XB-1 Goes Mach 1
Mach 1.122
(750 mph) MAX AIR SPEED
34 MIN
Time in air
35,290 FT
Altitude
Boomless Cruise with XB‑1
Flying at Mach 1.1, no audible boom reached the ground.
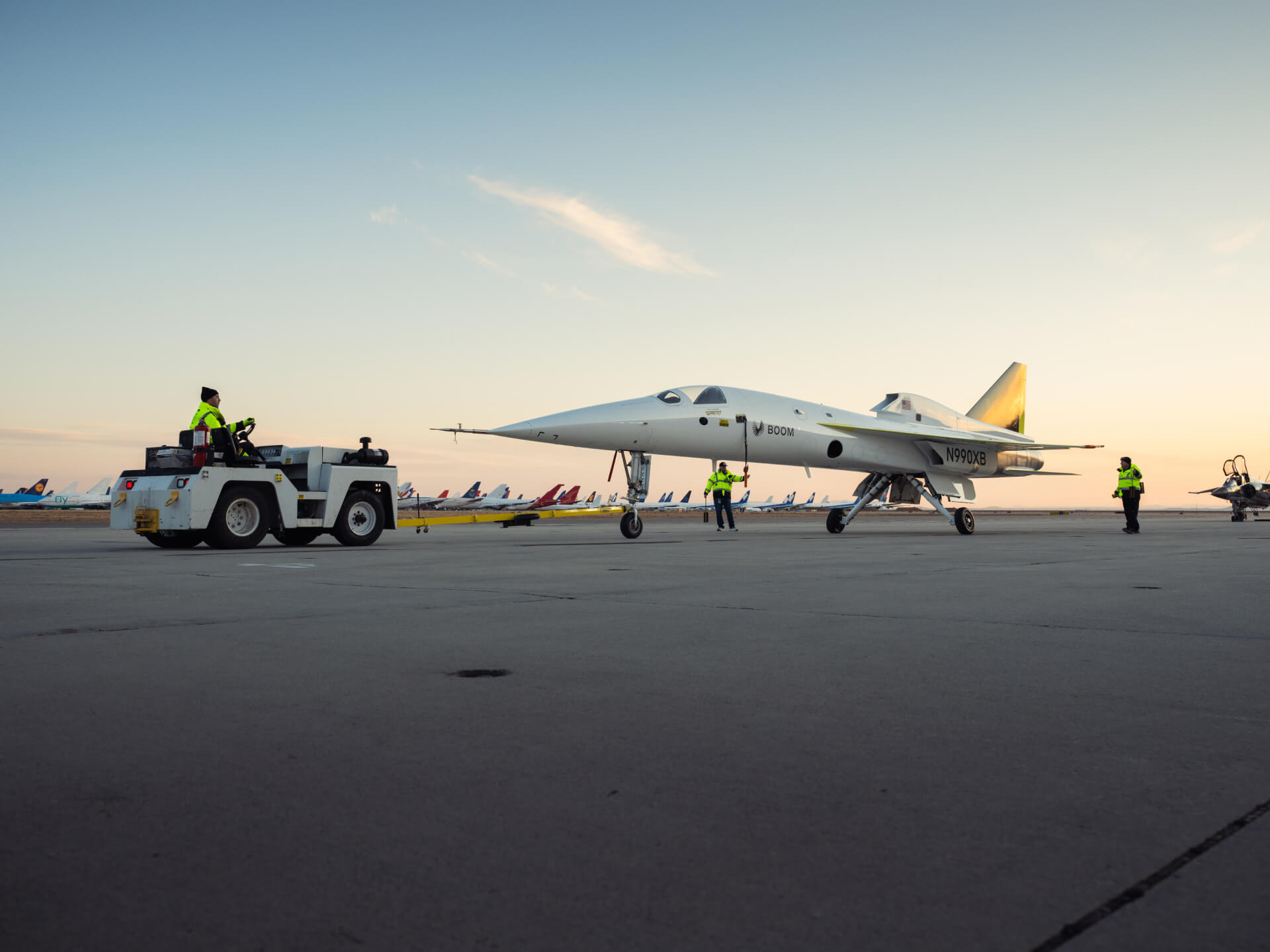
Watch XB-1’s Second Supersonic Flight
FEB 10, 2025
Watch XB-1’s Historic First Supersonic Flight
JAN 28, 2025
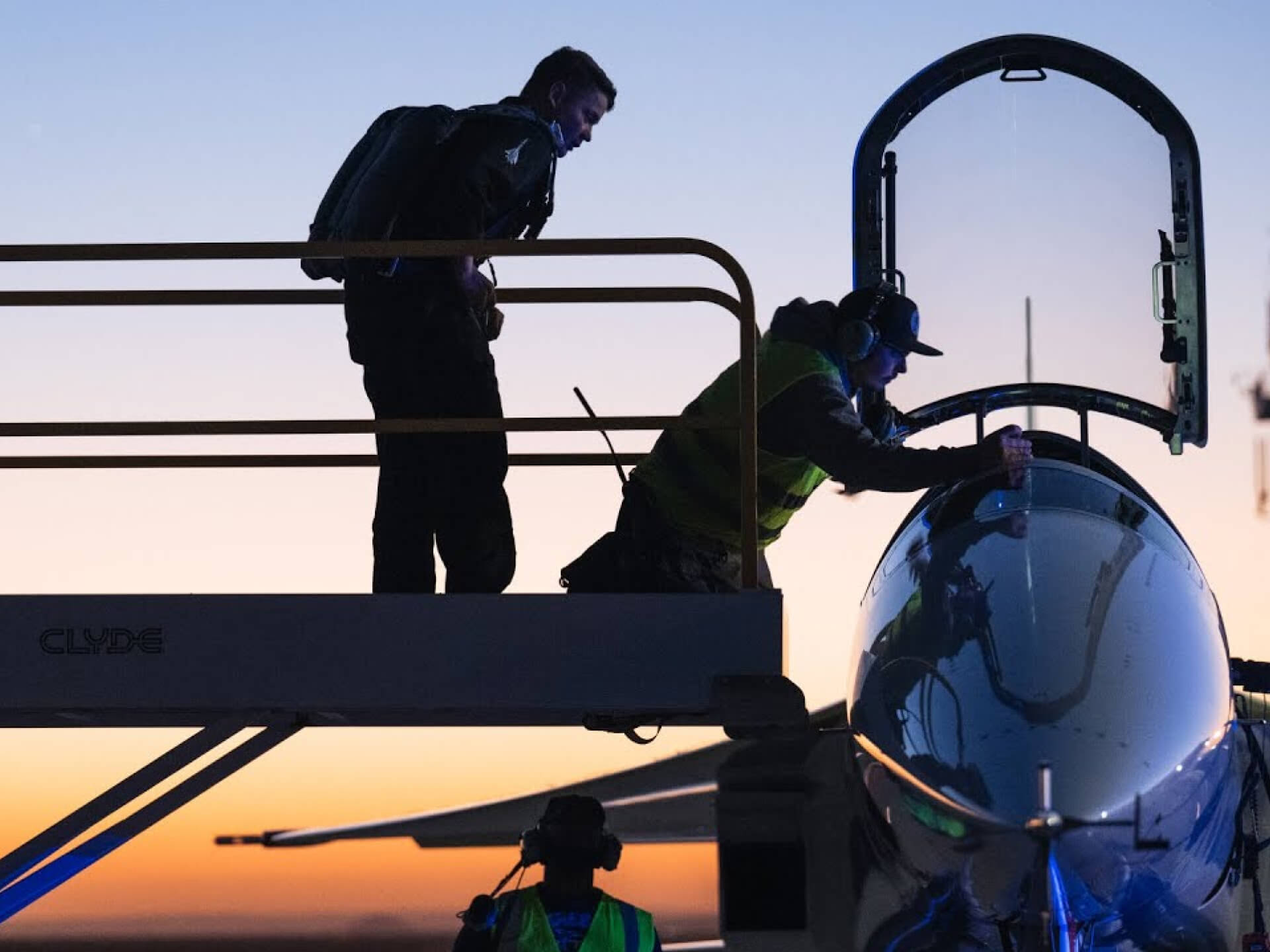
Completed Test Flights
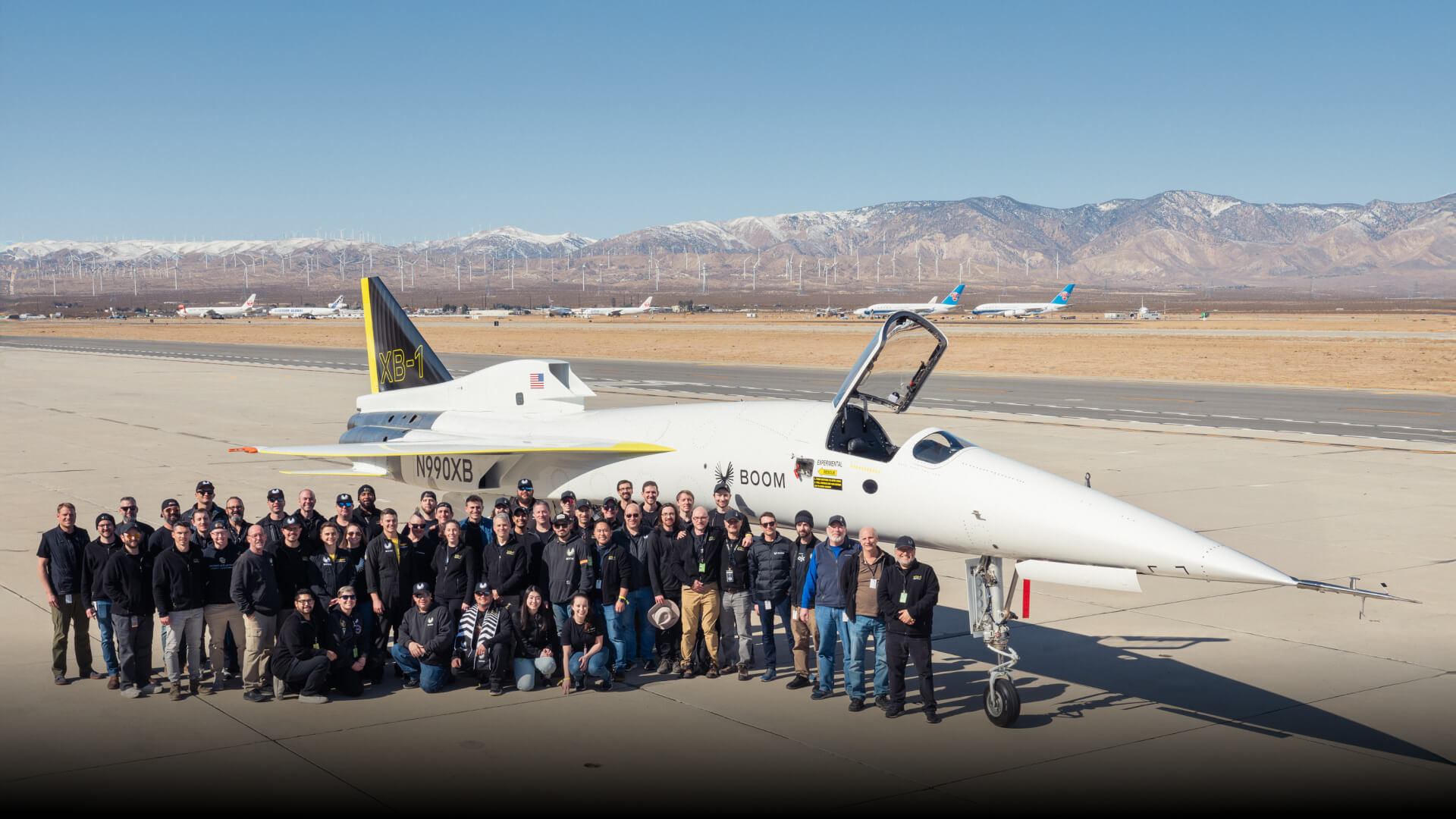
Made in America
Meet the team that built the first American civil supersonic jet.
“XB-1’s supersonic flight demonstrates that the technology for passenger supersonic flight has arrived. A small band of talented and dedicated engineers has accomplished what previously took governments and billions of dollars. Next, we are scaling up the technology on XB-1 for the Overture supersonic airliner. Our ultimate goal is to bring the benefits of supersonic flight to everyone.”
