It’s been 50 years since the first Concorde aircraft took to the airways. During that time, aerospace engineering has advanced with a speed that would thrill even the original Concorde team. We’re inspired by what the Concorde team accomplished and immensely proud to carry that legacy forward.
At Boom, we’re applying decades of knowledge to develop Overture, a supersonic aircraft that is dramatically more fuel-efficient and cost-effective. Here are the top three differences between Overture and Concorde in aerodynamics, materials and engines.
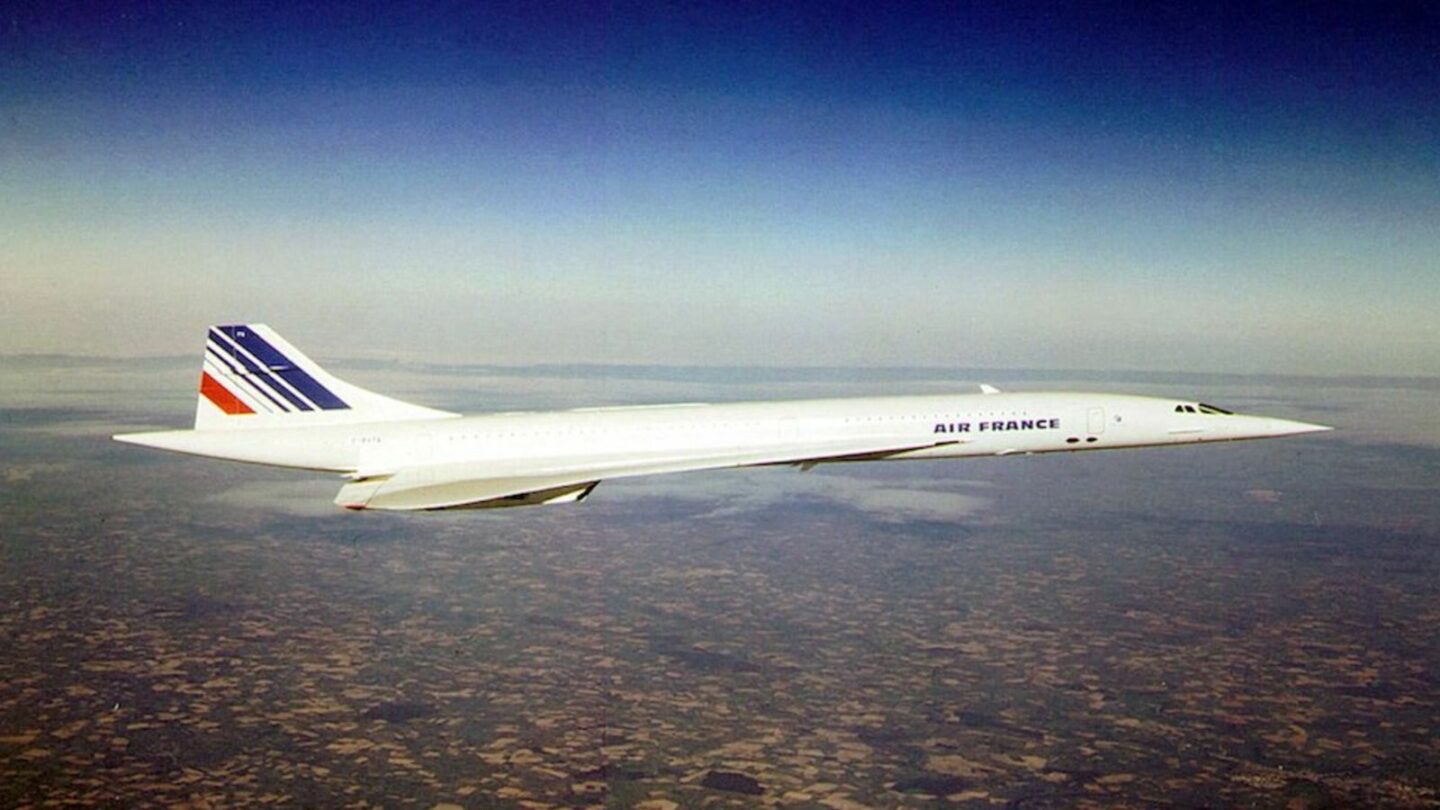
Aerodynamics
Compared to Concorde, Overture is much more aerodynamically shaped — thanks in part to new materials such as carbon composites. For example, the fuselage is “area ruled,” meaning the cross-section area is carefully controlled to reduce disturbances to the surrounding air (aka drag). Concorde’s designers knew of this principle, but it wasn’t feasible to realize in aluminum at the time. Fast-forward 50 years and we have the advantage of new materials. Since today’s carbon composites are molded, it’s possible to create a strong and lightweight structure in any dynamic shape desired.
