One milestone stands apart in the build of XB-1: the closeout of the wings. It’s an exceptional procedure because there’s no going back once the wings are closed. The team must get it right the first time — and that’s exactly what they did with a finely-orchestrated operation in the hangar.
XB-1’s wings are now officially closed out and ready for installation into the fuselage. Weighing in at 507 pounds — a relatively modest weight considering XB-1’s wingspan is 21 feet — the wings still required the use of a small forklift to move and flip safely.
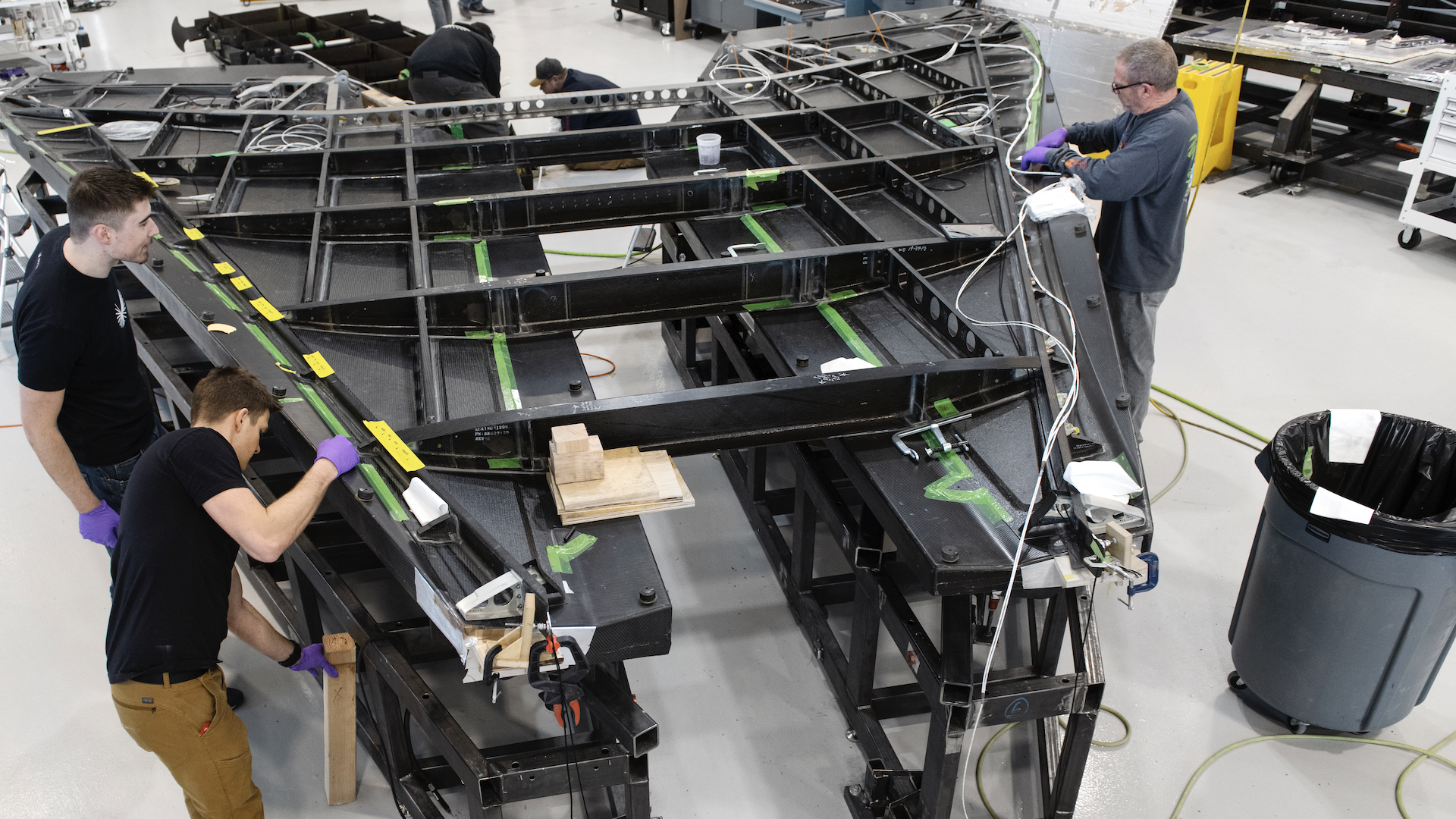
“The closeout of XB-1’s wings marks a significant milestone for the major structural assembly,” says Boom’s Head of XB-1 Production, Mike Jagemann. “It’s significant because of the finality of the event—once you close them out, you cannot go back and open it like you could a bolted structure. After we install a few more parts, such as the leading edges, the wing will be complete and moving on to structural testing.”
