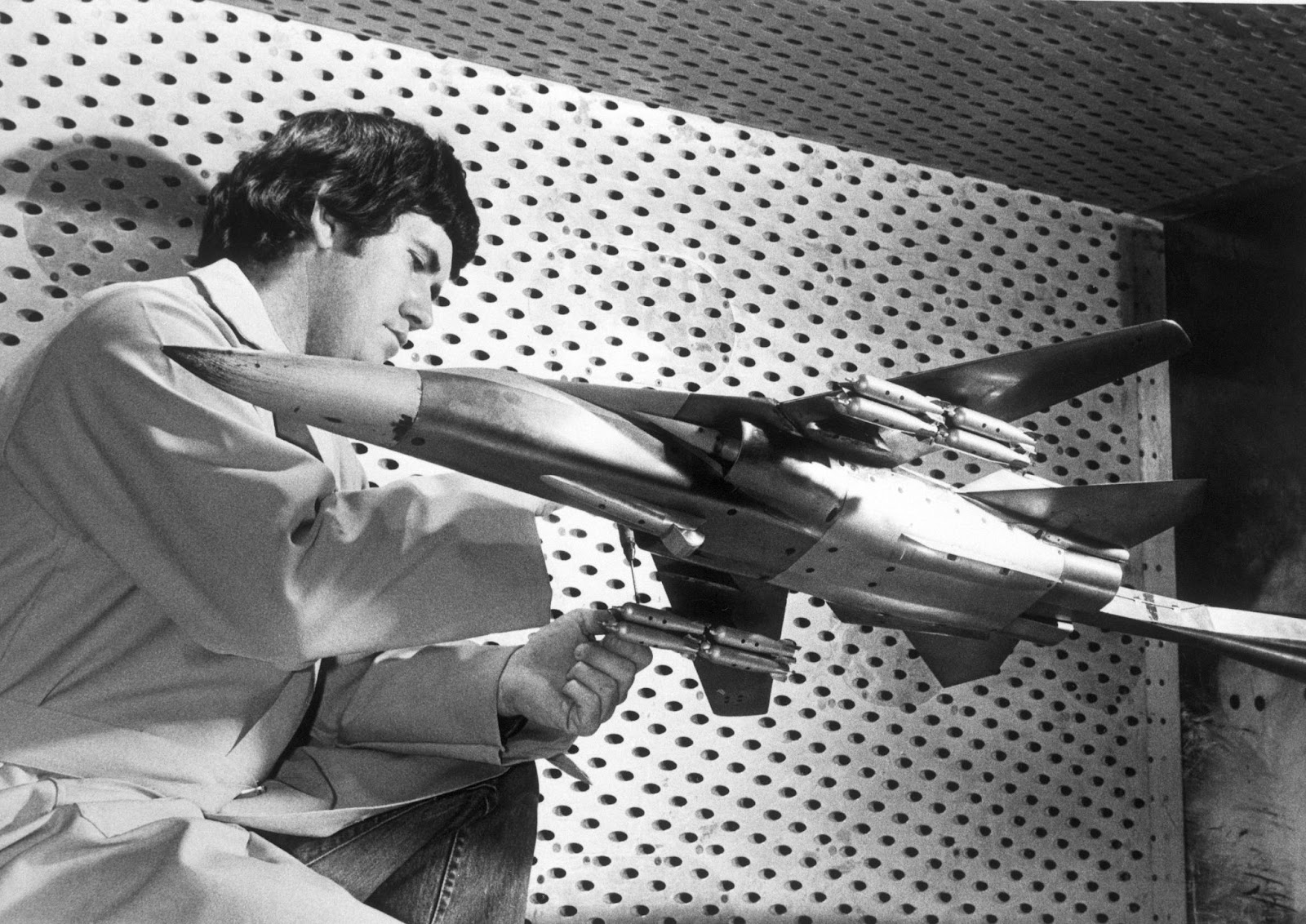
What can engineers learn from wind tunnel tests?
Wind tunnel tests verify engineers’ calculations and identify areas for improvement in their designs. In the case of aircraft, the tests help engineers improve aerodynamic performance — reducing drag and increasing lift — while ensuring the aircraft will be stable and controllable. And when aircraft have better aerodynamic performance, they’re more fuel efficient because they require less power to travel through the air.