Blake Scholl
FOUNDER & CEO
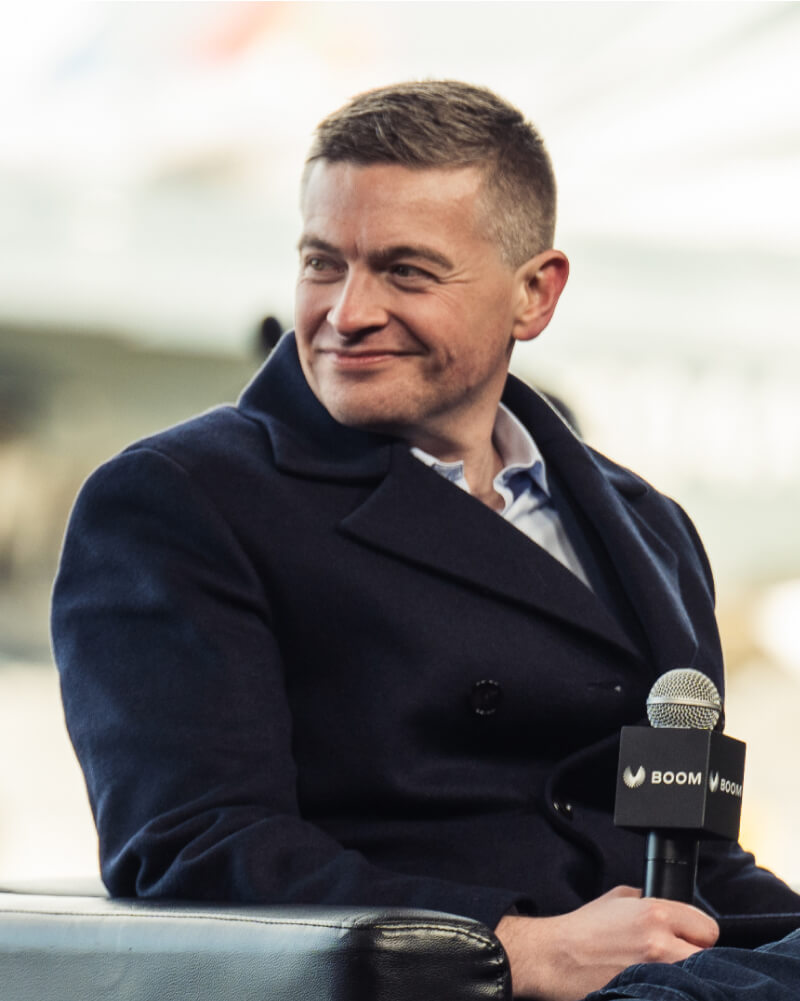
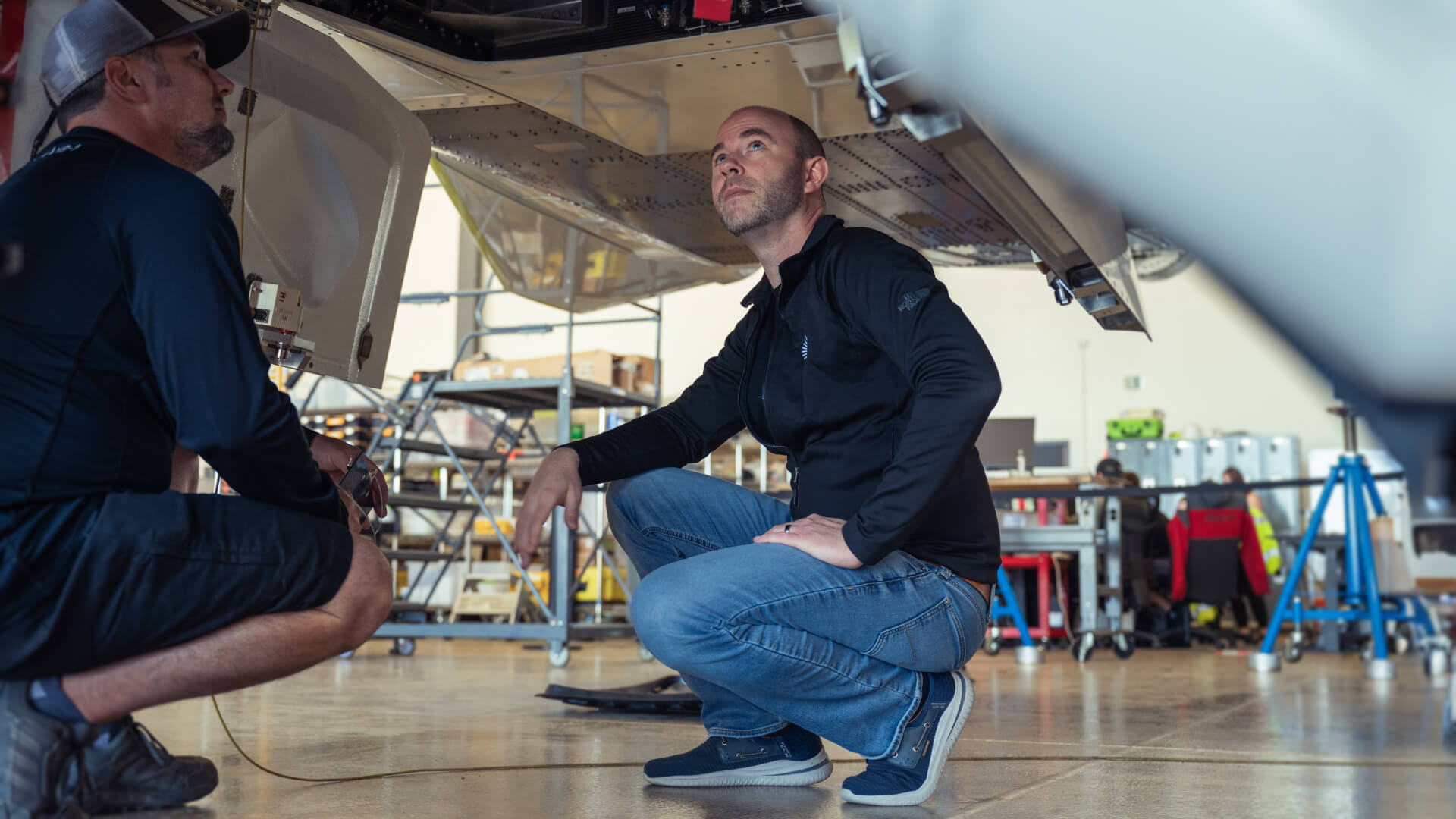
Inside Look at XB-1’s Flight Test Program
XB-1 Chief Flight Test Engineer Nick Sheryka speaks to Boom’s progressive approach to flight testing, which is rooted in the idea that safety is the ultimate mission.
Chief Test Pilot Tristan “Geppetto” Brandenburg
Geppetto is a graduate of the United States Naval Test Pilot School and TOPGUN Adversary. He has completed 2500 total flight hours in 30 different aircraft and executed over 200 carrier arrested landings. He tested new systems on the F/A18 Super Hornet before they were released to the fleet. Geppetto piloted test flights 2-11 and will be at the controls for XB-1’s first supersonic test flight.
