In October 2019, human factors evaluations transitioned from testing in the XB-1 simulator to XB-1 itself when our demonstrator aircraft underwent ergonomics testing with Boom test pilots Bill “Doc” Shoemaker and Chris “Duff” Guarente.
From simulator to cockpit
Following two years of rigorous testing in Boom’s in-house simulator, ergonomics tests began under the direction of the flight control systems team.
“Apart from validating findings from the simulator, verifying ergonomics as early as possible in the design process helps us to remove risk from the aircraft build, not to mention flight test schedules,” explained Erin Young, Lead Flight Control Systems Engineer. “It’s also a critical component of safety testing for any aircraft and will be used repeatedly throughout the design process.”
Data from the simulator has already provided the team with invaluable key learnings for flight characteristics. Subsequent tests in the aircraft are ensuring that the ergonomics assessments made in the simulator, which may not reflect XB-1 geometry with complete accuracy, represent how pilots fit in the aircraft as the build progresses.
Ergonomics (or human factors) is the scientific discipline concerned with the understanding of the interactions among human and other elements of a system, and the profession that applies theory, principles, data and methods to design in order to optimize human well-being and overall system performance. – International Ergonomics Association Executive Council, August 2000
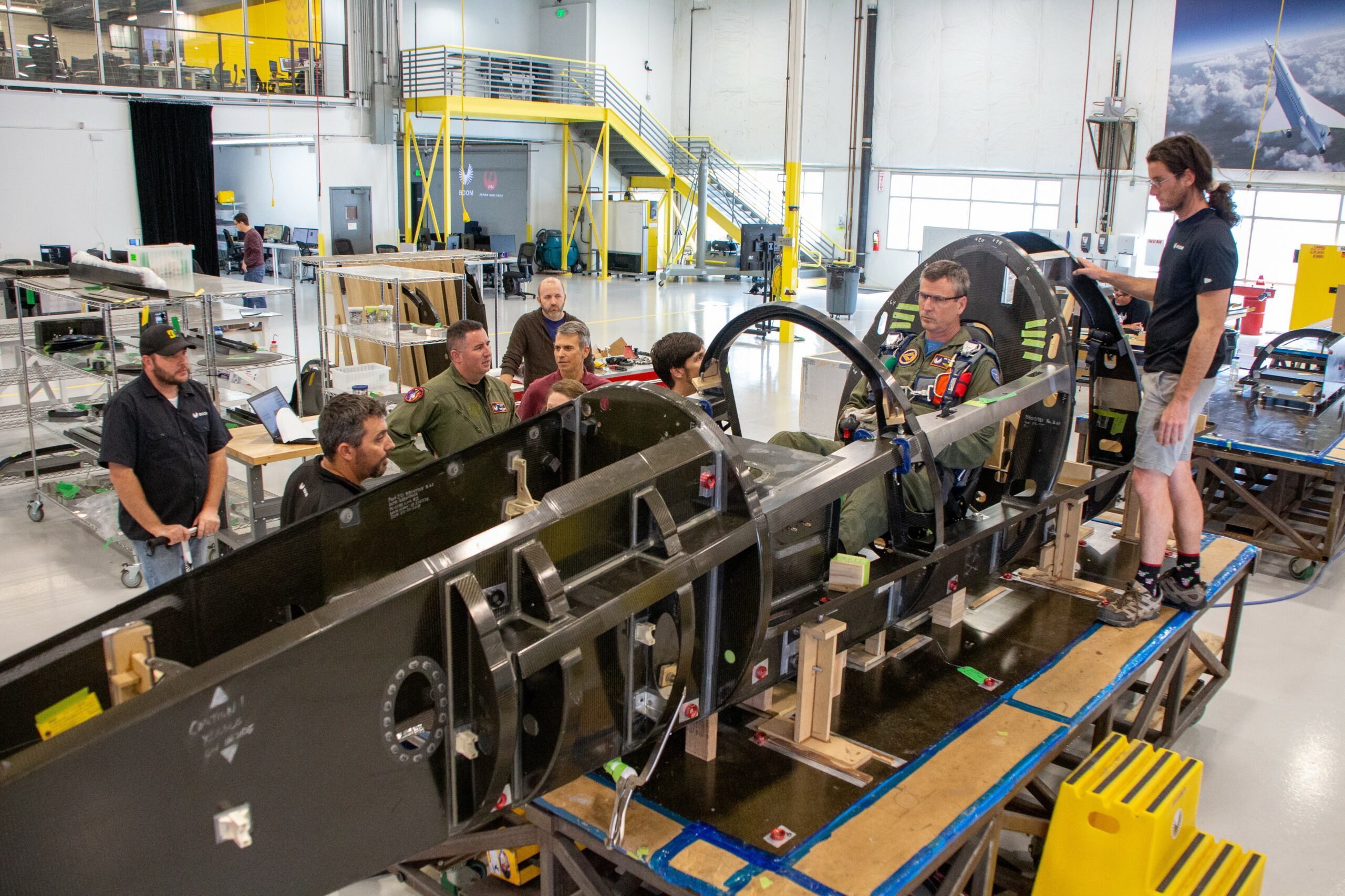
Tailor-made for two test pilots
“Getting to where we are evaluating the actual airplane is a testament to our progress,” said Shoemaker. “It’s exciting to be literally surrounded by flight hardware. Everything’s coming together in the hangar.”