Since November, cross-departmental teams have worked together to establish best practices, draw on one another’s expertise, and document every step of the closeout process. Departments including Flight Controls, Hydraulics, Avionics, and Structures, as well as Boom’s two test pilots and the crew chief, offered insights and guidance as the build out of the wings progressed. Following the successful installation of XB-1’s seven wing spars and two aileron trays in January, dress rehearsals for the closeout got underway.
The closeout process is relatively simple, yet requires the highest level of precision possible. During the preparation phase, the team:
- Installed the upper wing skin into its holding fixture
- Bonded all spars and ribs into the upper skins — also known as the substructure
- Installed flight control brackets and pulleys
- Installed wire harnesses and instrumentation
On closeout day, the team ran concurrent safety checks to ensure the proper installation of hardware such as temperature gauges inside the wings, and that all cable bundles ran correctly through each wing. The team also inspected flight control pulleys and cables, which are routed through the wings to the systems bay, as well as the aileron trays on the outboard portion of each wing. (Ailerons are the hinged part of each wing that control roll or maneuvers, and are controlled by the pilot via wire pulleys that run through the wings.) A final bond line inspection and FOD (Foreign Object Debris) check also ensured that any and all foreign objects were removed before close out.
With the wings ready for final closeout, the operation got underway. The team dedicated the day to:
- Grit blasting the entire bonding area on the substructure, as well as the lower skins in their bond areas to remove dirt and dust particles
- Meticulously cleaning surfaces
- Loading the upper skins into a custom-build vacuum fixture
- Applying adhesive to the substructure (both the spars and the ribs in the upper skin)
- Flipping a custom vacuum fixture over to the proper orientation
- Lifting the vacuum fixture and wing skin with a lift boom on a forklift
- Moving the vacuum fixture and skin into position, and also lowering the skin into position
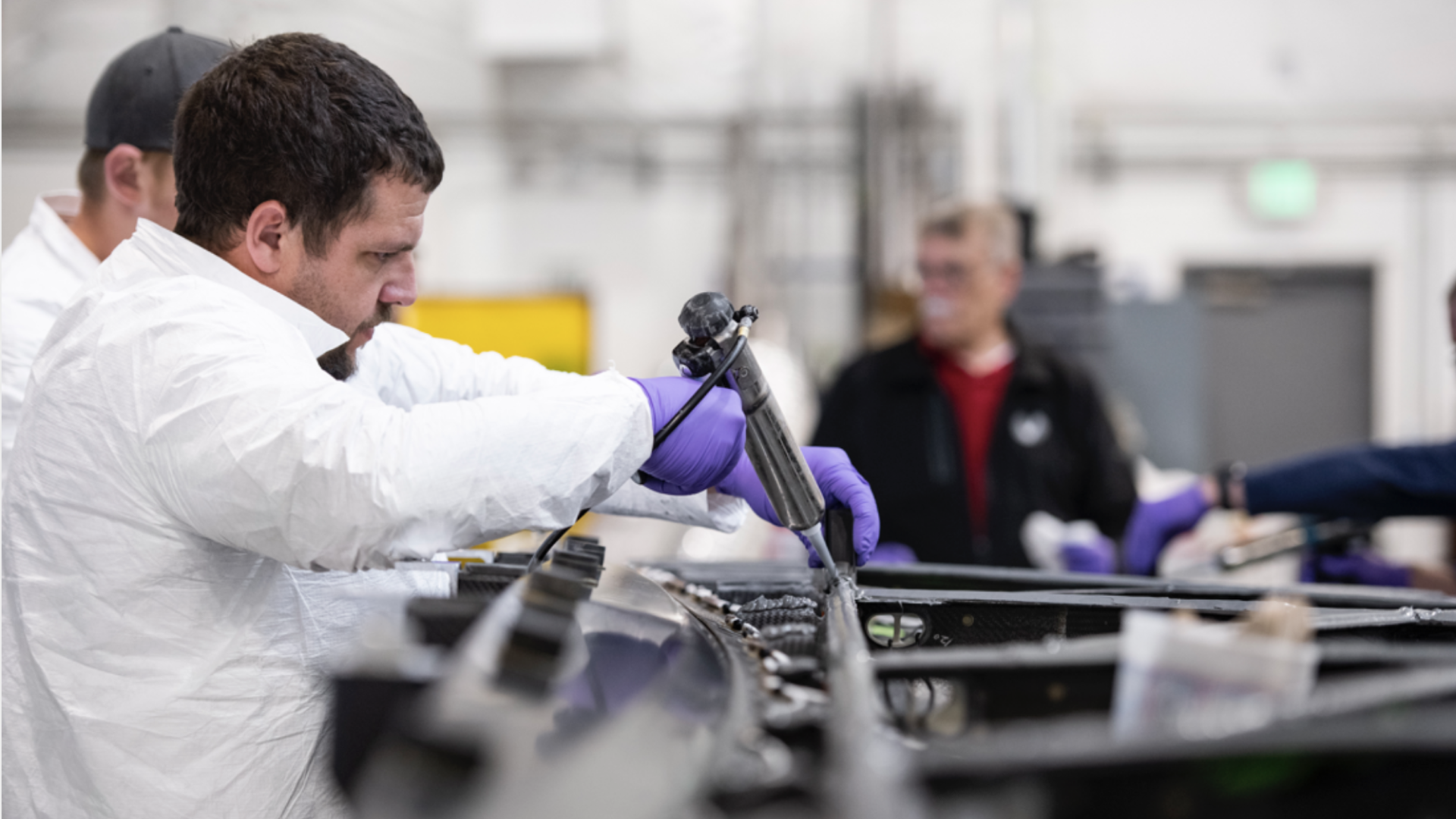
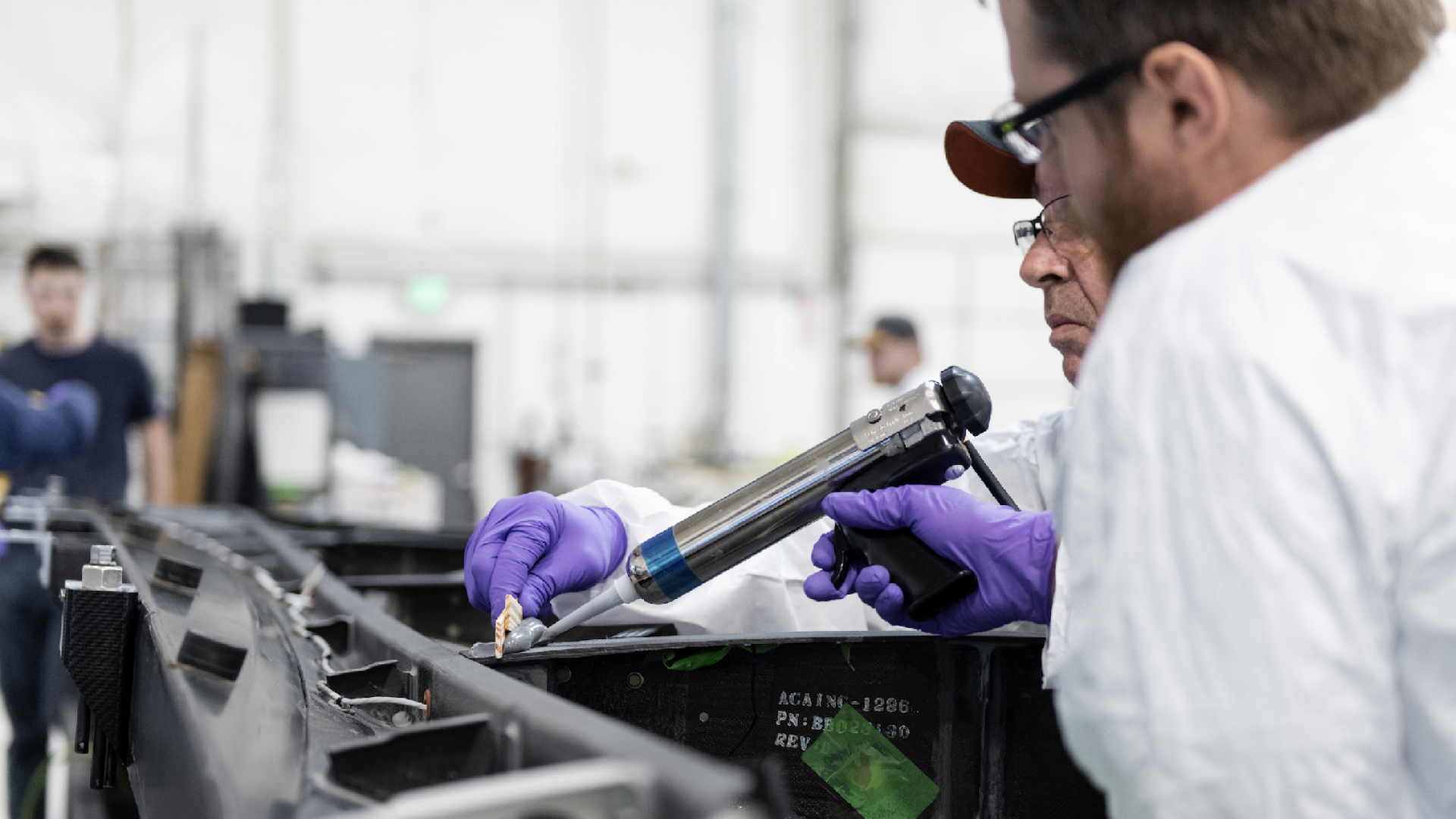
During the application of the adhesive along the bond lines, the team placed lines of clay to capture any shift in position, ensuring bond line acceptance in the skins. With razor-tight margins (+/-.020″ of the wing’s profile), the team measured the bond lines to within 0.005— 0.100 of an inch.