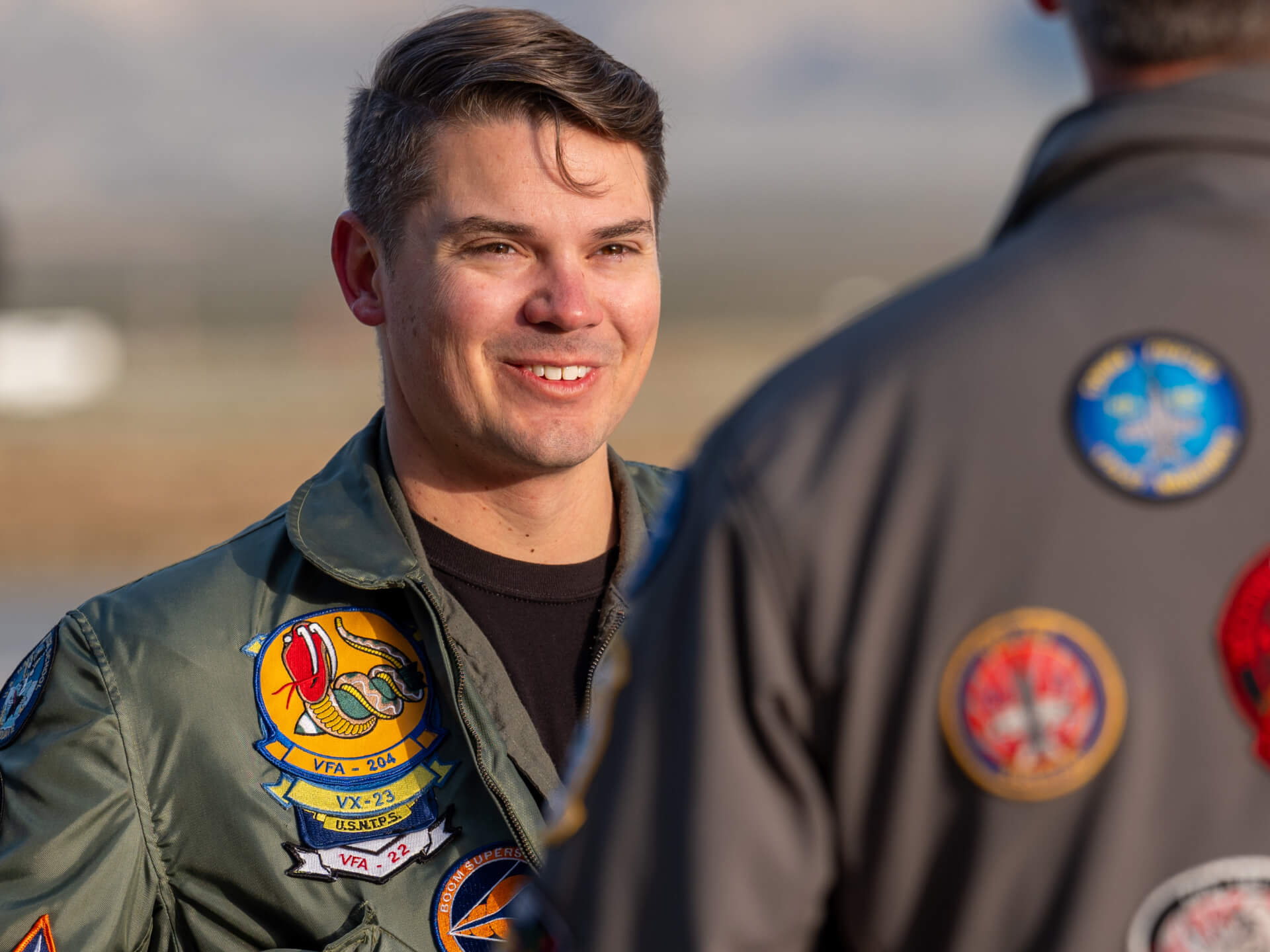
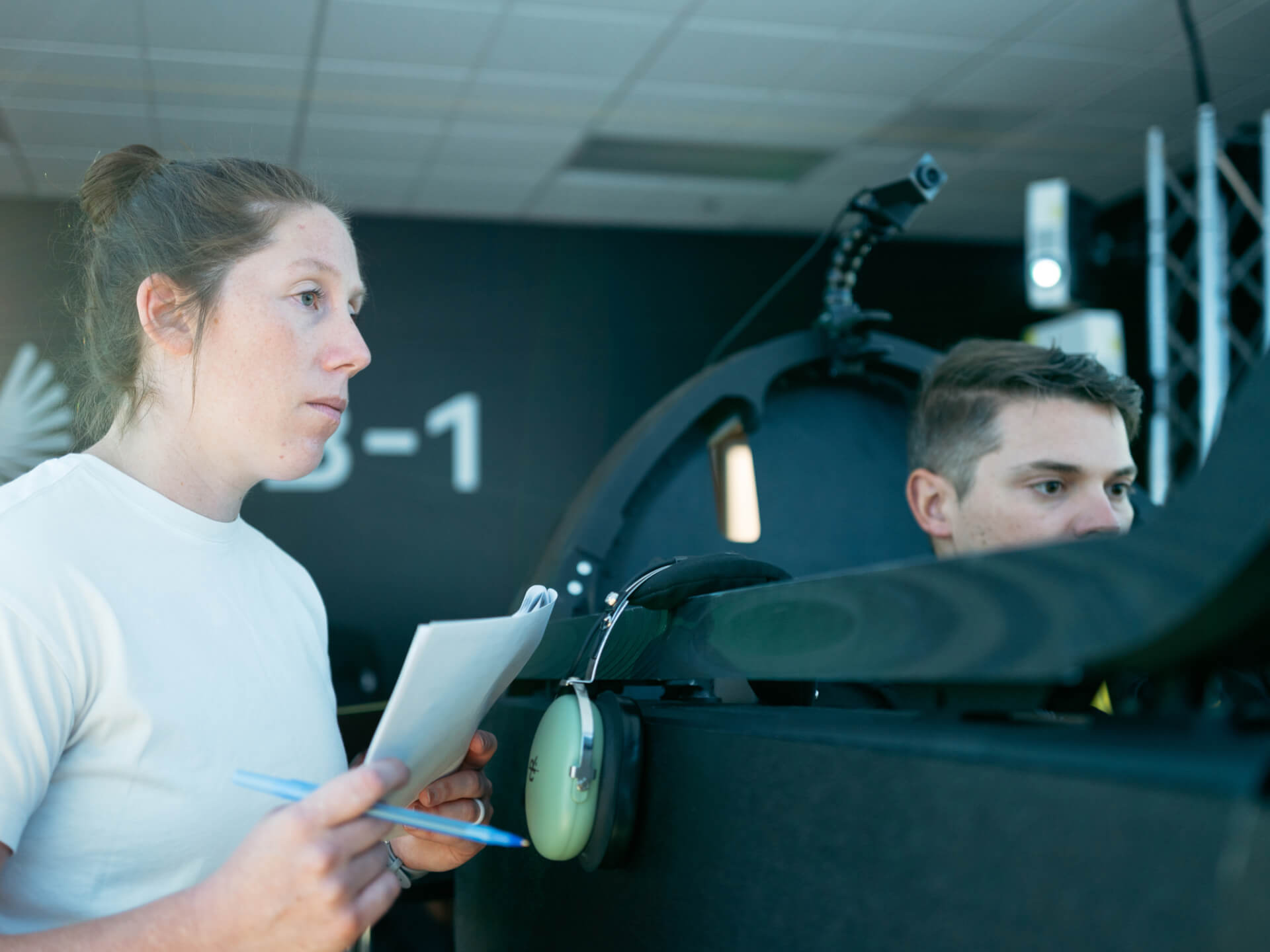
What Happens Between XB-1 Test Flights?
Step into the hangar with Senior Manager of Aircraft Systems Erin Young to learn what happens before XB-1 takes off and after XB-1 returns to the hangar.
When Every Step Matters
Go behind the scenes with Mareguis Killabrew, Boom’s Deputy Crew Chief, as he prepares XB-1—and our team—for safe and optimized test flights.