Unlike commercial, military or private aircraft that must fit a very broad range of people, XB-1 is built for only two pilots. As a result, Boom had a much tighter range for design. (Typical aircraft are designed to fit people whose anthropometric characteristics fall within the 5th and 95th percentile of a population. In the case of XB-1, our fit was narrowed to just two test pilots, which allowed for a faster design process.)
Like all aircraft, the cockpit is designed around the “design eye point” — the location of the pilot’s eyes and what they see. It’s essential for landing (ensuring pilots have good visibility) and for instrument layout (confirming instruments are easily visible). If all pilots were the same height, one solution would fit everyone — but that’s not the case for XB-1. As a result, Boom designed the rudder pedals, seat harness and the seat knowing that at least two pilots are going to fly the aircraft while also confirming that, regardless of height, their eyes are always in nearly identical locations.
Boom isn’t the first aerospace program to address different pilot heights. Space programs including Mercury, Apollo and Soyuz famously made casts of each astronaut’s back and legs to build a custom, individualized seat. In XB-1, the same seat was originally placed in our flight simulator for testing. Subsequent ergonomics testing in the actual aircraft with the same seat helped us to verify what we learned in the simulator, and make minor yet highly important changes.
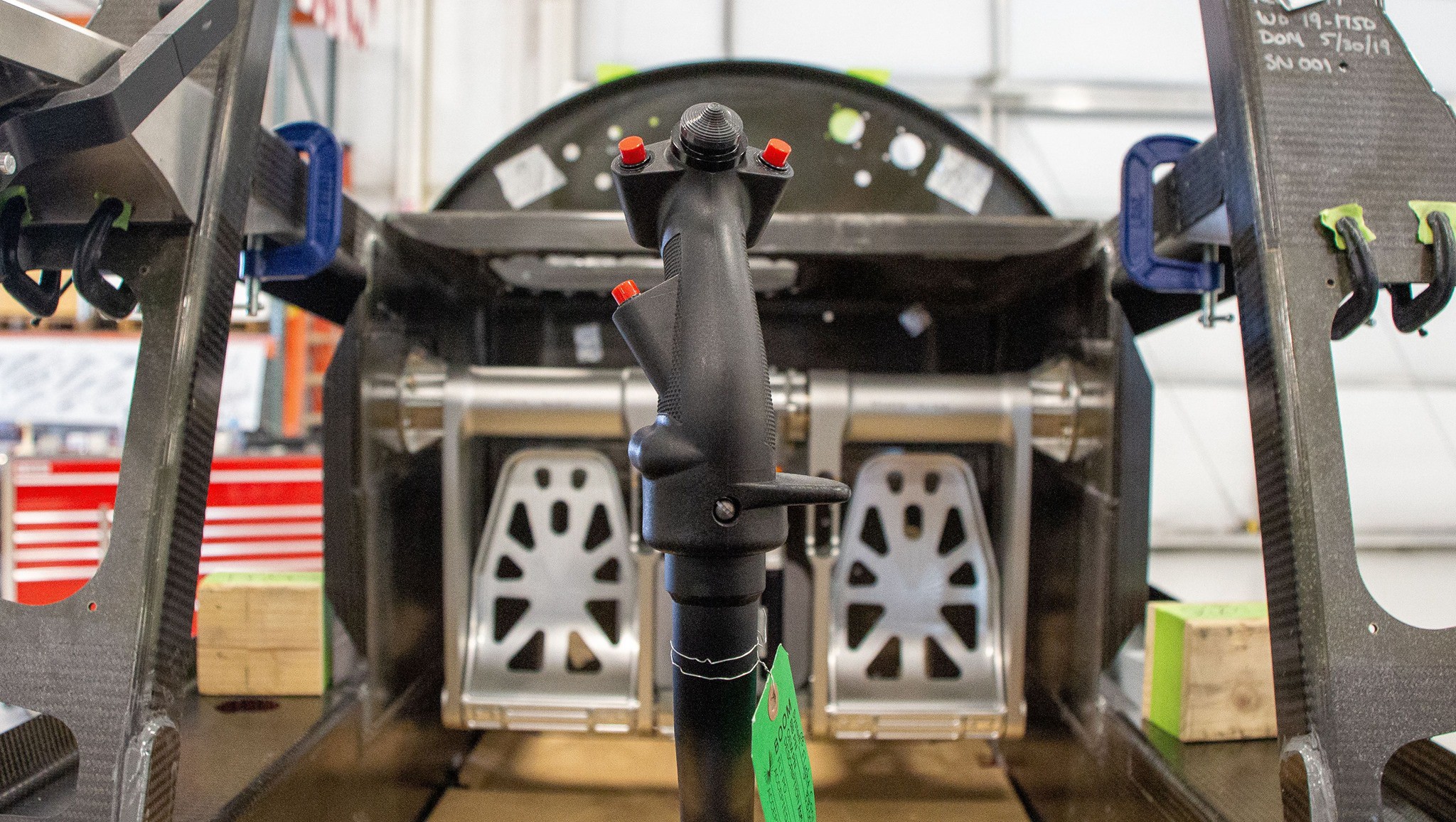
Phase One: Seat, Harness and Mobility
