Chris Taylor, Boom’s vice president of manufacturing, has watched the Overture Superfactory go from groundbreaking to construction site to building completion at the Piedmont Triad International Airport in Greensboro, North Carolina.
The 179,000 square foot Superfactory houses the state-of-the-art assembly line where Boom will build its supersonic airliner, Overture. As the first supersonic airliner factory in the United States, the Superfactory represents a major milestone toward ensuring America’s continued leadership in aerospace manufacturing.
Chris is responsible for developing Boom’s manufacturing facilities and processes and, ultimately, delivering completed aircraft into the flight test program and to Boom’s airline customers.
We caught up with Chris to learn more about the Superfactory and what’s coming next in the first-in-flight state.
What is the current status of the Overture Superfactory, and what’s next?
I am proud to say that construction on the building is complete! We celebrated this milestone with a ribbon-cutting ceremony on June 17, 2024, joined by our construction partners, BE&K, as well as local leaders and elected officials who helped bring this accomplishment to fruition. We have also had great support from the Piedmont Triad International Airport, which is where the campus is located.
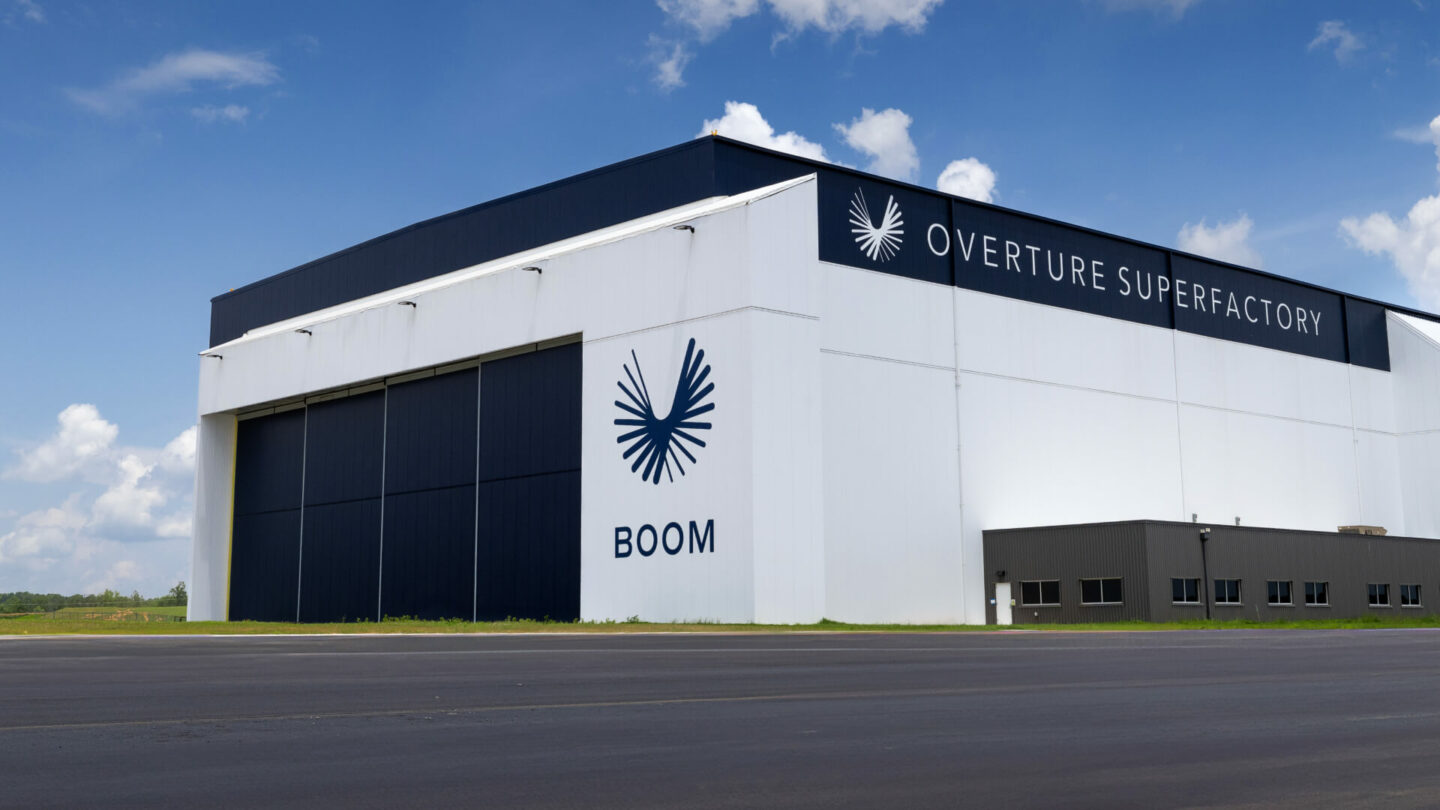
Now that the construction is complete, my team and I will focus on operationalizing the production floor, which includes designing and implementing assembly stations, developing positioning and joining processes, and planning material flow.