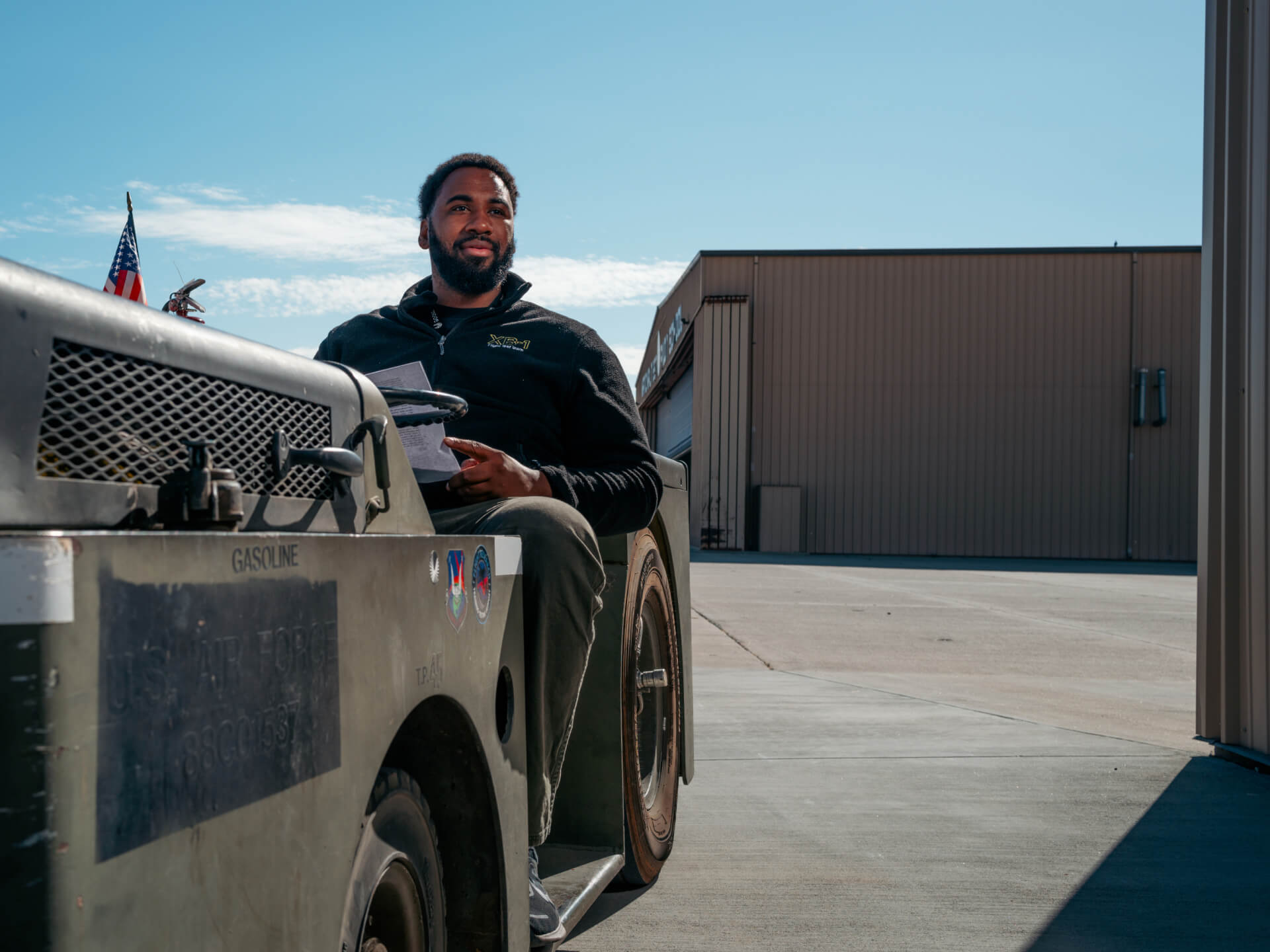
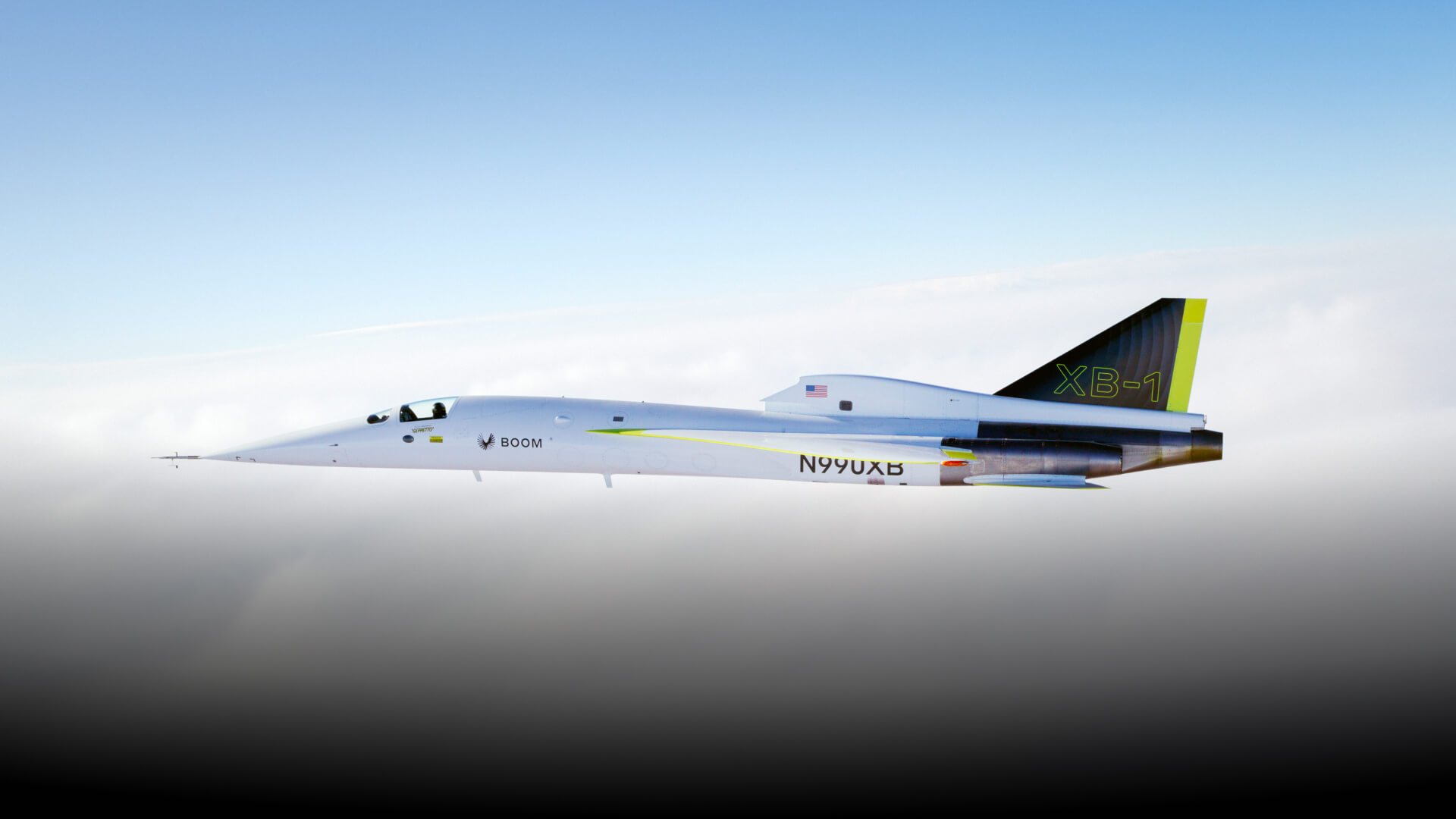
XB-1 Sets the Foundation for Overture
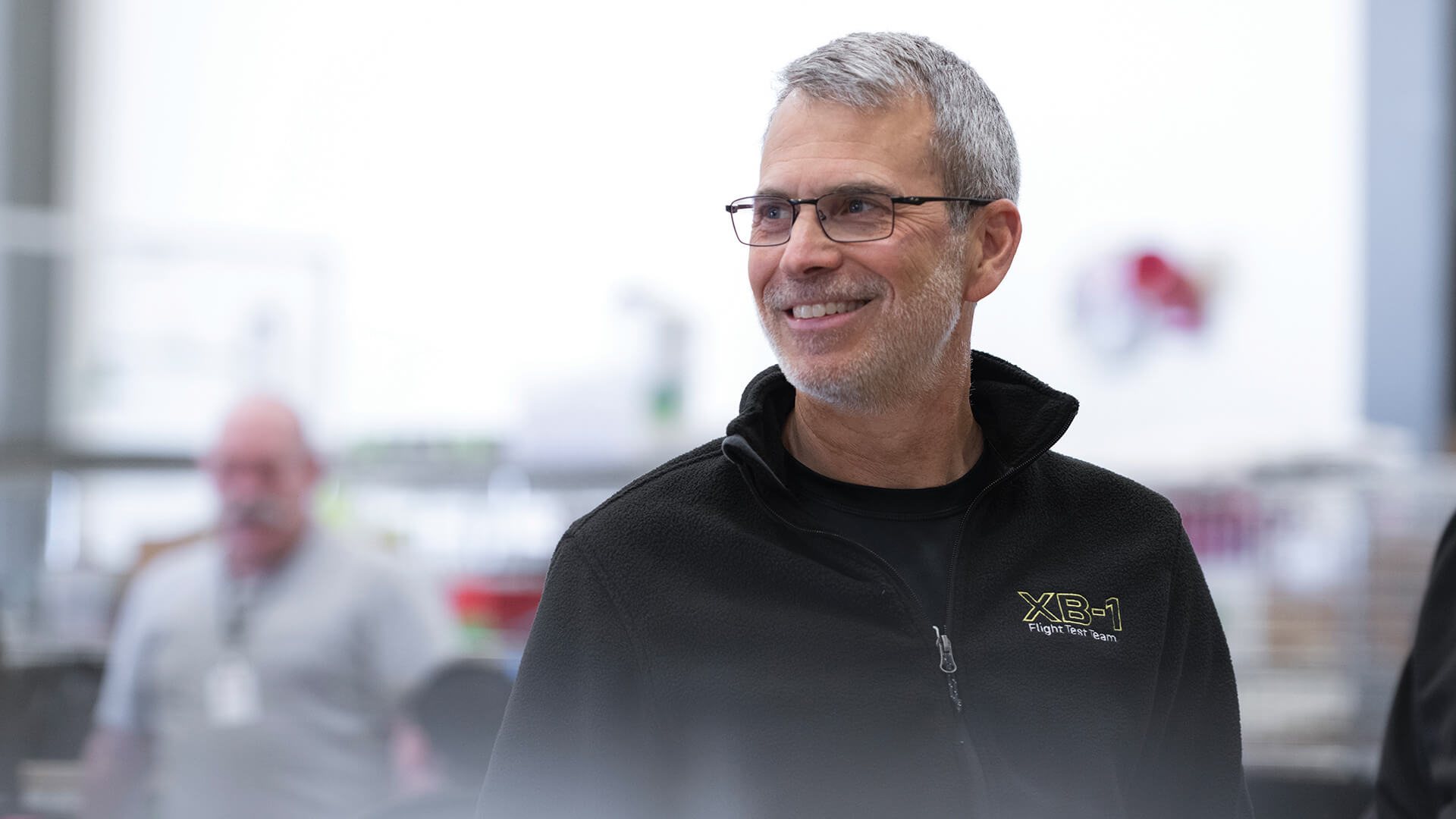
XB-1 and Overture: Two Distinct Aircraft
Explore the connection between XB-1, our supersonic