Drag = Fuel Consumption
One of the most vital goals of aerospace engineers is to create minimal disturbance to the air flowing around the aircraft. For supersonic aircraft, this is paramount. When an aircraft redirects incoming air at supersonic airspeeds, it creates shocks. The pressure of the air increases across these shocks and causes “wave drag” on the aircraft. The more the air is redirected, the stronger the shock. With a stronger shock comes more drag. And that means more power — fuel — is required to move the aircraft.
Fuel efficiency is directly tied to how much drag an aircraft generates because all drag must be overcome with thrust from engines. Naturally, more drag means more thrust, which results in more fuel burn and less efficiency.
Advanced Manufacturing = Improved Aerodynamics
One issue common to supersonic aircraft is that the point where the wings attach to the body represents a large increase in the amount of air being redirected, relative to the slim nose. This causes substantial wave drag, which was one of the primary sources of inefficiency for Concorde.
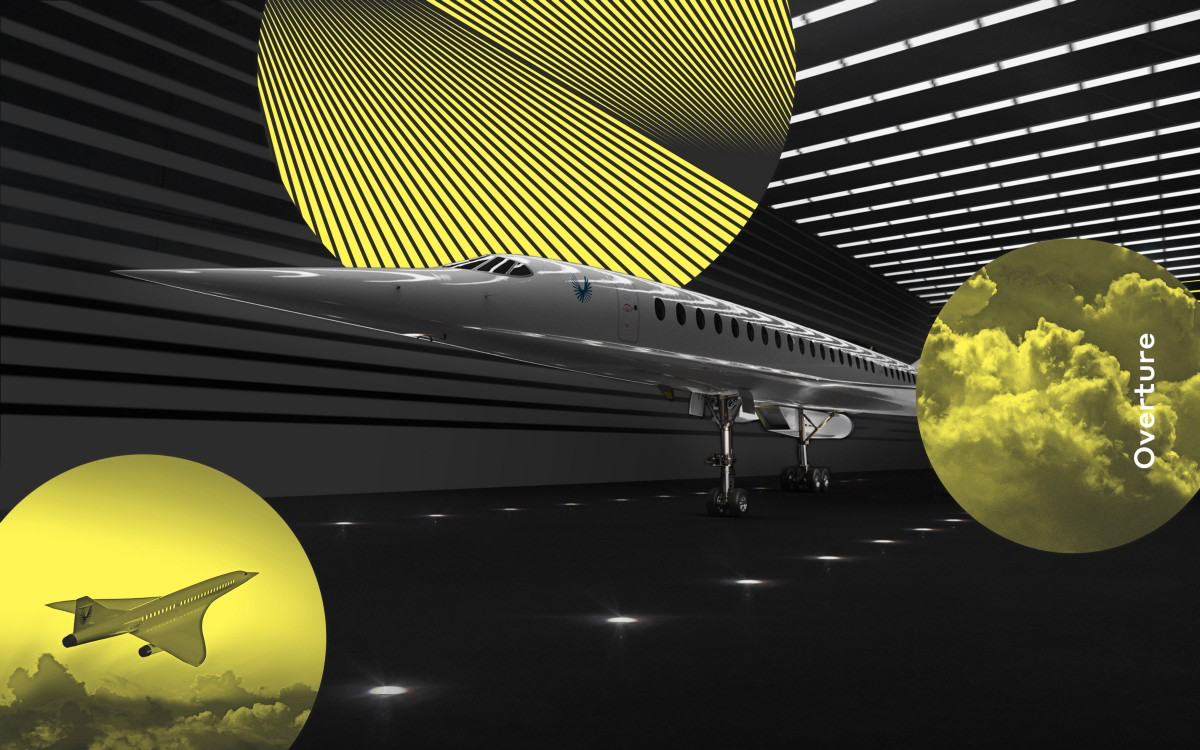
Overture’s design will significantly decrease the drag created at supersonic cruise conditions. Overture has the benefit of advanced manufacturing techniques, such as carbon fiber composites, which allow for the tapering down of the size of the fuselage — and thus redirecting less air and reducing the amount of wave drag. This concept is known as “area ruling.”
One aspect to note is that Overture will look quite different from Concorde. With so few supersonic aircraft ever produced, there are no prescribed solutions in place when it comes to aerodynamics. Unlike subsonic aircraft, such as the Boeing 767, which have been studied and tested since the 1980s, supersonic aircraft offer engineers the opportunity to explore options to achieve optimum design. As a result, Boom engineers have more trade space—more opportunities to evaluate, test and improve aerodynamics.
How does drag impact speed and efficiency?
A good example of how drag impacts speed is a motorized boat. At low speeds there is considerably more drag on the hull as the boat displaces water. The boat’s engines must work harder to part water as it moves through it. But at high speeds, the drag is significantly reduced because water is pushed under and around the boat. You can feel the sensation of reduced drag anytime you zip along in a boat powered by an outboard motor.
In the case of hydroplane boats, the hull’s shape allows it to “plane”—to “fly”— across the water. Drag is significantly reduced at very high speeds as the hydroplane glides on top of the water (rather than pushing it aside). In fact, a hydroplane boat in racing situations probably isn’t touching the water at all; hydrofoils (the boat’s foils or wings that are usually submerged underwater) create lift so the boat’s hull is completely outside the water.
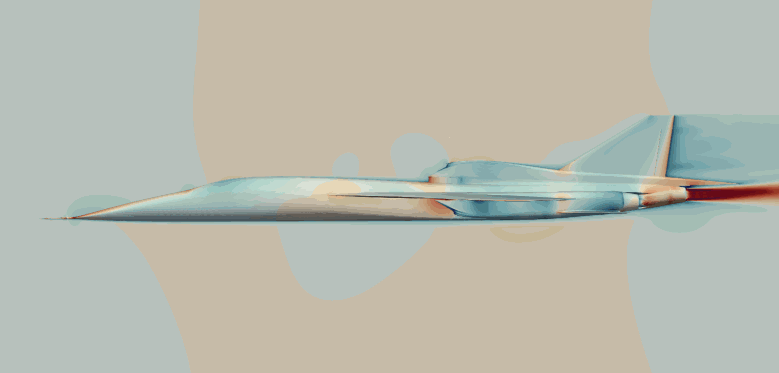
Reduced Drag = Greater Efficiency
In the case of aircraft design, the goal is to have the highest lift to drag ratio or L/D ratio (pronounced “L over D ratio”) to improve efficiencies. Not surprisingly, gliders have the least amount of drag. The Eta glider, for example, has an L/D ratio of 70, which means that for every pound of drag, it can make 70 pounds of lift, or for every one foot it descends, it can cover 70 ft across the ground.
Every type of aircraft must reduce its profile to reduce drag. It must also overcome the drag that it generates with thrust from its engines. At supersonic speeds, the drag “penalty” for redirecting significant amounts of air is magnified. That’s why engineers create long, slender supersonic aircraft with pointed noses and tapering fuselages. As a result, all supersonic aircraft are shaped the same way to be as aerodynamic as possible.