I am working in partnership with our tooling supplier, Advanced Integration Technology (AIT), to begin procuring and installing tooling into the Superfactory. The first major piece of equipment to be installed is an advanced test cell unit. The test cell will be used to develop manufacturing processes, optimize the flow of the assembly line, and prepare staff for Overture production. That same unit will become an operational part of the assembly line.
Tell us more about your role at Boom.
I’m responsible for manufacturing and delivering Overture to the flight test team. That begins with building a team to establish processes required to turn design into reality and to execute all those strategies safely with a high degree of quality — on schedule and on time.
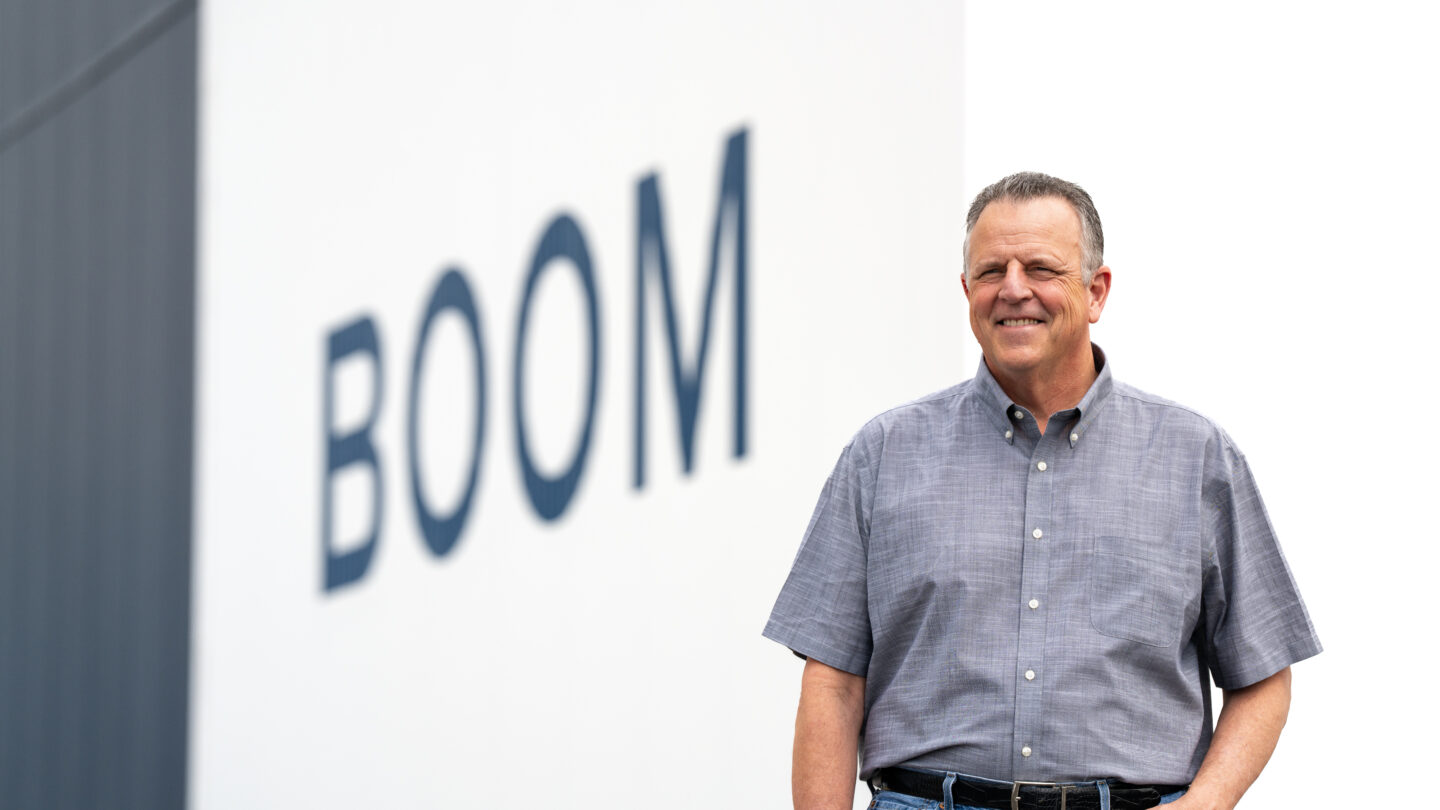
Within 17 months, we went from breaking ground on the site to the completed building that stands today. Now that construction is complete, I will get to spend a lot of time on the manufacturing floor, where I love to be.
I’m very excited to start building out our team in the Triad. The state and local officials in North Carolina are ideal partners for Boom as we build the supersonic future. And, the level of community support showed me immediately that this is the right place to be. There are also hundreds of aerospace companies and suppliers in North Carolina. It’s such a great opportunity for Boom and we are proud to help North Carolina maintain and grow its leadership in the aerospace sector.