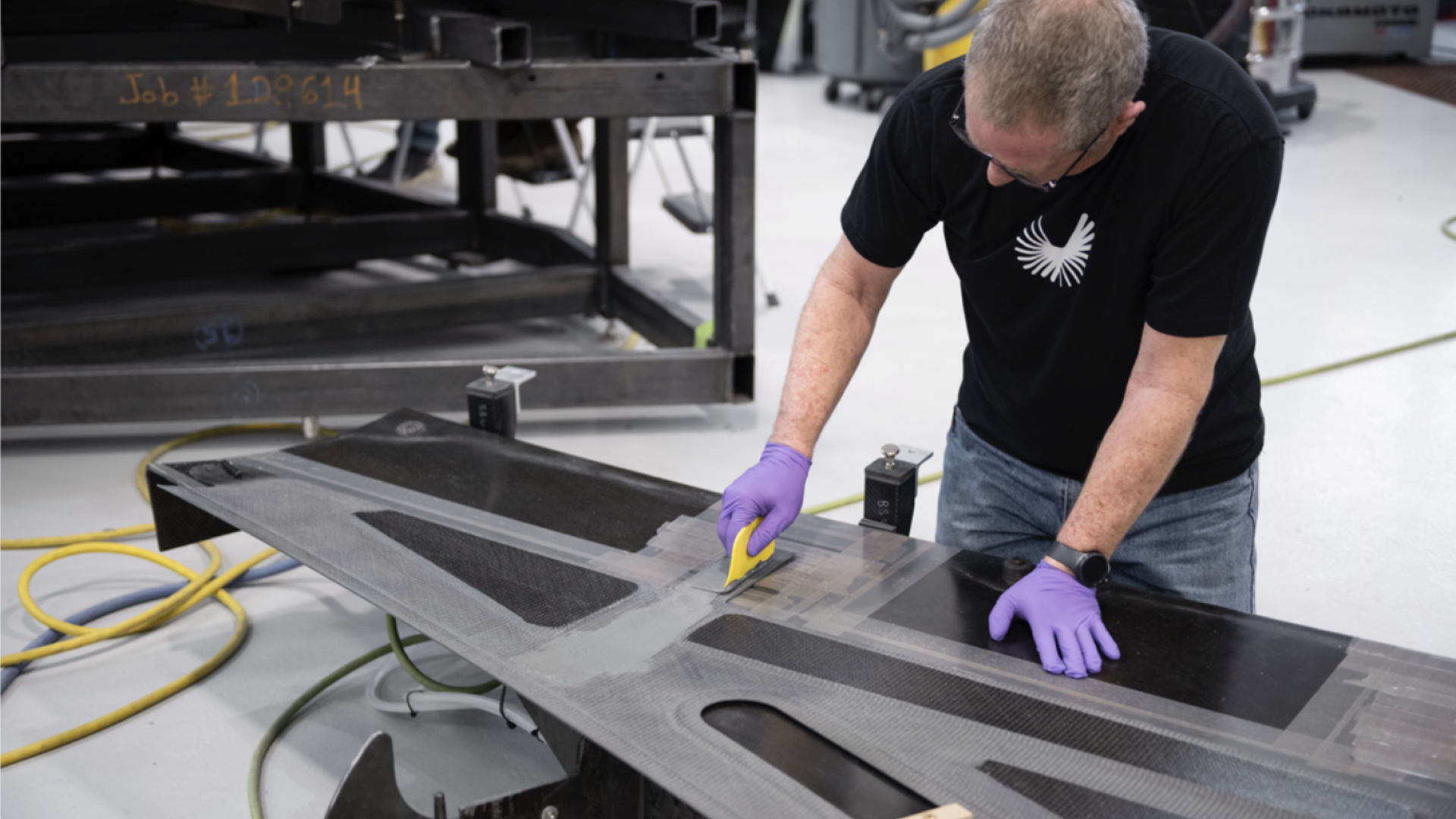
It was critical that the team work quickly, yet precisely, because there is only an eight-hour time window from application of the adhesive to when the part must reach the ideal curing temperature. As work progressed, team leaders signed off on specific aspects of the closeout. Boom’s two test pilots were also onsite to verify that all aspects of the wing met their approval.