demonstrator, and Overture, our commercial airliner, with Boom’s VP Jeff Mabry.
Returning Civil Supersonic Flight to The Skies
Boom built and flew the first civilian supersonic jet since Concorde and will now scale the learnings to deliver supersonic travel with Overture, cutting travel times in half.
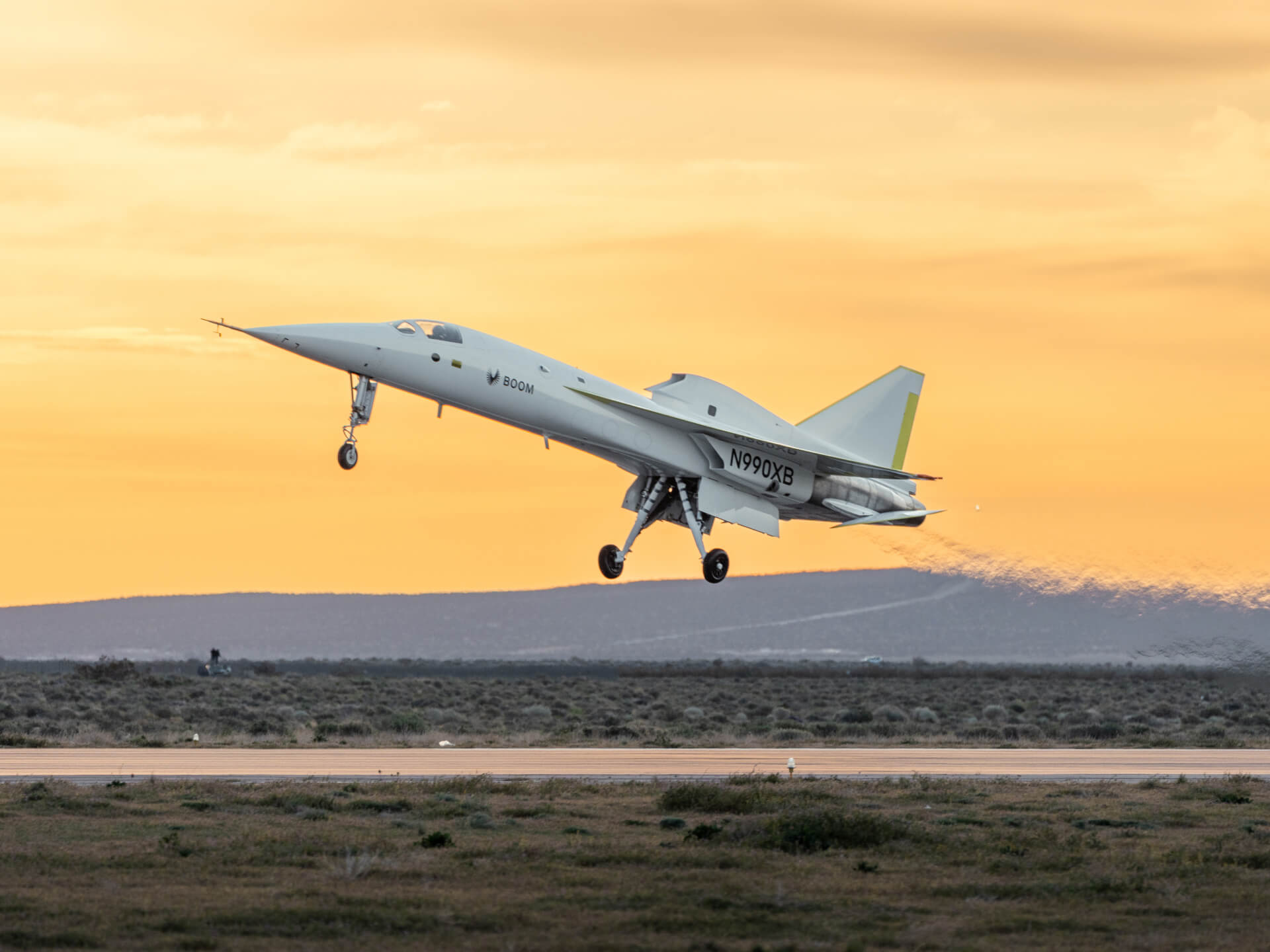
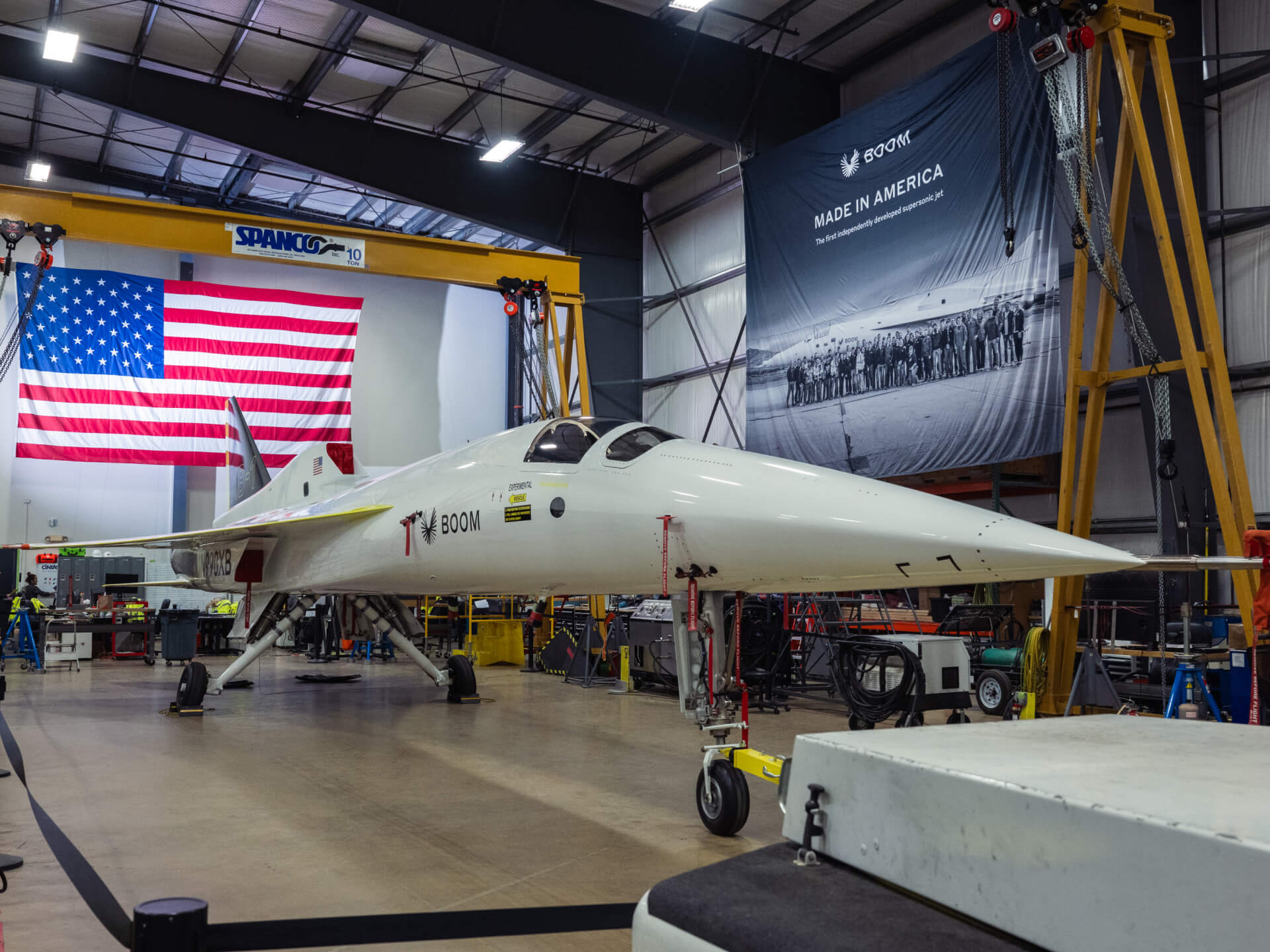
Supersonic Air Travel is Coming
Boom is driving innovation in aviation to ensure American leadership with supersonic air travel.