Margins are very tight in XB-1 and while the cockpit isn’t cramped, it’s not a large space. Dimensions are partly driven by weight: every pound of weight saved in the cockpit is another pound of fuel that can be used to fly XB-1 longer at supersonic speeds. As a result, it’s built for purpose rather than comfort.
The entire system of seat, harness and flight controls is highly sensitive to small changes, especially as bodies are incapable of sitting in exactly the same position twice. Our initial phase of ergonomics testing focused on:
- Ensuring the stick and throttle are in the correct position, and verifying that pilots can reach all buttons and switches in the aircraft while seeing them clearly, whether the shoulder harness is locked or not
- Verifying that equipment attached to pilots, including the oxygen hose and communications cord, is within easy reach — and not in the way of anything they need to be able to see or touch
- Establishing that our taller pilot has full mobility, as well as clearance with the canopy, with his helmet on
- Confirming the basic location of the rudder pedals to establish the distance required to fit either pilot
- Identifying concerns with the shoulder straps, which will require additional work to ensure the pilots can easily put them on and take them off
Simulator and ergonomics testing allowed us to establish ideal settings for XB-1 based on our two test pilots. As the build progresses, we’ll return for regular human factors evaluations in both the simulator and XB-1.
“At Boom, where we see aircraft parts manufactured in the hangar, performing XB-1 ergonomics testing provided a huge sense of progress for the team,” said Charlie Hoffert, Structures Engineer. “It’s part of what makes Boom special — the aircraft is getting assembled literally steps away from where the pilots sit, allowing for easy communication and regular ergonomics check with the entire team.”