Do acoustic engineers also use wind tunnels?
Acoustic engineers use wind tunnels to measure the sound vehicles generate as they move through air. Test findings help them to validate predictions and refine designs, which ultimately yields quieter aircraft and a better experience for passengers.
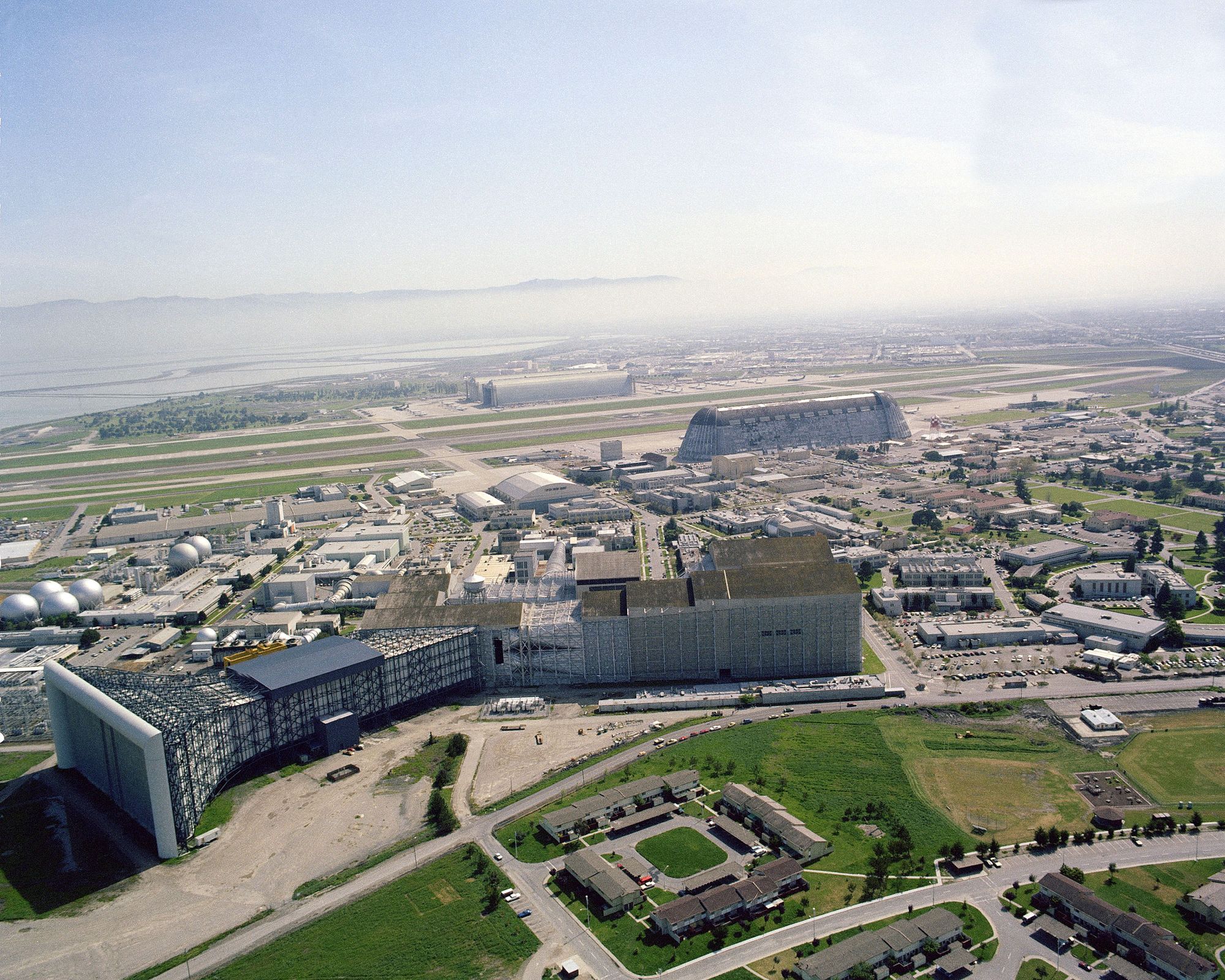
When will Boom begin wind tunnel testing for Overture?