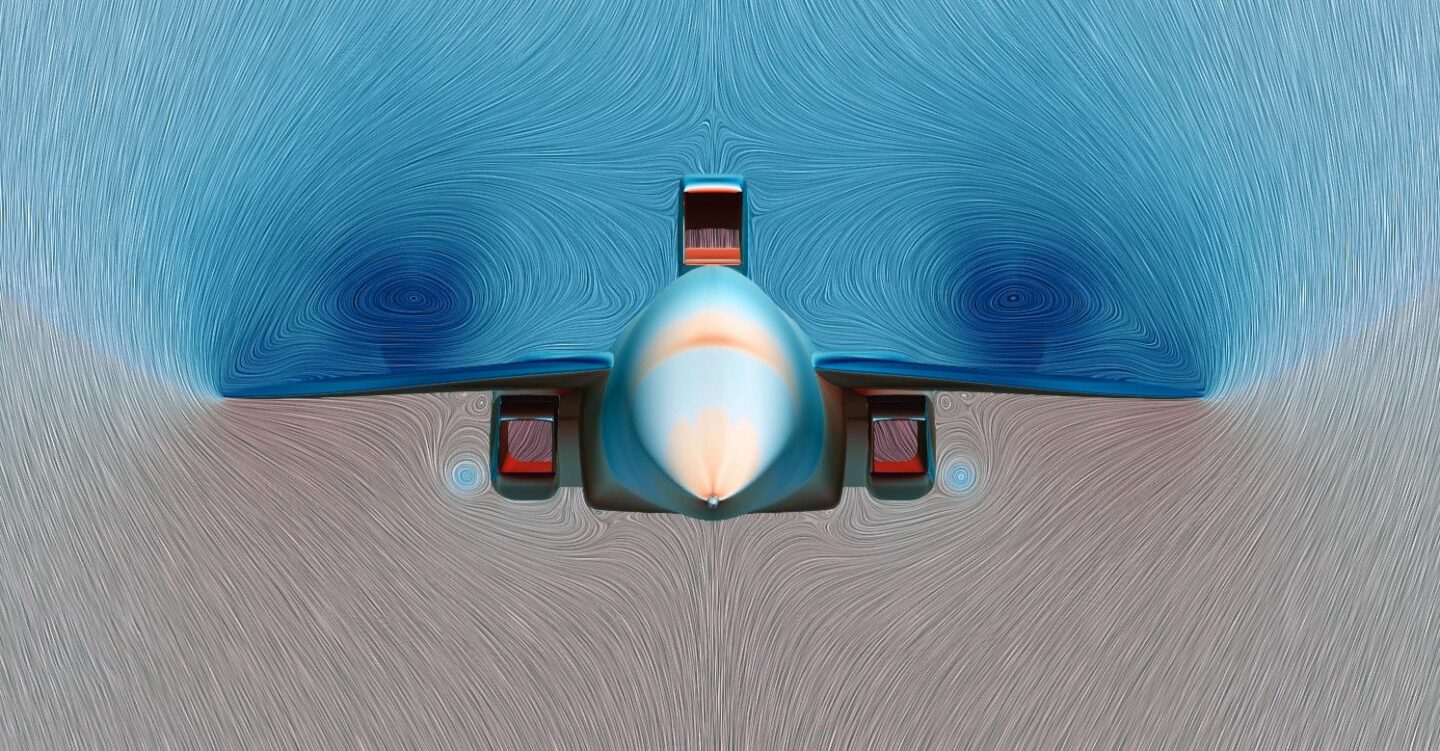
Boom also has the advantage of iterating and testing designs in hundreds of computer simulations, which were unavailable to Concorde engineers. While Concorde’s highly-advanced wind tunnel required months and millions of dollars per iteration, Boom engineers can take advantage of dramatically faster computational design techniques. For example, Computational Fluid Dynamics (CFD) software reduces the design cycle from several months to a few hours or days.
Materials
Speed is no longer limited by materials. Overture’s carbon-based material systems can handle temperatures well above those encountered at Mach 2.2.