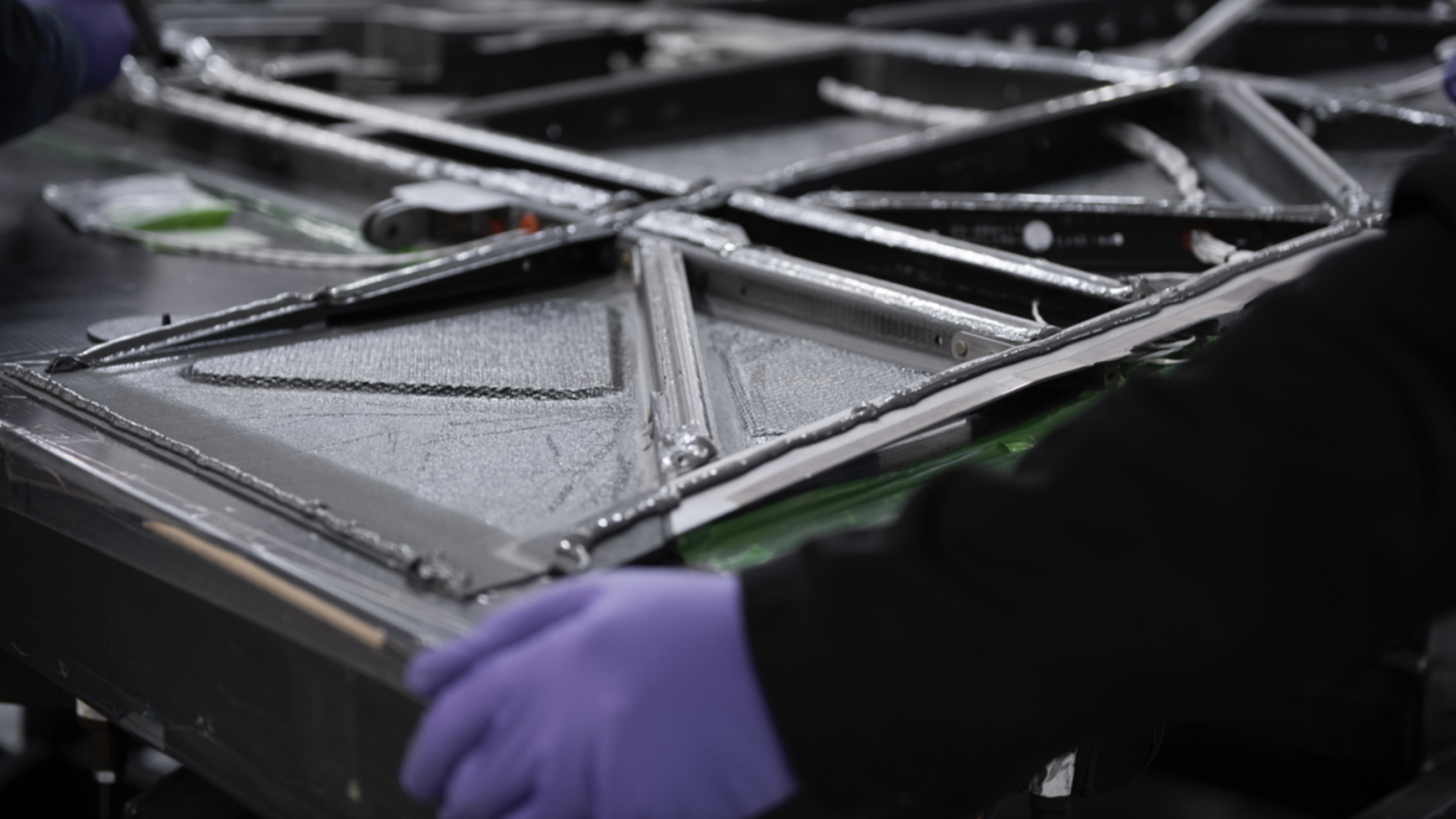
In the coming months, the entire wing structure will be tested and subsequently installed into the fuselage, sealed, and bonded into place. The Boom team is eagerly setting its coordinates for the Mojave Desert to put the wings into action.