Boom will begin wind tunnel testing for Overture in late 2021. During multiple rounds of testing, the engineering team will test Overture models in five wind tunnels, located in Europe and the U.S. Testing will range from low-speed airframe acoustics to high-speed aerodynamics. The team completed wind tunnel testing for XB-1, the company’s supersonic demonstrator, in 2017 and has carried this experience forward into the extensive series of Overture tests.
Stay tuned for more updates about Overture’s wind tunnel testing from Boom’s aerodynamics and propulsion teams.
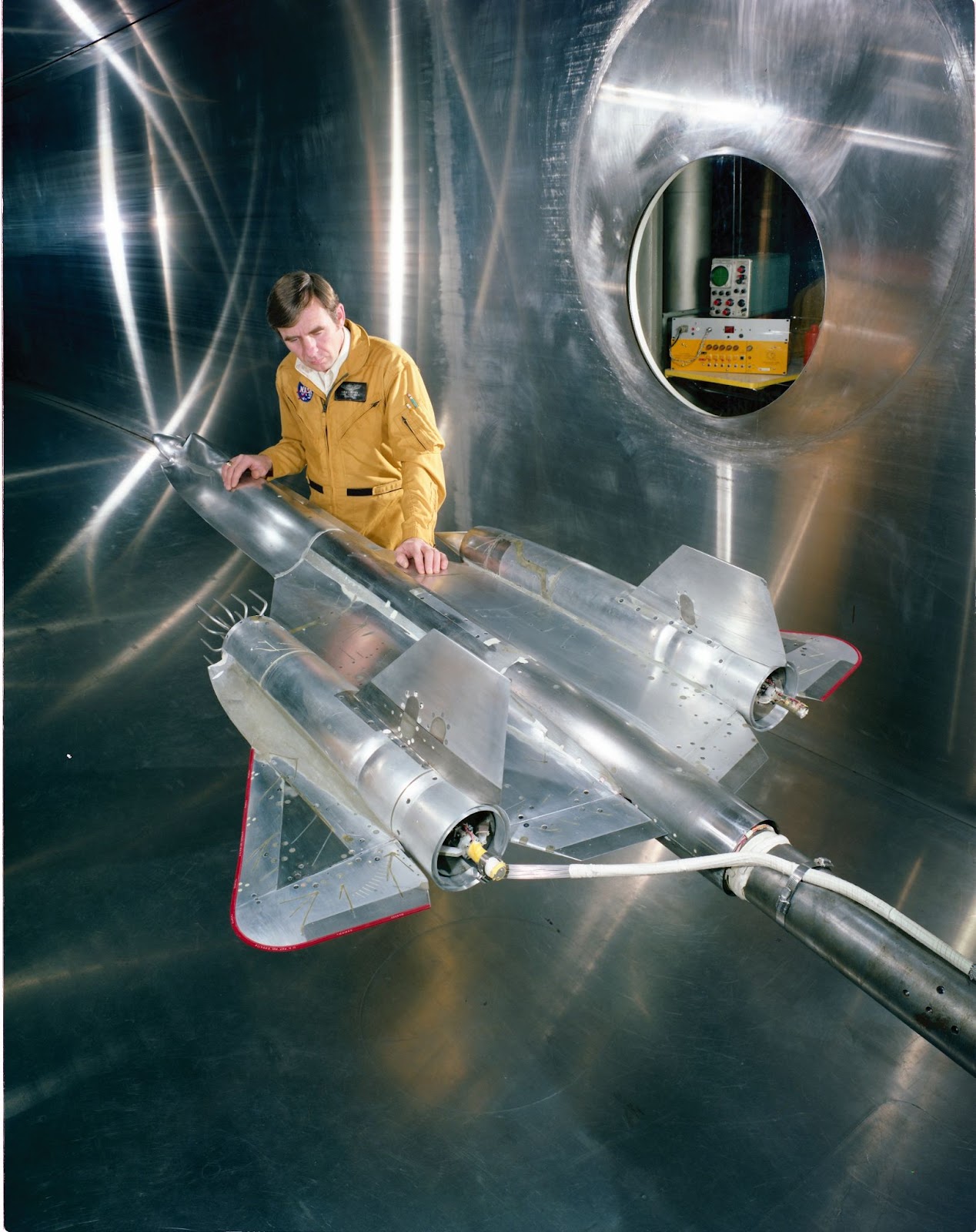