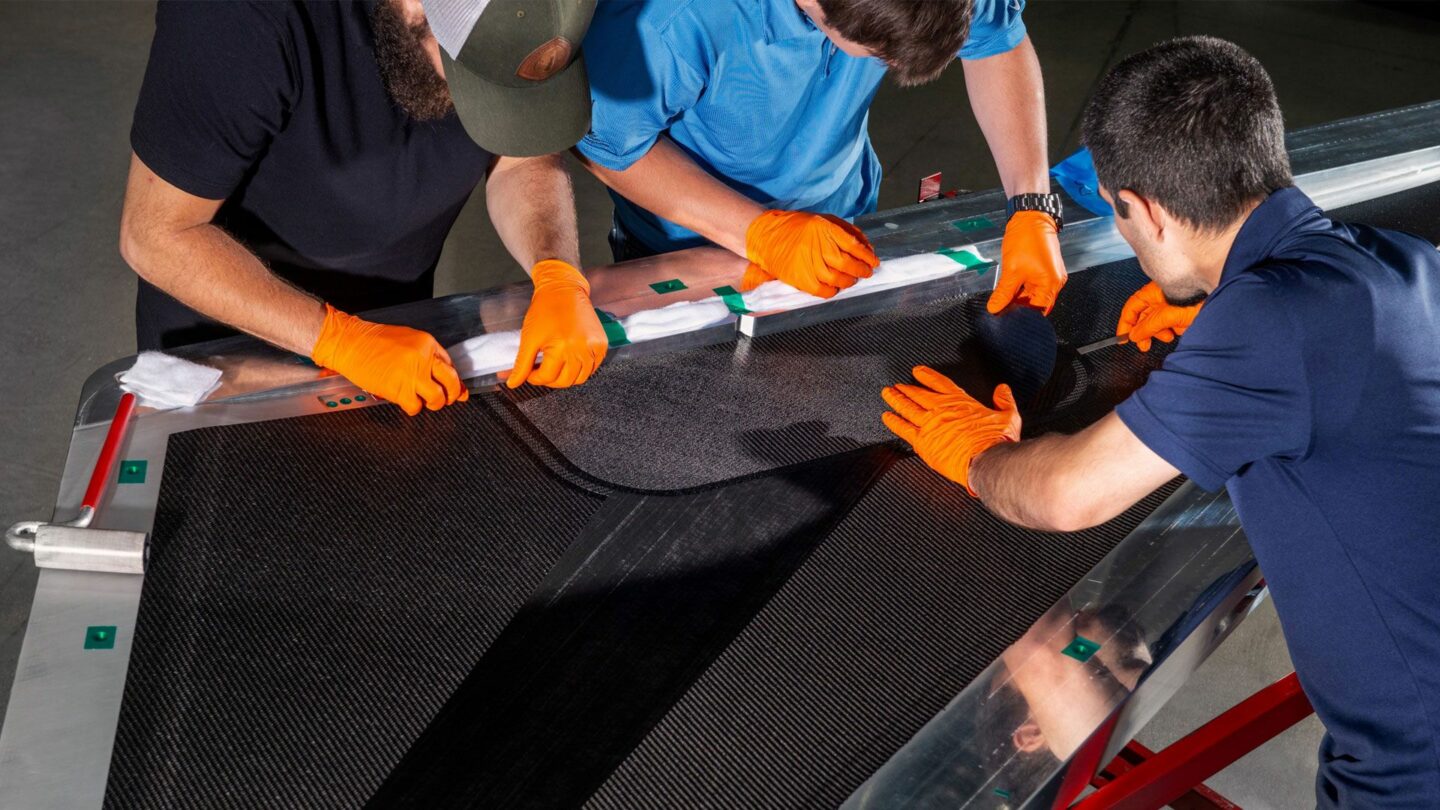
Concorde’s aluminum-alloy airframe was lightweight but would expand and contract up to 30 cm at the high temperatures of supersonic flight. (The faster an aircraft flies, the higher the effective ambient temperature.) The aluminum alloys available to Concorde’s designers couldn’t withstand the high temperatures required at Mach 2.2, but today’s carbon-based material systems can.
Overture’s carbon-fiber composites maintain strength at elevated temperatures better than aluminum. The composites also expand and contract much less than metal under Mach 2.2 conditions, allowing Overture to fly at higher speeds.
Engines
Today, we have vastly improved turbofan engines, which can produce enough thrust for supersonic flight while also being quiet and friendly around airport communities. There’s no need for an afterburner, which Concorde used for takeoff and to break through the high-drag transonic barrier.