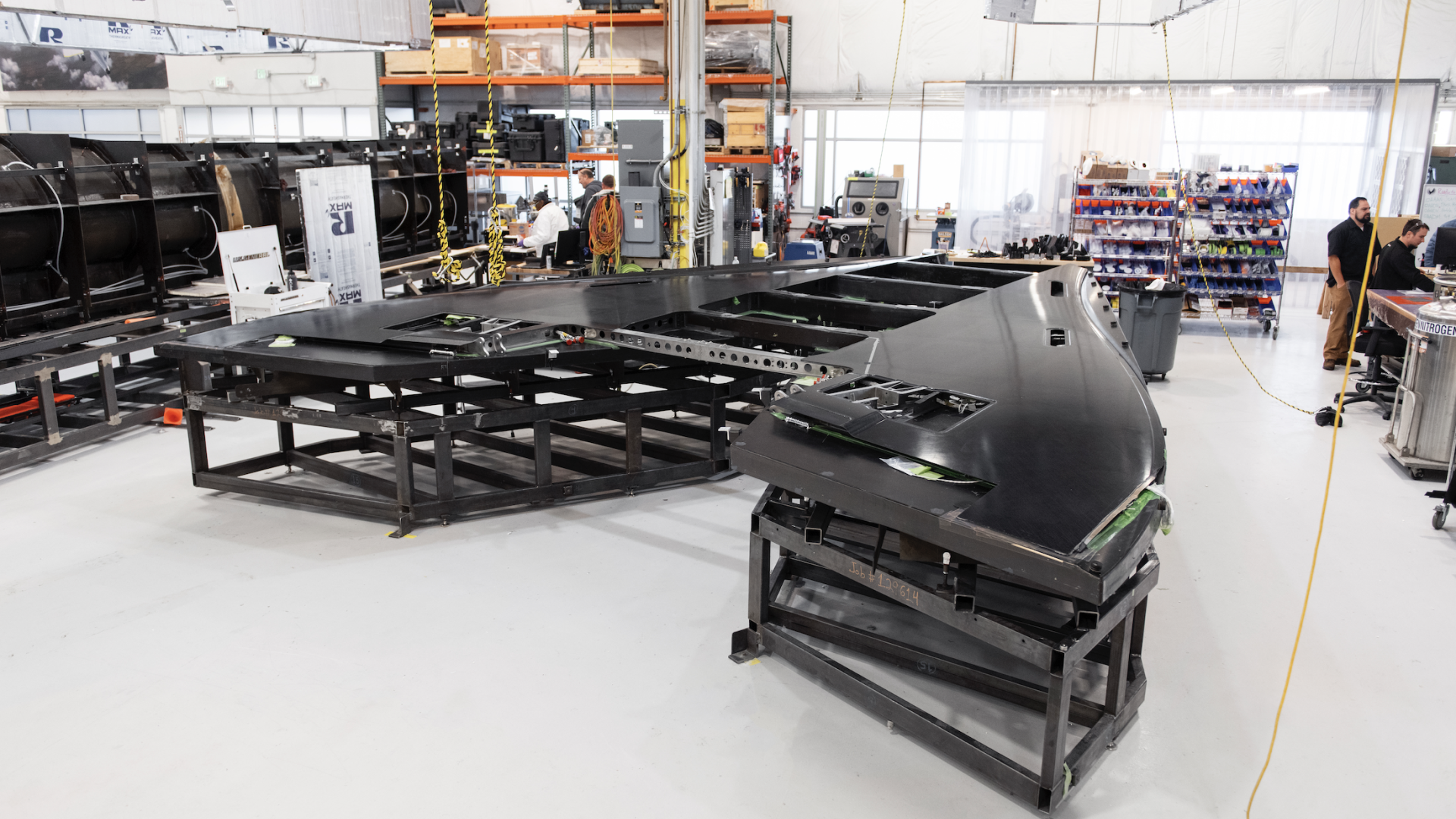
Did you know? XB-1’s wings comprise one single structure. Unlike large commercial aircraft that have individual wings, which are manufactured and attached separately, XB-1’s wings are a solitary piece. Due to the nature of the design, the team began the process with the wings “upside down” and then flipped them with a forklift to complete the closeout.