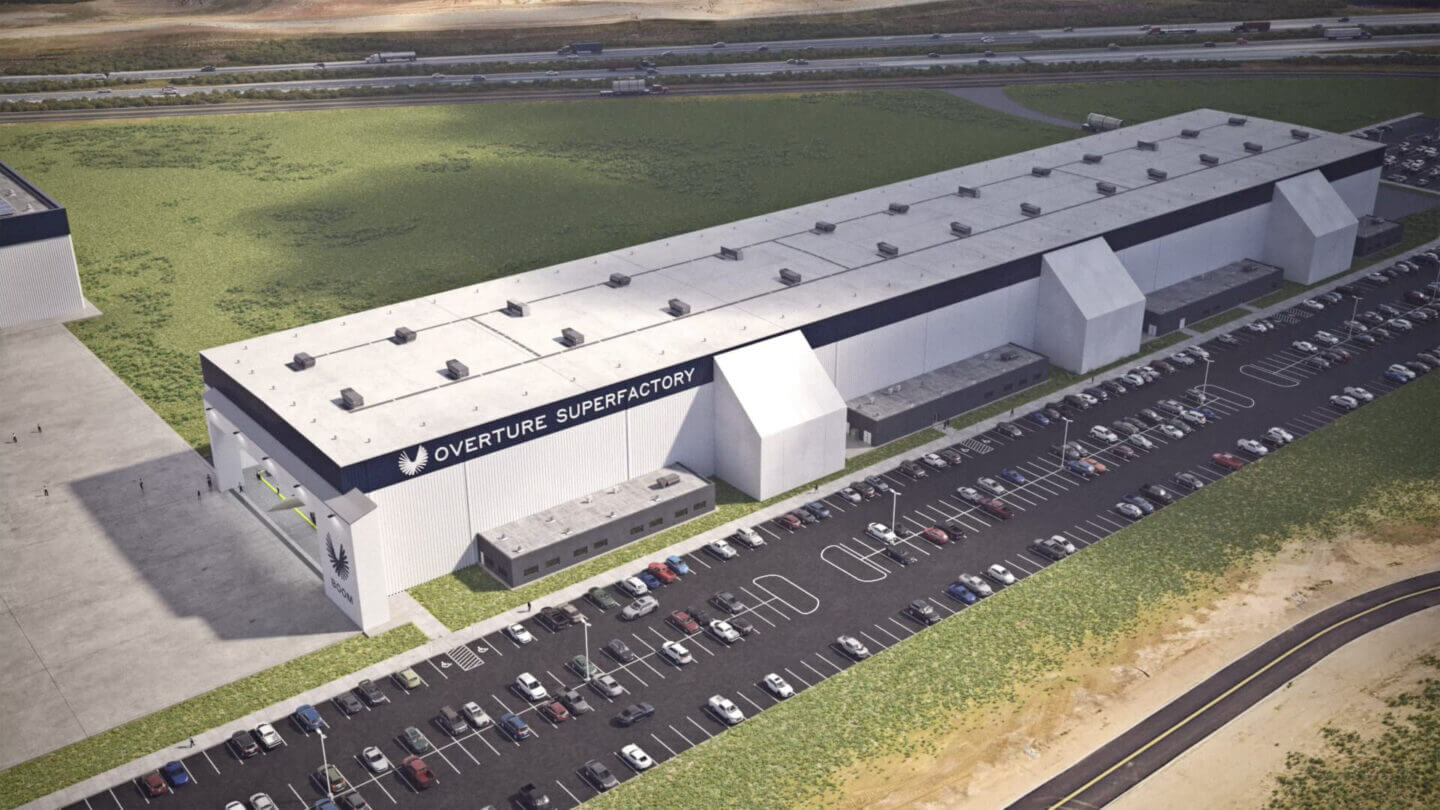
Can you tell us more details about the work that will be done at the Superfactory?
The Overture Superfactory is a 179,000 square foot building, which spans the final assembly line, office space, and miscellaneous areas of the site.
The first assembly line has the capacity to produce 33 Overture aircraft per year. We have plans to build an additional assembly line, scaling to produce 66 supersonic airliners annually. The campus will also include a delivery center where airlines including United, American, and Japan Airlines will receive their supersonic aircraft.
When Overture is ready to begin test flights, that program will also happen here in North Carolina. We like to say that the state that is first-in-flight will also be the first in supersonic flight!
What’s unique or innovative about the Superfactory?
This is the first factory in the United States to produce supersonic airliners. Seeing the building complete is a big step toward the return of supersonic travel – we are literally paving the way.
In order to assure safe operation at supersonic speeds, we will need to be especially focused on the quality of the aircraft. Our tooling system (from AIT) is designed to provide us with precise positioning of all the structural sections, control steps into the airstream, and gaps in the joints. The drilling machine will allow us to monitor and control hole quality to minimize protrusions of fasteners into the airstream that could cause excess drag.
And just as critical as the hardware systems, are the options available for manufacturing execution software systems that we are exploring. These systems enhance our ability to manage the shop floor processes to strengthen product quality. Technicians will have easy access to the engineering models on the shop floor and inside the aircraft. We’ll be able to provide detailed work instructions and incorporate mixed reality into the build process. Automatic data collection from our tools into the manufacturing execution system will allow us to monitor the build as it progresses as well as analyze data from previous builds to track and correct variations more quickly.
What prompted your passion for manufacturing and aerospace?
For me, going into manufacturing was very intentional. I always wanted to work in a factory and find ways to help technicians do their jobs better and to make them feel more empowered in the work they do. That meant supporting the people building the product, whatever that product was.
Going into aviation and aerospace was less intentional. Although I knew I wanted to work in manufacturing before college, I didn’t initially care what the product was. Although maybe I should have known where I would have ended up because as a kid, I built WWII model airplanes as a hobby.