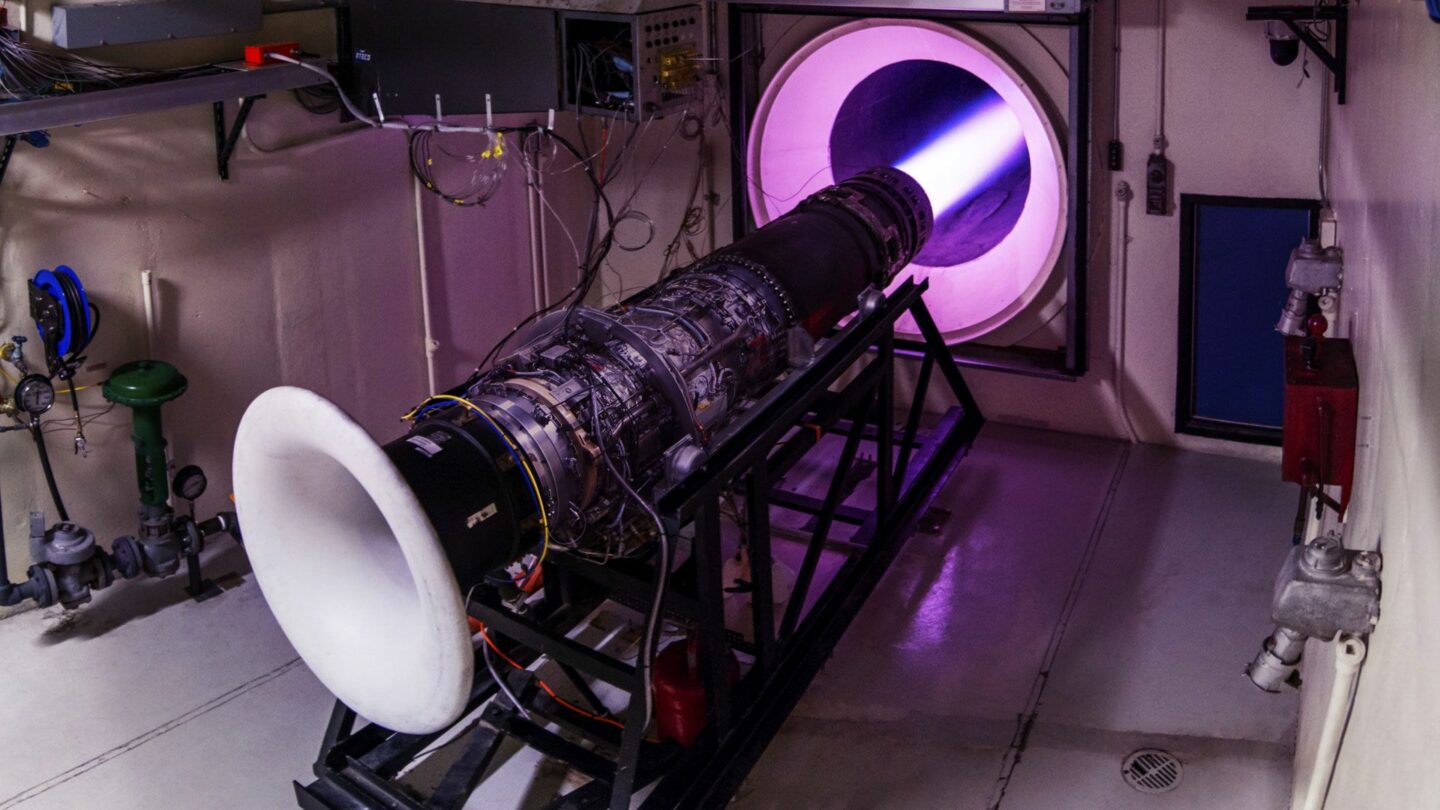
Concorde’s four Rolls Royce/Snecma Olympus 593 turbojet engines provided the thrust necessary for cruising and landing. However, Concorde required the additional thrust of afterburners during takeoff and to reach supersonic speed (for acceleration and climb from approximately Mach 0.9 to Mach 1.7). Besides being loud, afterburners were also very inefficient. For example, during takeoff Concorde’s afterburners increased fuel consumption 78% while adding only 17% in extra thrust.
When design is complete, Overture’s three medium-bypass engines will also be quieter and cleaner, and won’t require afterburners. Boom is targeting fuel-burn parity with subsonic business class. We’re also testing alternative fuels to substantially lower Overture’s carbon footprint.
All of us at Boom are inspired by what Concorde’s engineers and designers accomplished. We look forward to making supersonic travel — and our planet — more accessible with Overture.