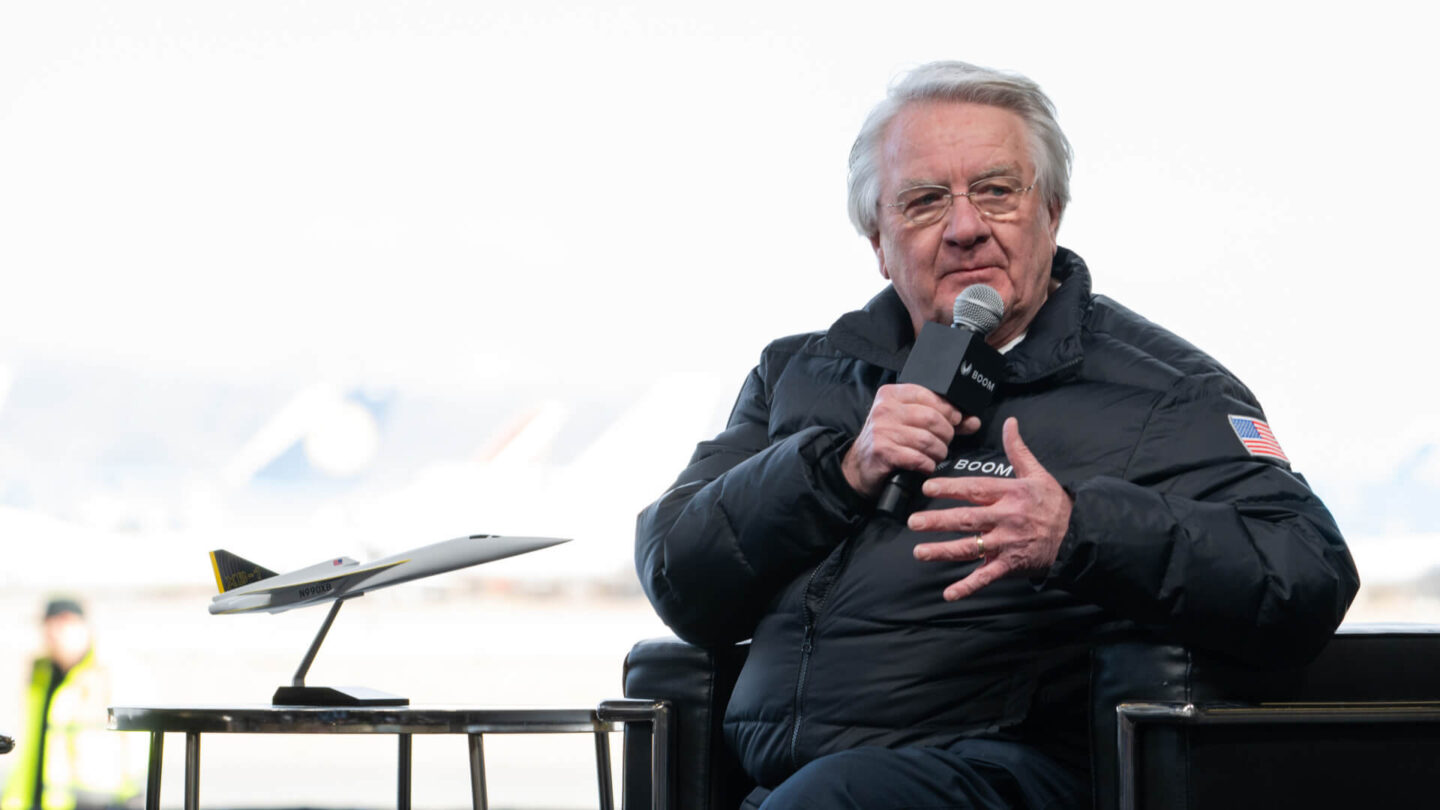
“I’ve been waiting over 20 years for an environmentally friendly successor to Concorde and XB-1’s supersonic flight is a major landmark towards my dreams being realized. When I last flew Concorde in 2003 I knew that this day would come.
The supersonic flight of the XB-1 supersonic demonstrator is a significant achievement toward making sustainable supersonic flight a reality, aboard Overture—my #1 choice as the successor to Concorde. I’m now looking forward to the next big step— the first running of the core of Boom’s ‘Symphony’ engine later this year.
Congratulations to Blake Scholl, all at Boom and especially its pilot, Tristan ‘Geppetto’ Brandenburg. Having been Concorde’s Chief Pilot I envy his role in this exciting return towards mainstream supersonic flight.”Captain Mike Bannister
former Chief Concorde Pilot for British Airways
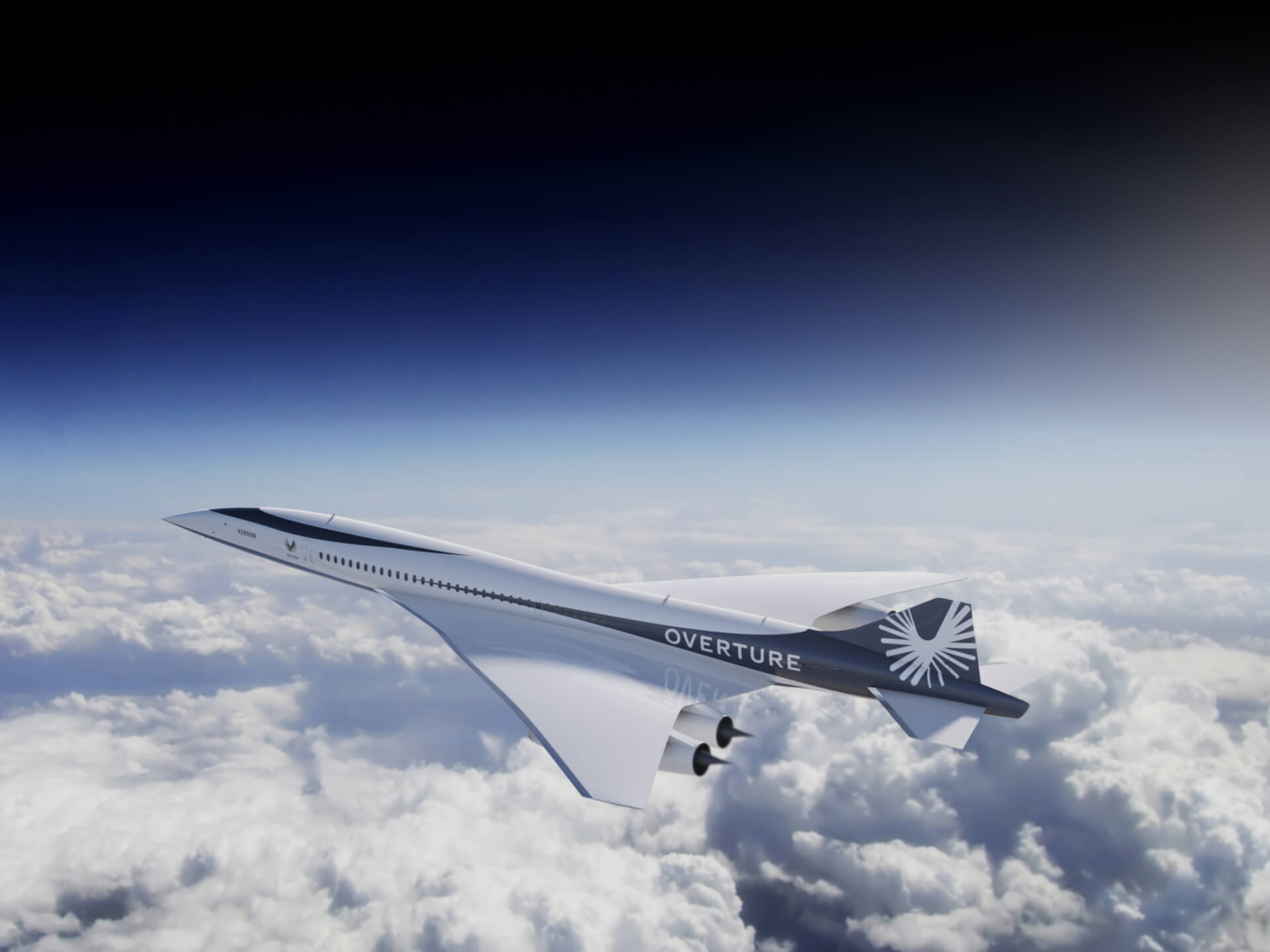
Beyond Mach 1
The XB-1 program has built the foundation for Boom to deliver supersonic travel, onboard Overture.