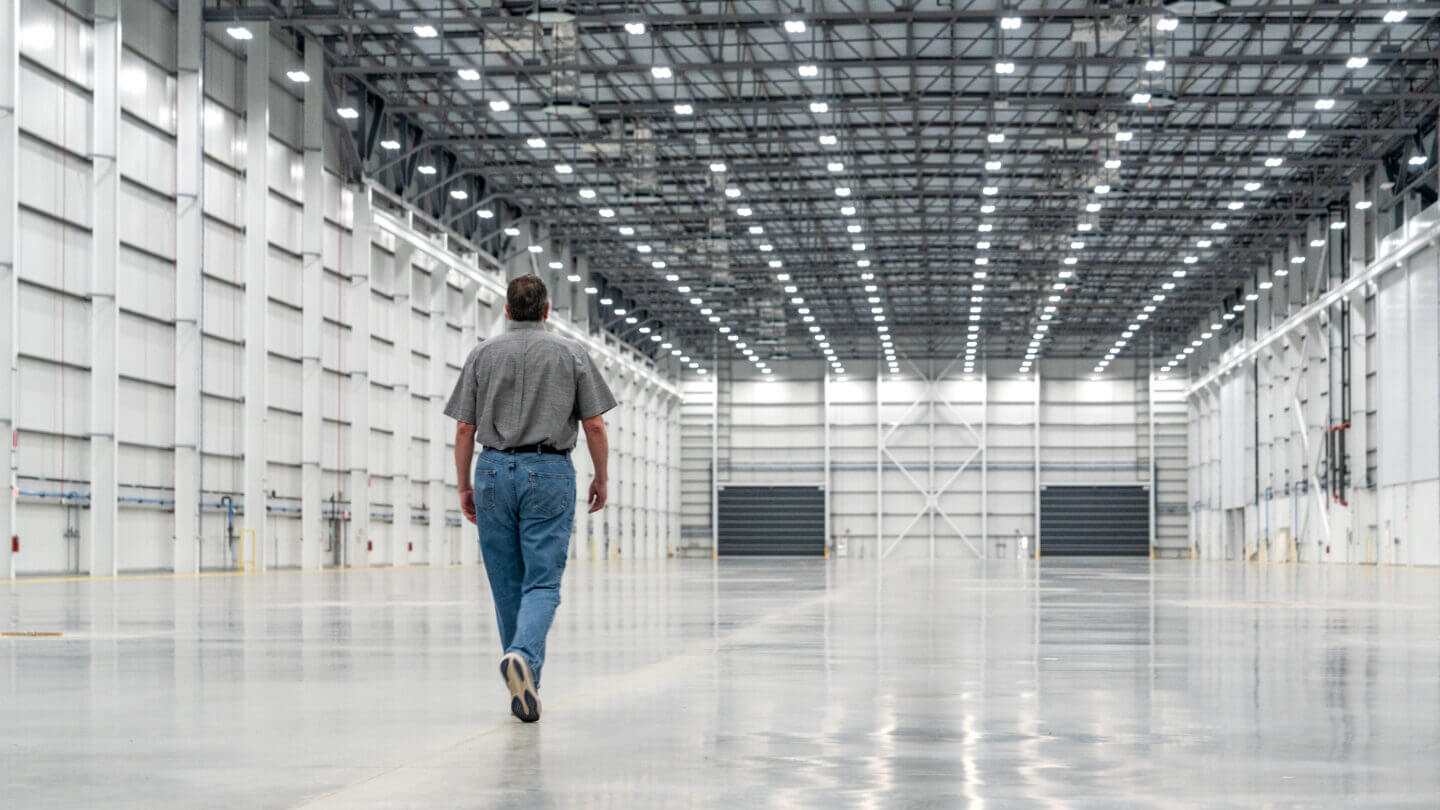
When I was in college at the Georgia Institute of Technology, I joined the co-op program. These exist so college students can get real-world work experience, alongside their classes. Luckily for me, Gulfstream, which was the only aerospace business at the time in my hometown of Savannah, Georgia, was just beginning to participate in the program. I ended up landing a co-op job with Gulfstream and I didn’t leave for nearly four decades. That experience as a co-op student, where I was actually in the tool shop as a toolmaker, immediately showed me I was on the right career path.
What sparked your interest in supersonic, and Boom in particular?
The mission to return civil supersonic aircraft to the skies is inspiring to me.
I am always motivated by wanting to make everything better for people who work in the factory. But I am also motivated by the end product. Even if, over the course of a project, something isn’t going my way, walking out on the factory floor and seeing something incredible being built drives me. It reinforces why I do what I do. The product has to be inspiring — and for me, that’s Overture.